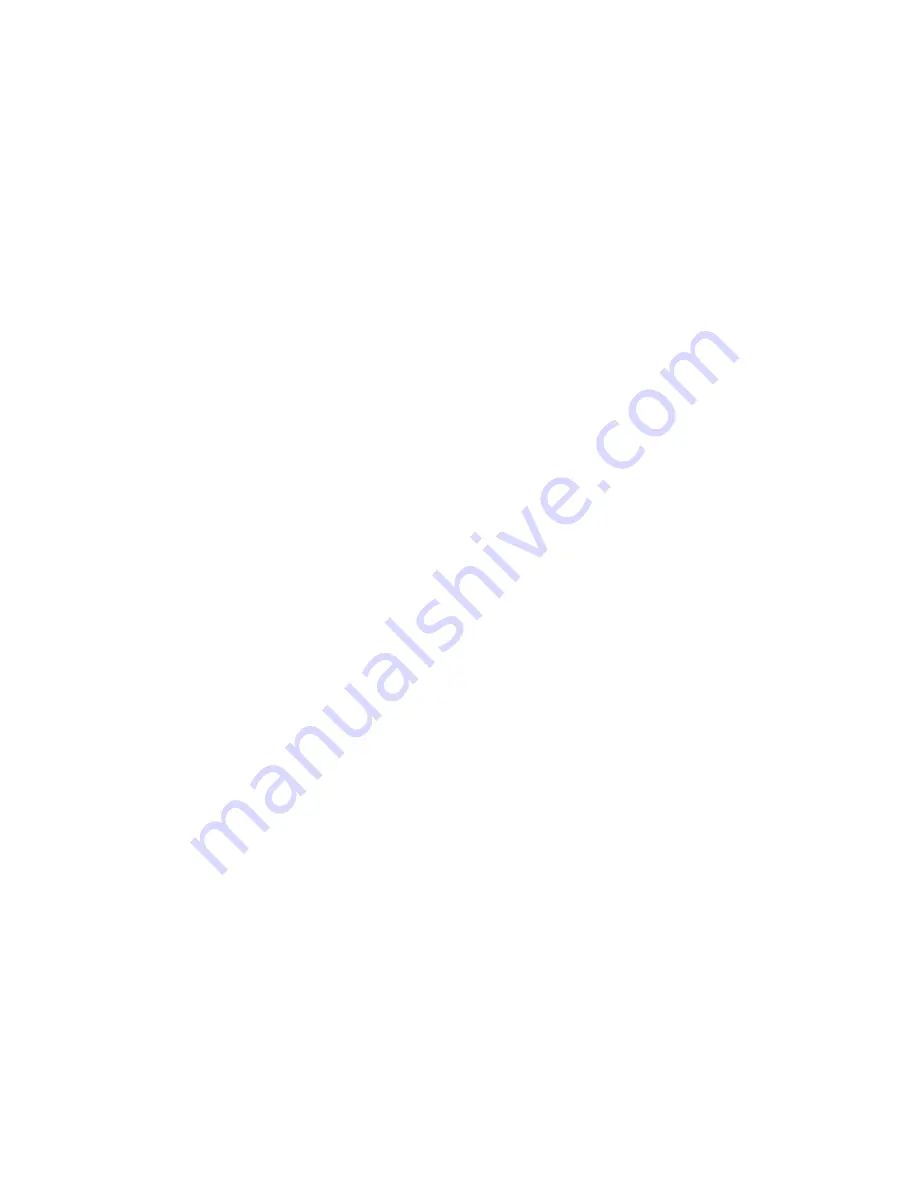
CI-154 User’s Manual
Page 73
monitoring is about risk assessment, and only general guidelines can be given for
monitoring. Fundamental to this is to understand why you are monitoring for particle
counts.
To assess the risks you have to identify which products or processes are critical and
select those for more frequent monitoring. For example, if you package liquid
medication, those points should be monitored where the container or the medication
are exposed to ambient air. However, if it is known or demonstrated that the fill
process generates airborne droplets of the medication, the monitoring point should
be far enough away from the fill point that unevaporated droplets are not entrained
into the particle counter; this is best determined empirically.
If no critical process or product can be identified, then you should identify typical
points in the room that characterize the overall level of contamination in the room.
Setting a sample probe at the output of the HEPA filter does not help assess the
room, and selecting a point that is conveniently out of the way will not reflect the
room in general. Select points that are typical of the activity in the room, and select
a number of locations appropriate for the size of the room; two or three points in a
large room might not reflect all areas of activity in the room.
Characterizing the room
Activities in the room may require daily monitoring or continual monitoring,
depending on the criticality of the activity, but additional monitoring at less frequent
intervals will provide a better understanding of the dynamics of the room, and this
data could help isolate a problem that might develop at some future date.
When people are moving about in the room and machinery is operating, particles
are stirred up into the air and new particles are generated. It would be valuable to
know the typical at rest counts for key locations in the room, and to monitor those
at rest locations monthly to spot any changes in the room that are unrelated to
activities in the room. This will help identify leaks in the ducts or filtration system.
Knowing what is typical during activity, and watching for deteriorating trends will
identify malfunctions in equipment or lax controls related to the staff.
5.2.2
5.2.2 Mo
n
itoring hot air sources
One of the processes that has to be monitored in some applications is the hot air in
an oven or other device that produces very elevated temperatures. Temperatures
high enough to collapse plastic sample tubes (such as Bev-A-Line™ or Tygon™) can
potentially damage the particle counter, and should be cooled down before applying
the air sample to the particle counter. The recommended method is to use the
cooling affect of a length of stainless steel tubing—about ten feet or longer—with a
½” inch ID. Some users have added a coiled section that is placed in a water bath.
The problem is that the water bath may cool the air too much for the water content
of the air being sampled. This brings the air below the dew point, resulting in
condensation. Since particle counters can detect water droplets, this can result in
unexpectedly high counts. It can also result in water collecting inside the sensor.
The temperature of the air exiting the stainless steel extension should be less than
100ºF (38º C).
Содержание CI-154
Страница 2: ...CI 154 User s Manual Page ii ...
Страница 4: ...CI 154 User s Manual Page iv ...
Страница 9: ...CI 154 User s Manual Page ix FRONT VIEW OF CI 154 ...
Страница 10: ...CI 154 User s Manual Page x REAR PANEL OF CI 154 ...
Страница 16: ...CI 154 User s Manual Page 6 ...
Страница 18: ...CI 154 User s Manual Page 8 ...
Страница 80: ...CI 154 User s Manual Page 70 ...
Страница 84: ...CI 154 User s Manual Page 74 ...
Страница 92: ...CI 154 User s Manual Page 82 ...
Страница 96: ...CI 154 User s Manual Page 86 ...
Страница 98: ...CI 154 User s Manual Page 88 ...