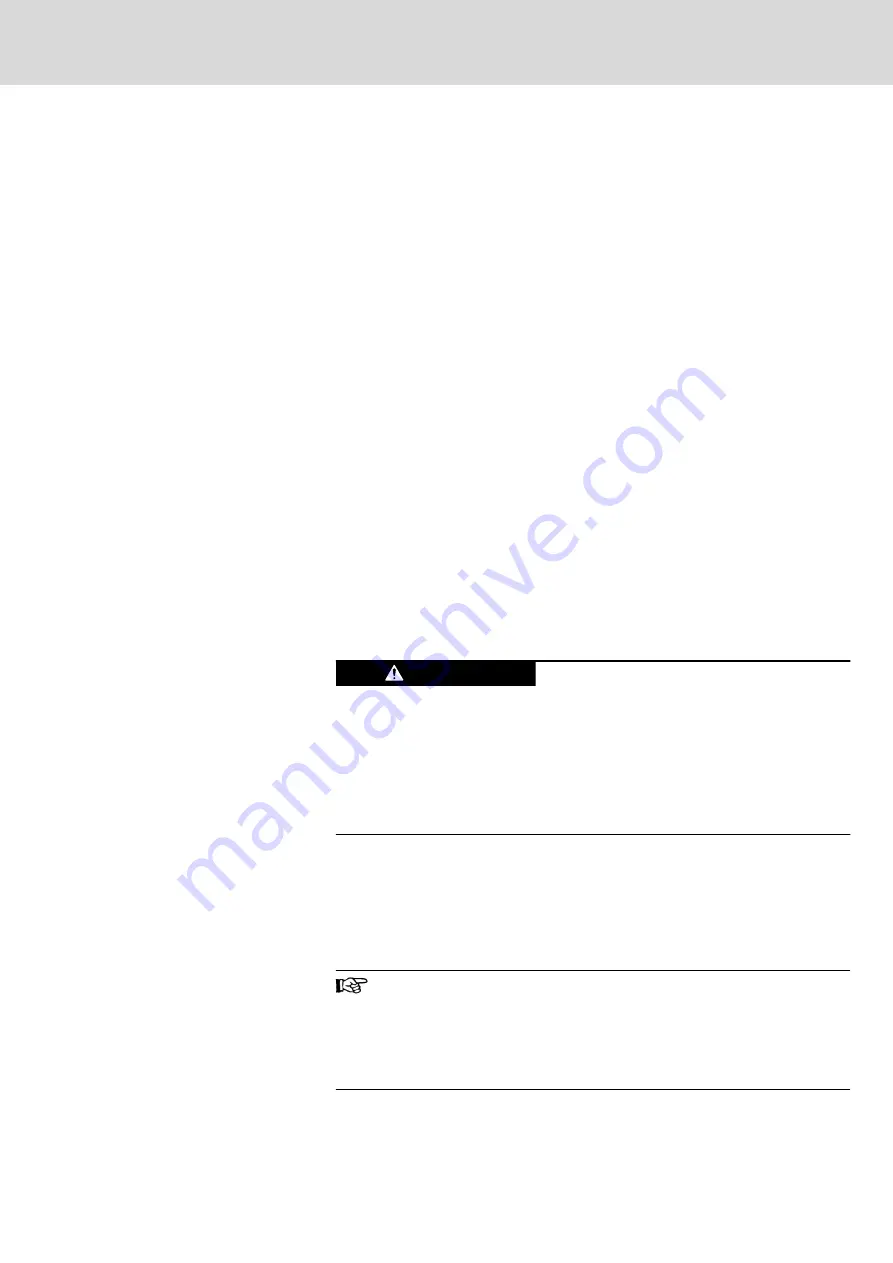
Wait 30 minutes to allow discharging before you start replacing the com‐
ponent.
4. Verify zero potential
5. Dismount defective component
6. If available: Write down address selector switch positions of the defec‐
tive component
7. If available: Remove cover from slot X107 of defective component and
take out programming module
8. If available: Set address selector switch of new component like the one
of defective component
9. If housing of new component is dirty: Clean housing
10. When carrying out the next step, take care that dirt and moisture are
prevented from penetrating the inside of the housing.
If available: Remove cover from slot X107, plug programming module of
defective component in slot X107 of new component, check sealing ring
of cover for damage (if sealing ring damaged: provide new sealing ring),
mount cover (screw tightening torque: 1 Nm)
11. Mount new component
12. Connect new component according to machine circuit diagram
13. Switch on 24V supply
14. Put machine into ready-for-operation state again according to machine
manufacturer's instructions
15. Check functions of drive
11.4.5
"Release holding brake" service function
Lethal injury caused by errors when control‐
ling motors and working at moving parts!
WARNING
●
Do not work at running or unsecured installations.
●
Before starting to dismount, secure the machine against accidental
movements and unauthorized operation.
●
Before dismounting them, secure the motor and the supply lines unit
against falling or movements, before unfastening the mechanical con‐
nections.
Via the
interface, it is possible to "release" the integrated holding brake:
●
A voltage of 30 … 46 V has to be applied at X103.1 (pins 11 and 12).
●
Short-circuit pin 3 with pin 9 at X141.
●
The holding brake is released after the system has been booted up
(
The "release holding brake" service function may only be used
provided that communication with other drive components or with
an Engineering tool has not been established.
With operational communication established, the holding system
check command can be used to release the holding brake (pa‐
rameter "P‑0‑0541, C2100 Holding system check command").
DOK-INDRV*-KCU02+KSM02-PR03-EN-P
Bosch Rexroth AG
313/337
Rexroth IndraDrive Mi Drive Systems with KCU02 KSM02, KMS02/03, KMV03, KNK03
Commissioning, operation, diagnostics and maintenance
LSA Control S.L. www.lsa-control.com [email protected] (+34) 960 62 43 01