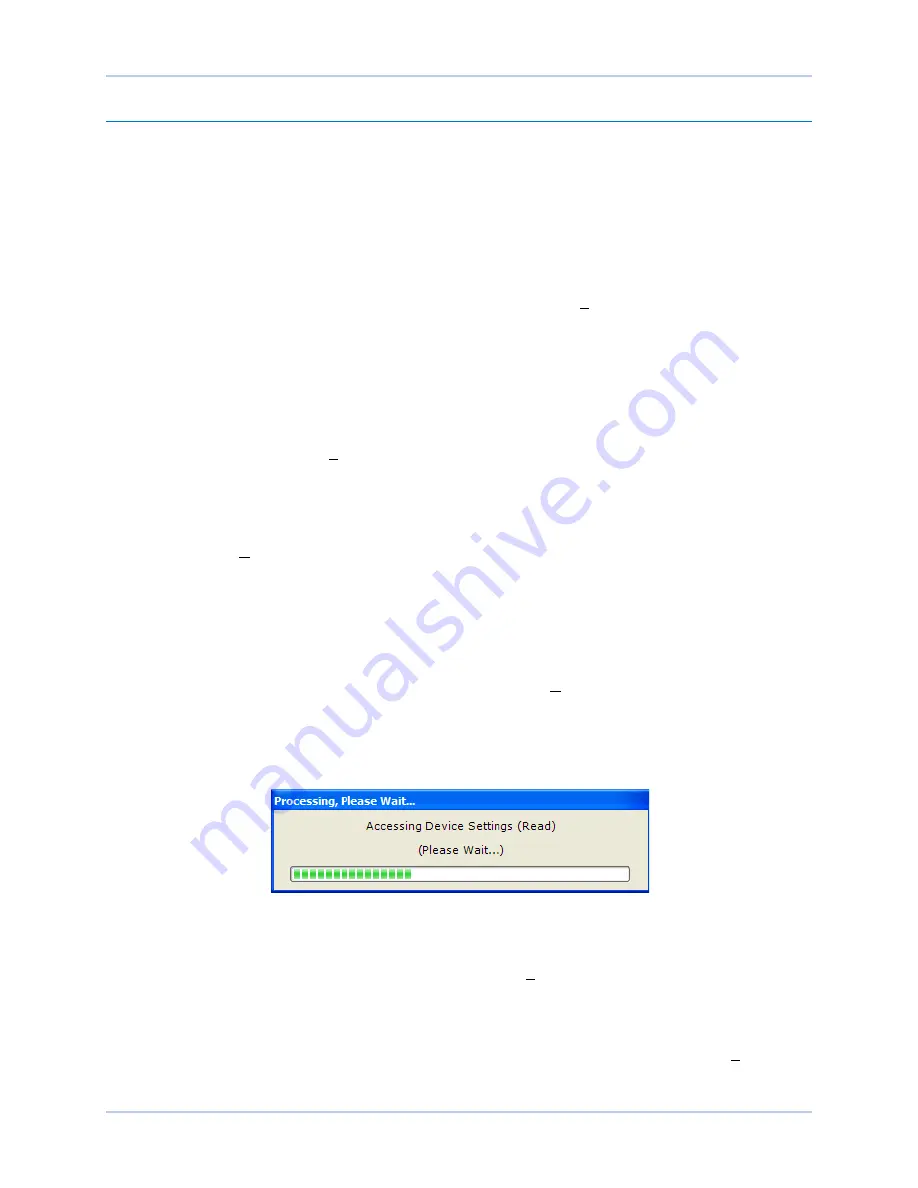
9440300990 Rev J
131
DECS-250
BESTCOMS
Plus
®
Software
Settings File Management
A settings file contains all DECS-250 settings including logic. A settings file assumes a file extension of
“
∗
.bstx”. It is possible to save the logic only as a separate logic library file on the
BESTlogicPlus
Programmable Logic
screen. This function is helpful when similar logic is required for several devices. A
logic library file assumes a file extension of “
∗
.bslx”. It is important to note that settings and logic can be
uploaded to the device separately or together, but are always downloaded together. For more information
on logic files, refer to the
BESTlogicPlus
chapter.
Opening a Settings File
To open a DECS-250 settings file with BESTCOMS
Plus
, pull down the
File
menu and choose
Open
. The
Open
dialog box appears. This dialog box allows you to use normal Windows techniques to select the file
that you want to open. Select the file and choose
Open
. You can also open a file by clicking on the
Open
File
button on the lower menu bar. If connected to a device, you will be asked to upload the settings and
logic from the file to the current device. If you choose
Yes
, the settings displayed in BESTCOMS
Plus
instance will be overwritten with the settings of the opened file.
Saving a Settings File
Select
Save
or
Save As
from the
File
pull-down menu. A dialog box pops up allowing you to enter a
filename and location to save the file. Select the
Save
button to complete the save.
Upload Settings and/or Logic to Device
To upload a settings file to the DECS-250, open the file or create a new file through BESTCOMS
Plus
.
Then pull down the
Communication
menu and select
Upload Settings and Logic to Device.
If you want to
upload operational settings without logic, select
Upload Settings to Device
. If you want to upload logic
without operational settings, select
Upload Logic to Device
. You are prompted to enter the username and
password. The default username is “
A
” and the default password is “
A
”. If the username and password
are correct, the upload begins and the progress bar is shown.
Download Settings and Logic from Device
To download settings and logic from the DECS-250, pull down the
Communication
menu and select
Download Settings and Logic from Device
. If the settings in BESTCOMS
Plus
®
have changed, a dialog
box will open asking if you want to save the current settings changes. You can choose
Yes
or
No
. After
you have taken the required action to save or discard the current settings, downloading begins.
BESTCOMS
Plus
reads all settings and logic from the DECS-250 and loads them into BESTCOMS
Plus
memory. See Figure 118.
Figure 118. Processing, Please Wait…
Printing a Settings File
To view a preview of the settings printout, select
from the
File
pull-down menu. To print the settings,
select the printer icon in the upper left corner of the
Print Preview
screen.
Comparing Settings Files
BESTCOMS
Plus
has the ability to compare two settings files. To compare files, pull down the
Tools
menu
and select
Compare Settings Files
. The
BESTCOMSPlus Settings Compare Setup
dialog box appears
(Figure 119). Select the location of the first file under
Left Settings Source
and select the location of the
Содержание DECS-250
Страница 2: ......
Страница 6: ...iv 9440300990 Rev J Revision History DECS 250 ...
Страница 16: ...xiv 9440300990 Rev J Contents DECS 250 ...
Страница 20: ...4 9440300990 Rev J Introduction DECS 250 ...
Страница 28: ...12 9440300990 Rev J Power Stage DECS 250 ...
Страница 32: ...16 9440300990 Rev J Voltage and Current Sensing DECS 250 ...
Страница 40: ...24 9440300990 Rev J Synchronizer DECS 250 ...
Страница 52: ...36 9440300990 Rev J Auxiliary Control DECS 250 ...
Страница 56: ...40 9440300990 Rev J Contact Inputs and Outputs DECS 250 ...
Страница 84: ...68 9440300990 Rev J Limiters DECS 250 ...
Страница 108: ...92 9440300990 Rev J Power System Stabilizer DECS 250 Figure 85 PSS Function Blocks and Software Switches ...
Страница 114: ...98 9440300990 Rev J Power System Stabilizer DECS 250 Figure 96 PSS Parameter Settings ...
Страница 124: ...108 9440300990 Rev J Stability Tuning DECS 250 ...
Страница 126: ...110 9440300990 Rev J Mounting DECS 250 Figure 103 Overall and Projection Mounting Dimensions ...
Страница 127: ...9440300990 Rev J 111 DECS 250 Mounting Figure 104 DECS 250 Escutcheon Plate Dimensions ...
Страница 128: ...112 9440300990 Rev J Mounting DECS 250 Figure 105 Panel Cutting and Drilling Dimensions for DECS 250 Panel Mounting ...
Страница 198: ...182 9440300990 Rev J Timekeeping DECS 250 ...
Страница 210: ...194 9440300990 Rev J CAN Communication DECS 250 ...
Страница 304: ...288 9440300990 Rev J Maintenance DECS 250 ...
Страница 316: ...300 9440300990 Rev J Specifications DECS 250 ...
Страница 334: ...318 9440300990 Rev J Analog Expansion Module DECS 250 ...
Страница 341: ...9440300990 Rev J 325 DECS 250 Contact Expansion Module Figure 188 CEM 2020 Input Contact and Output Contact Terminals ...
Страница 351: ......