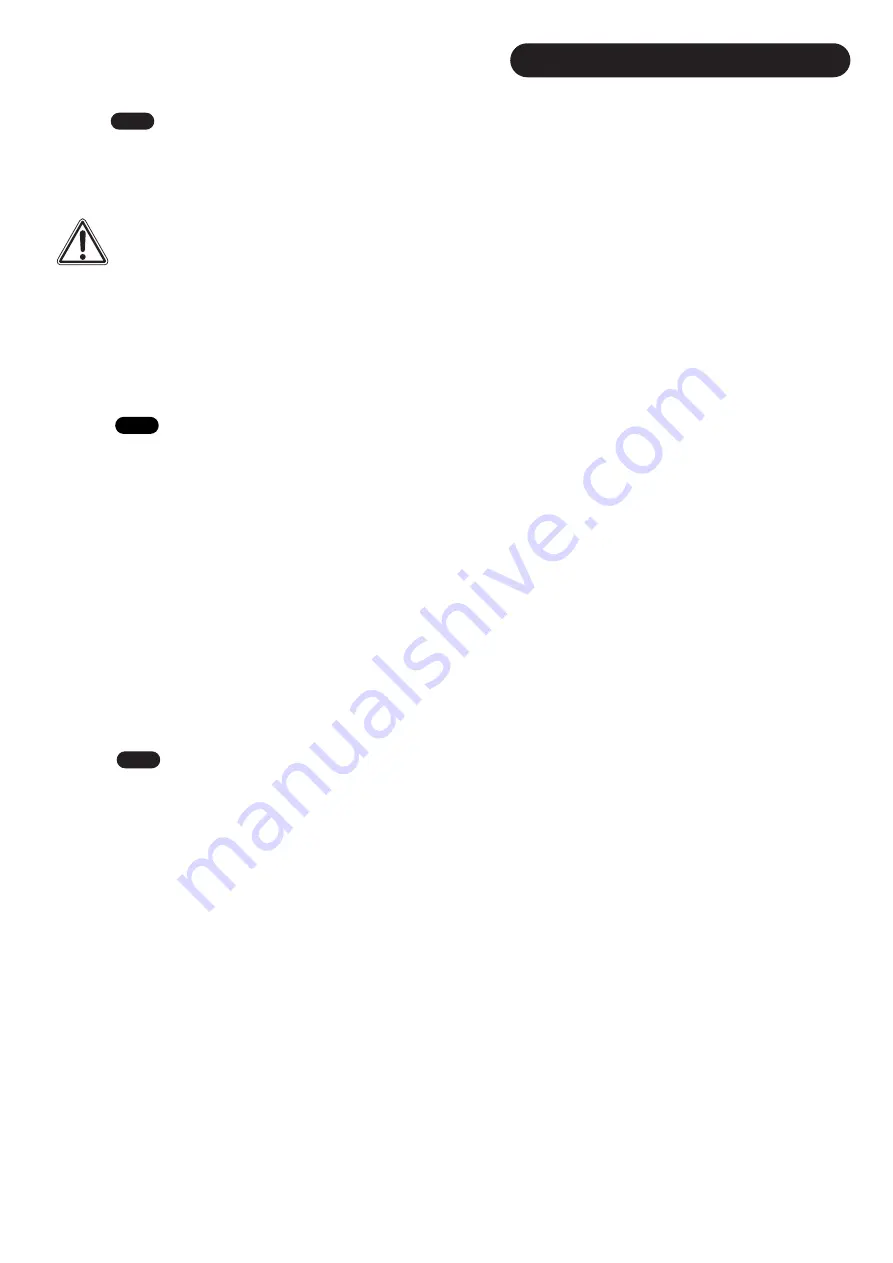
8
.0
Trouble
s
hooting
8
.1
Connecting to the tractor
Electrical connections to the tractor need to be capable of 20 amps continuous supply with no significant volt drop (ie. more than 0.5v).
Heavy wires and a high enough fuse ratings connected as close to the battery as possible will give the best results.
It is recommended the fused cable supplied is connected directly to the battery in order to avoid malfunction.
WARNING:
If you connect close to the battery use a fuse to prevent damaged conductors shorting to the chassis, melting and
possible fire.
Do not operate without fuse supplied in order to prevent damage/fire to the machine.
It is possible that high current demands, such as starting, will cause sufficient volt drop to ‘freeze’ the controller, this can also be a
symptom of a bad connection and low supply voltage. If this occurs switch off the controller by the 'Emergency Switch' and switch back
on, the controller should recover. If all connections and voltages to the controller are good then check connections inside the box to the
stop switch and PCB terminal blocks carefully. If in doubt, contact Big Bale Co South Ltd for further technical information.
8
.2
Pick Up
The pickup height is adjustable to accommodate different sizes of bales. It is important that the majority of the bales clear the table
surface on pickup and do not pinch on the edge of the table and prevent the pickup completing its cycle and add unnecessary stress
to the pickup, tines and table components.
This symptom may still occur when the ground is particularly uneven. In this event, manually withdraw the pickup tines, manually finish
the pickup up cycle and then re-press auto pickup key to complete the auto cycle and prevent the controller becoming ‘hung up’ in the
pickup cycle and corrupting subsequent cycles. It will be noticed that the tines re-enter the bale at this point.
With bales in excess of 1200mm depth it may be necessary to raise the connecting height of the machine to the tractor, to above level,
to compensate.
Difficulty may be experienced with bales of lower density and/or short straw being damaged by the pickup and a central portion is torn
from the bale. To get the best results in these conditions, Ensure the tines are fully entering the bale.
Experiment with different tine configurations and density, 6, 4 or 2 tines in the optional positions.
High density bales will stress the pickup tines more and result in pre-mature breakages of the tines and stress the tine frames.
8
.3
Stacking
When two or three bales are placed onto the table it is important that they are central on a line the length of the machine. Bales not
placed centrally may cause difficulty in pushing the stack back down the platform, (when they are tied) may cause the bales to be
impaled on the side clamp bale keeps and generally contribute to a poor stack appearance and weather resistance.
Obstruction of the tie cycle may cause problems. The extension frame may not be coming forward sufficiently to clear the bales on the
platform in which case See
Section Proximity Sensors 6.8
. In any case, manual interruption of the cycle to adjust the extension to
clear the obstruction will stop the auto cycles which can be resumed by re-pressing the associated auto key.
In conditions of high friction between the bales (often moisture) the stack cycle may stop before the bales are fully raised into the
platform. Ensure that the clamps are not unnecessarily restricting the stack to avoid frictional contact with the bales. Manual forward
extension will clear the problem and re-pressing the correct auto stack key will resume the cycle.
When performing a stack, the forks have to come forward to the front of the platform before the platform is raised. If you are finding the
forks are not coming all the way forward and seem to be getting stuck under the platform, pull on the wire cables that are connected to
the forks (ensuring the Transtacker PTO is off). This may free any debris that could be stopping them coming forward. Perform a Forks
Forward motion and try tipping the Transtacker platform up again.
37
Содержание Transtacker 4100
Страница 61: ...58...
Страница 62: ...59...
Страница 63: ...11 0 Hydraulic Systems 11 4 Valve Block Schematic Fig 168 60...
Страница 67: ...13 0 Maintenance 13 2 Pickup Grease Points Fig 172 64...
Страница 68: ...13 0 Maintenance 13 3 Grab Arm Grease Points Fig 173 65...
Страница 69: ...13 0 Maintenance 13 4 Turntable A Frame Grease Points Fig 174 66...
Страница 70: ...13 0 Maintenance 13 5 Side Gate Grease Points Fig 175 67...
Страница 71: ...13 0 Maintenance 13 6 Rear Clamps Grease Points Fig 176 68...
Страница 72: ...13 0 Maintenance 13 7 Chassis Grease Points Fig 177 69...
Страница 73: ...13 0 Maintenance 13 8 Platform Grease Points Fig 178 70...
Страница 74: ...13 0 Maintenance 13 9 Axle Grease Points Fig 179 71...
Страница 84: ...16 0 Operators Notes 81...
Страница 85: ...82...
Страница 86: ...83...
Страница 87: ...84...