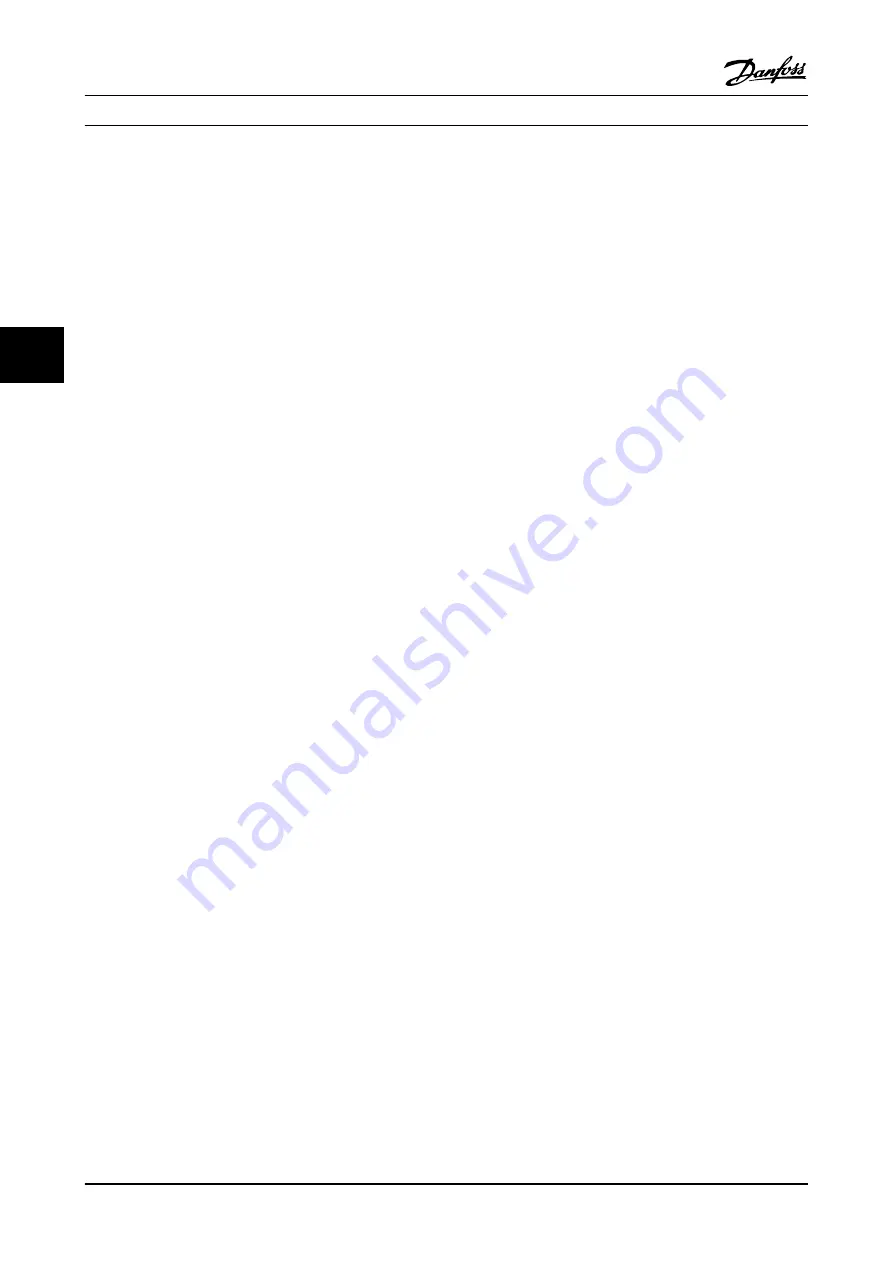
WARNING 47, 24 V supply low:
The external 24 V DC backup power supply may be
overloaded, otherwise contact your Danfoss supplier.
WARNING 48, 1.8 V supply low:
Contact your Danfoss supplier.
WARNING 49, Speed limit:
The speed is not within the specified range in
and
.
ALARM 50, AMA calibration failed:
The motor is not suitable for the particular size of drive. Start
the AMA procedure once again by
, eventually with a reduced AMA function. If
still failing; check the motor data.
ALARM 51, AMA check Unom and Inom:
The setting of the motor voltage, motor current, and motor
power is presumably wrong. Make sure the settings.
ALARM 52, AMA low Inom:
The motor current is too low. Check the settings.
ALARM 53, AMA motor too big:
The motor is too big for the AMA to be carried out.
ALARM 54, AMA motor too small:
The motor is too small for the AMA to be carried out.
ALARM 55, AMA par. out of range:
The motor parameter values found from the motor are
outside the acceptable range.
ALARM 56, AMA interrupted by user:
The AMA has been interrupted by the user.
ALARM 57, AMA timeout:
Try to start the AMA again a number of times, until the AMA
is carried out. Please note that repeated runs may heat the
motor to a level where the resistances Rs and Rr are
increased. In most cases, however, this is not critical.
ALARM 58, AMA internal fault:
Contact your Danfoss supplier.
WARNING 59, Current limit:
The current is higher than the value in
.
WARNING 60, External interlock:
External interlock has been activated. To resume normal
operation, apply 24 V DC to the terminal programmed for
external interlock and reset the adjustable frequency drive
(via serial communication, digital I/O, or by pressing reset
button on keypad).
WARNING/ALARM 61, Feedback Error:
An error between calculated speed and speed measurement
from feedback device. The function Warning/Alarm/
Disabling setting is in
4-30 Motor Feedback Loss Function
Accepted error setting in
4-31 Motor Feedback Speed Error
and the allowed time the error occur setting in
. During a commissioning procedure
the function may be effective.
WARNING 62, Output Frequency at Maximum Limit:
The output frequency is higher than the value set in
. This is a warning in VVC
plus
mode
and an alarm (trip) in flux mode.
ALARM 63, Mechanical Brake Low:
The actual motor current has not exceeded the “release
brake” current within the “Start delay” time window.
WARNING 64, Voltage Limit:
The load and speed combination demands a motor voltage
higher than the actual DC link voltage.
WARNING/ALARM/TRIP 65, Control Card Overtemp:
Control card overtemperature: The cut-out temperature of
the control card is 176°F [80°C].
WARNING 66, Heatsink Temperature Low:
The heatsink temperature is measured as 32°F [0°C]. This
could indicate that the temperature sensor is defect and that
the fan speed has thus increased to the maximum in case the
power part or control card is very hot.
ALARM 67, Option Configuration has Changed:
One or more options has either been added or removed
since the last power-down.
ALARM 68, Safe Stop:
Safe Stop has been activated. To resume normal operation,
apply 24 V DC to T-37. Press reset button on LCP.
WARNING 68, Safe Stop:
Safe Stop has been activated. Normal operation is resumed
when safe stop is disabled. Warning: Automatic Restart!
ALARM 69, Power card temperature
The temperature sensor on the power card is either too hot
or too cold.
Troubleshooting:
Check the operation of the door fans.
Make sure that the filters for the door fans are not
blocked.
Check that the connector plate is properly installed
on IP 21 and IP 54 (NEMA 1 and NEMA 12) drives.
ALARM 70, Illegal FC Configuration:
The current control board and power board combination is
illegal.
ALARM 71, PTC 1 Safe Stop:
Safe Stop has been activated from the MCB 112 PTC
Thermistor Card (motor too warm). Normal operation can be
resumed when the MCB 112 applies 24 V DC to T-37 again
(when the motor temperature reaches an acceptable level)
and when the digital input from the MCB 112 is deactivated.
When that happens, a reset signal must be is be sent (via Bus,
Digital I/O, or by pressing [RESET]).
Troubleshooting
FC 300 Programming Guide
5-8
MG.33.MA.22 - VLT
®
is a registered Danfoss trademark
5
5