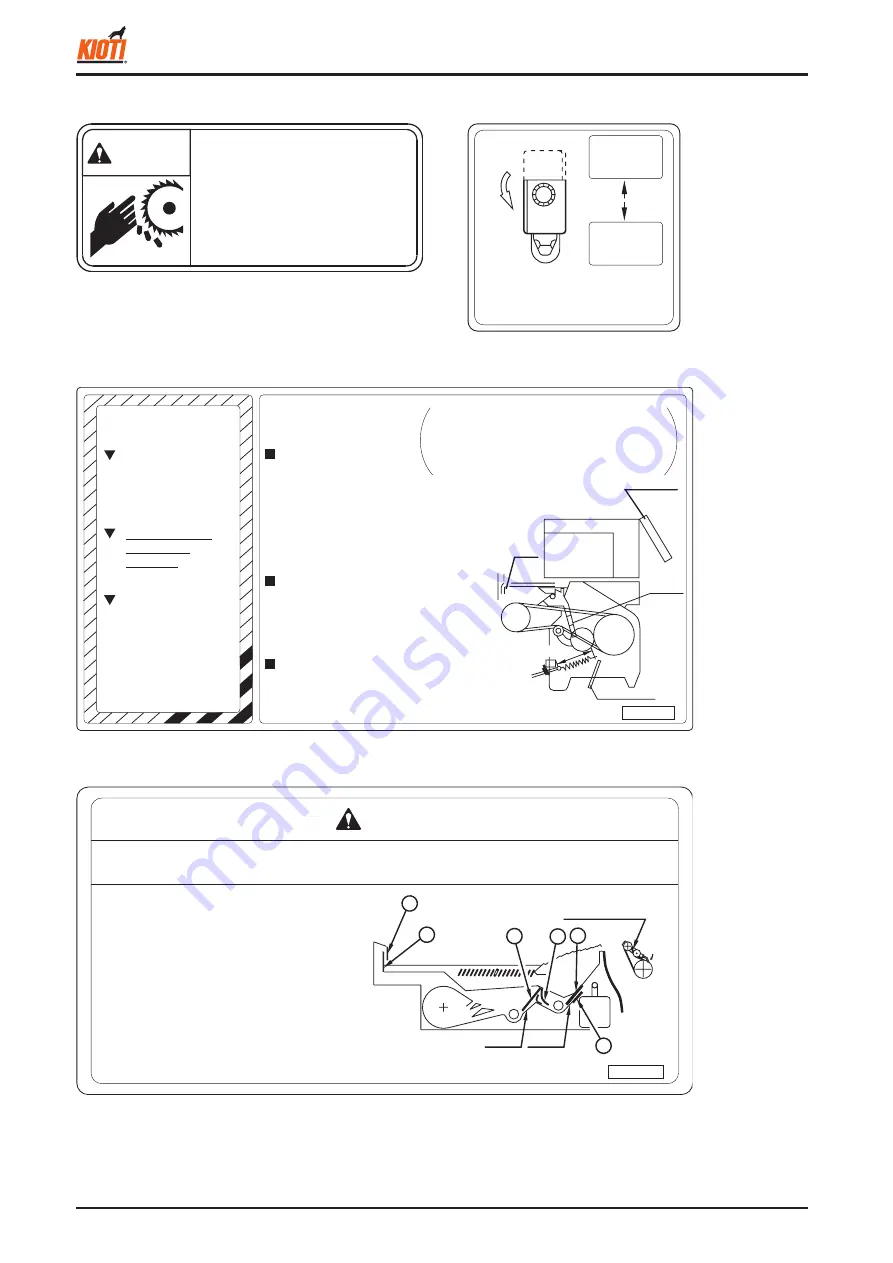
0
-28
Apr. 2007
DSC48
Warning
C7343-64371
Under the cover is a cutter with
sharp blade. Extremely
dangerous! This cover must be
in place especially when the
cutter is rotating to prevent
injuries.
When installing the chaff container, the rubber plate must be installed as specified in the following
figure. Otherwise, the container will easily be damaged.
1. After assembling the chaff container, put 1
under 2, place 3 into the first chaff container,
put 4 and 5 into the second chaff container.
And adjust them through a cleaning port.
Place 6 behind 5 and fasten it. Pull up 1
over the threshing rotor. And remove the
screen to adjust it.
2. Fasten the tensioner.
Oscillatiing tension
Sieve case
PULL
Case 1
Case 2
C7331-64221
Caution
6
2
3
4
5
1
+
+
18. Label C7311-43271
19. Label C7341-55131
17. Label C7343-64371
20. Label C7331-64221
For the LOCK position,
secure fasten the plate.
F
A
STENING
Unlock
(Operation)
Up
Down
Lock
(Adjustment)
C7341-55131
Before adjusting or
cleaning up the
cutter, shut off the
engine first.
Do not touch the
cutter during
operation.
When replacing the
cutter blade,
replacement should
be accurately
performed.
Open the cutter
1. Take out the belt cover.
2. Open the grain side cover.
3. Pull the control lever and remove the
belt.
4. Pull the tension lever forward and
slowly rotate it.
5. With a proper bar, support the cutter.
Close the cutter
1. Repeat the above steps in the
reversed order.
2. Accurately place the tension lever.
3. Do not put the belt inside out.
When replacing the cutter blade, follow
this manual. (Ensure that the sharpened
blade is downward (toward the grain)).
Use only genuine Daedong blades.
Caution
How to open the cutter
Caution 1. Do not open or close the cutter
on a slope.
2. Pay close attention to the blade.
3. First, open the left cover.
Control
lever
Tension lever
Upper cover
Support
bar
165mm
Содержание DSC48
Страница 1: ...DSC48 COMBINE HARVESTER WORKSHOP MANUAL...
Страница 2: ......
Страница 4: ......
Страница 6: ......
Страница 8: ......
Страница 38: ...MEMO...
Страница 40: ......
Страница 106: ......
Страница 136: ...MEMO...
Страница 138: ......
Страница 140: ......
Страница 160: ...MEMO...
Страница 162: ......
Страница 196: ...MEMO...
Страница 198: ......
Страница 216: ......
Страница 251: ...Apr 2007 7 11 DSC48 2 3 WIRING DIAGRAM 417W717A...
Страница 262: ...7 22 Apr 2007 DSC48 4 3 WIRING DIAGRAM 417W723A...
Страница 281: ...417W758B B ON GND B GND 7 2 CIRCUIT DIAGRAM Apr 2007 7 41 DSC48...
Страница 282: ......
Страница 285: ...DSC48 INDEX...