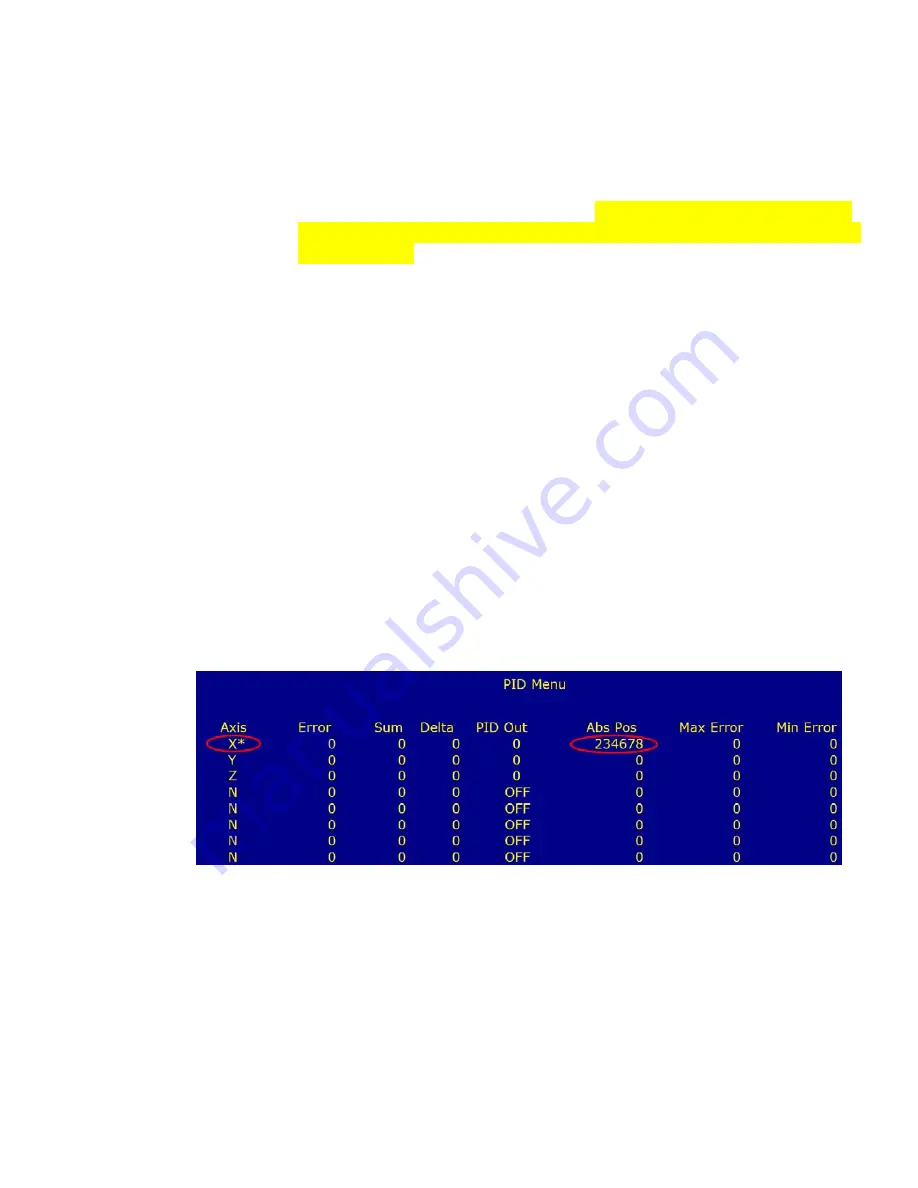
Appendix B: Troubleshooting Motion and Encoder Issues
Symptom or Error
Motion is not smooth
4. Have the motors been tuned in the control?
Before doing any tuning in the control, it is recommended that the servo
amplifier be set back to it's default configuration and, if supported, run
the auto-tuning procedure included with the software provided with the
manufacturer of your servo amplifier. Under no circumstances should
the Centroid auto-tune procedure be run with 3
rd
party servo amplifiers
and/or motors.
After you have configured and tuned your servo amplifier and you have
smooth motion while running the axis from the servo amplifier software,
begin tuning the axis in CNC11 by following Centroid Tech Bulletin 234
which is available here ###.
Symptom or Error
Axis does not move
1. Are your encoder counts per motor rev set correctly?
the correct distance
The encoder counts per motor rev setting is a fixed value and does not
get changed to adjust the distance that the motor travels with a given
command. To determine the number of encoder counts per revolution of
the motor, enter the PID screen and rotate the motor until the asterisk
appears next to the axis label as shown in the below. Note the value of
“Abs Pos”, rotate the motor shaft exactly 1 revolution until the asterisk
again appears next to the axis label again and note the new Abs Pos.
Subtract the two, the result is the number of encoder counts per motor
revolution for that axis. To get to the PID screen from the main screen
press: F1-Setup
→
F3-Config, pw = 137, press enter
→
F4 PID
Содержание GPIO4D
Страница 38: ...16 Wiring Auxiliary Sub systems 3 Spindle Wiring Spindle Contactor Wiring...
Страница 39: ...16 Wiring Auxiliary Sub systems 4 Spindle Inverter Wiring AutomationDirect GS2...
Страница 59: ...12 Counts differ on homing 13 Option not available 14 Parameter missing 15 Position error 16 FPWOM...