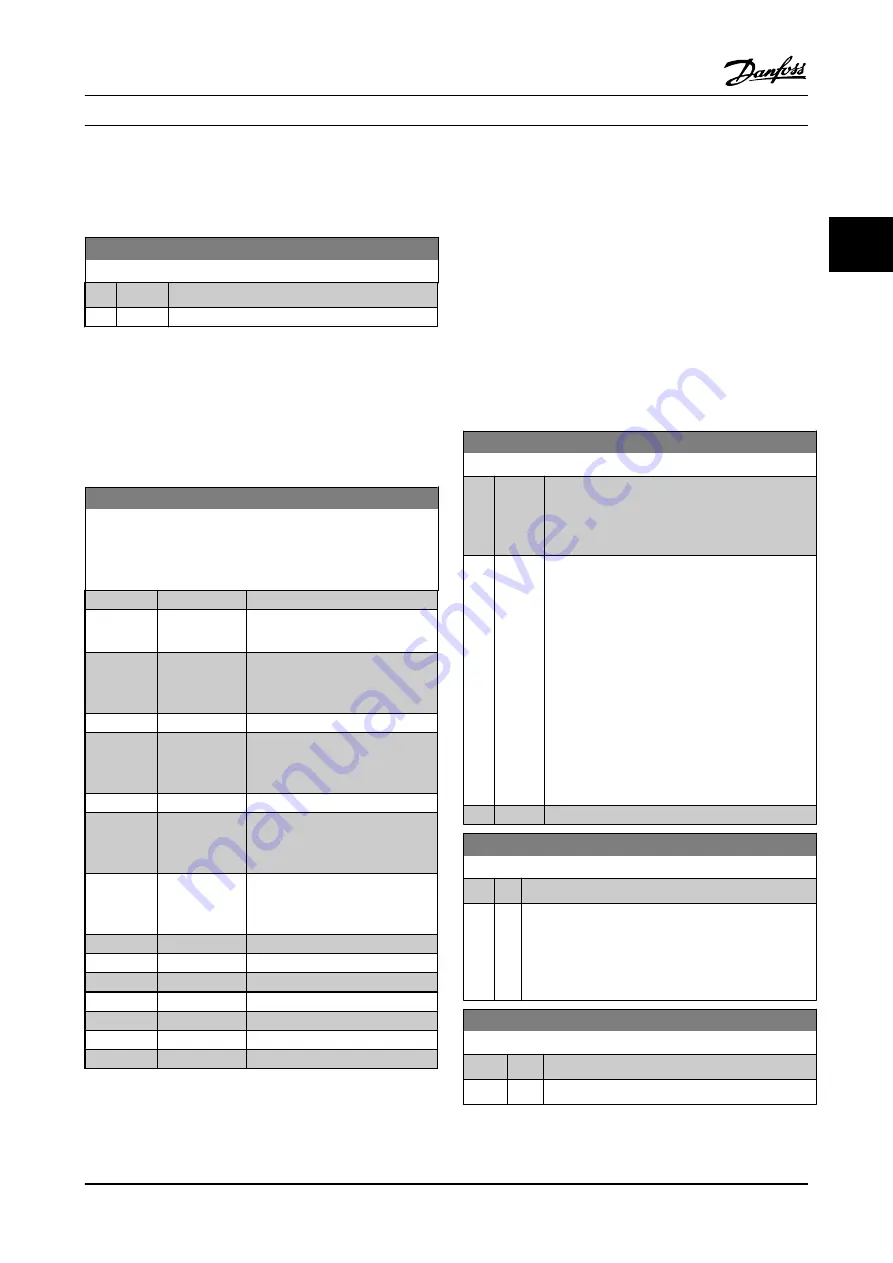
3.15 Parameters:
14-** Special Functions
3.15.1 14-0* Inverter Switching
14-00 Switching Pattern
Option:
Function:
[0]
*
60 AVM
Select the switching pattern: 60° AVM or SFAVM.
[1]
*
SFAVM
NOTE!
The output frequency value of the adjustable frequency
drive must never exceed 1/10 of the switching frequency.
When the motor is running, adjust the switching frequency
in
4-11 Motor Speed Low Limit [RPM]
until the motor is as
noiseless as possible. See also
and
the section
Special conditions
in the FC 300 Design Guide.
14-01 Switching Frequency
Select the inverter switching frequency. Changing the switching
frequency can help to reduce acoustic noise from the motor.
Default depend on power size.
Option:
Function:
[0]
1.0 kHz
[1]
1.5 kHz
Default switching frequency for
500–1600 hp [355–1200 kW], 690 V
[2]
2.0 kHz
Default switching frequency for
350–1075 hp [250–800 kW], 400 V
and 50–450 hp [37–315 kW], 690 V
[3]
2.5 kHz
[4]
3.0 kHz
Default switching frequency for 25–
50 hp [18.5–37 kW], 200 V and 50–
150 hp [37–200 kW], 400 V
[5]
3.5 kHz
[6]
4.0 kHz
Default switching frequency for
7.5–20 hp [5.5–15 kW], 200 V and
15–40 hp [11–30 kW], 400 V
[7]
*
5.0 kHz
Default switching frequency for
0.34–5 hp [0.25–3.7 kW], 200 V and
0.5–10 hp [0.37–7.5 kW], 400 V
[8]
6.0 kHz
[9]
7.0 kHz
[10]
8.0 kHz
[11]
10.0 kHz
[12]
12.0 kHz
[13]
14.0 kHz
[14]
16.0 kHz
NOTE!
The output frequency value of the adjustable frequency
drive must never exceed 1/10 of the switching frequency.
When the motor is running, adjust the switching frequency
in
4-11 Motor Speed Low Limit [RPM]
until the motor is as
noiseless as possible. See also
and
the section
Special conditions
in the VLT AutomationDrive FC
300 Design Guide.
NOTE!
Switching frequencies higher than 5.0 kHz lead to automatic
derating of the maximum output of the adjustable frequency
drive.
14-03 Overmodulation
Option:
Function:
[0]
Off
Select
Off
[0] for no overmodulation of the output
voltage, in order to avoid torque ripple on the
motor shaft. This feature may be useful for
applications such as grinding machines.
[1]
*
On
Select On [1] to enable the overmodulation
function for the output voltage. This is the right
choice when it is required that the output current is
higher than 95% of the input current (typical when
running oversynchronously). The output current is
increased according to the degree of overmodu-
lation, up to 103% of the input current.
Overmodulation leads to increased torque ripple as
harmonics are increased.
Control in FLUX mode provides an output current of
up to 98% of the input current, regardless of par.
14-03.
[2]
Optimal
14-04 PWM Random
Option:
Function:
[0]
*
Off
No change of the acoustic motor switching noise.
[1]
On
Transforms the acoustic motor switching noise from a
clear ringing tone to a less noticeable ‘white’ noise. This
is achieved by slightly and randomly altering the
synchronism of the pulse width modulated output
phases.
14-06 Dead Time Compensation
Option:
Function:
[0]
Off
No compensation.
[1]
*
On
Activates dead time compensation.
Parameter Descriptions
FC 300 Programming Guide
MG.33.MA.22 - VLT
®
is a registered Danfoss trademark
3-119
3
3