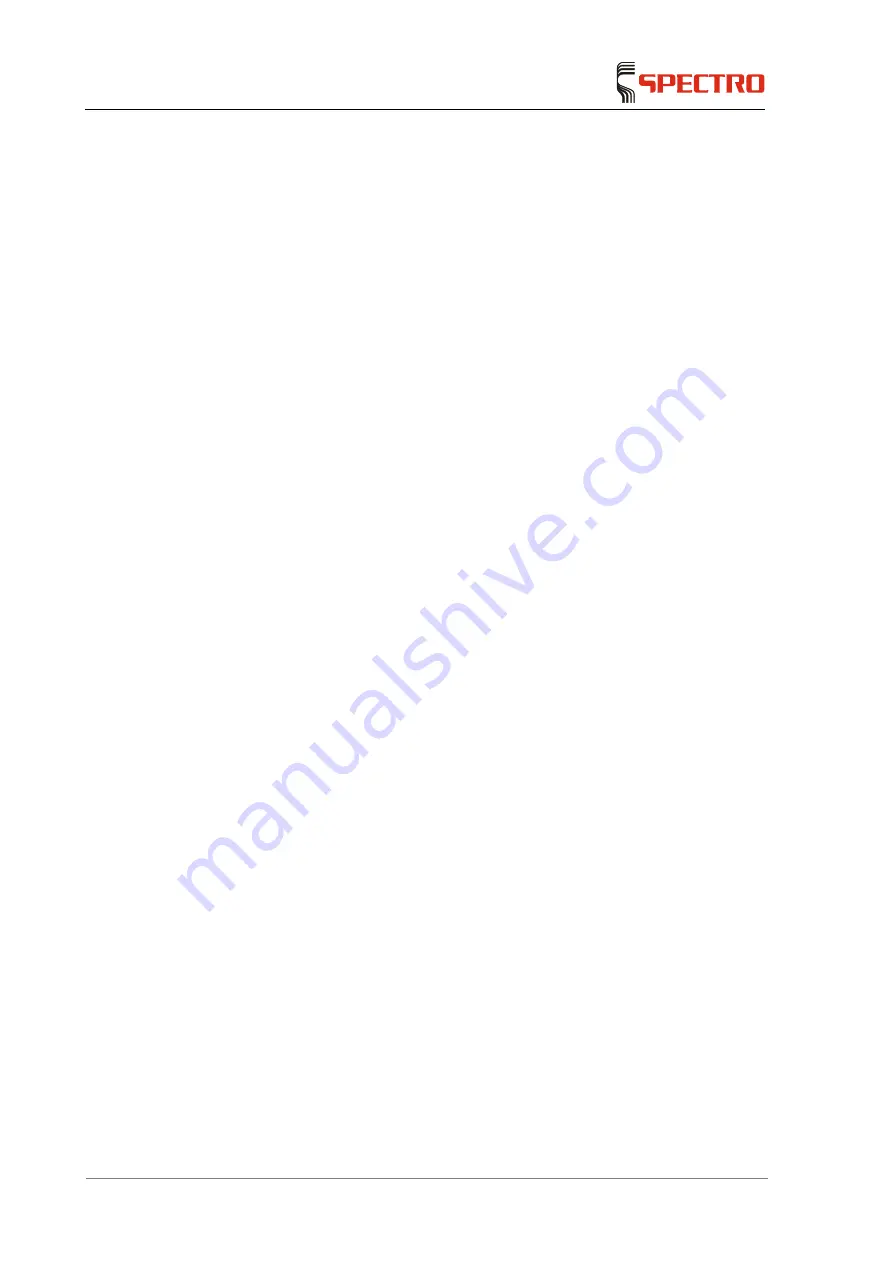
Spare parts and consumables
— 54
SPECTRO ARCOS FHX22 — 18.07.2019
8
Spare parts and consumables
You can find the spare parts and consumables for this instrument under "Support -
Parts Catalogue" (Service – Parts Catalogue) on our website at www.spectro.com.
Use only genuine spare parts for repairing the instrument. The use of non-genuine
spare parts will make the CE Declaration of Conformity null and void. Excepted
are spare parts from manufacturers approved by SPECTRO.
Only the use of genuine spare parts and consumables ensures the safe operation
and achievement of the specified output. This applies especially to all components
of the sample introduction system and, in particular, to the Plasma torch.
9
De-commissioning
Only organizations or persons authorized by the instrument manufacturer shall be
permitted to de-commission the instrument. Please contact your Service Center.
10
Manufacturer address
SPECTRO Analytical Instruments GmbH
Boschstr. 10
D-47533 Kleve
Germany
Tel.: +49.2821.8 92-0
Fax: +49.2821.8 92-22 00
http://www.spectro.com