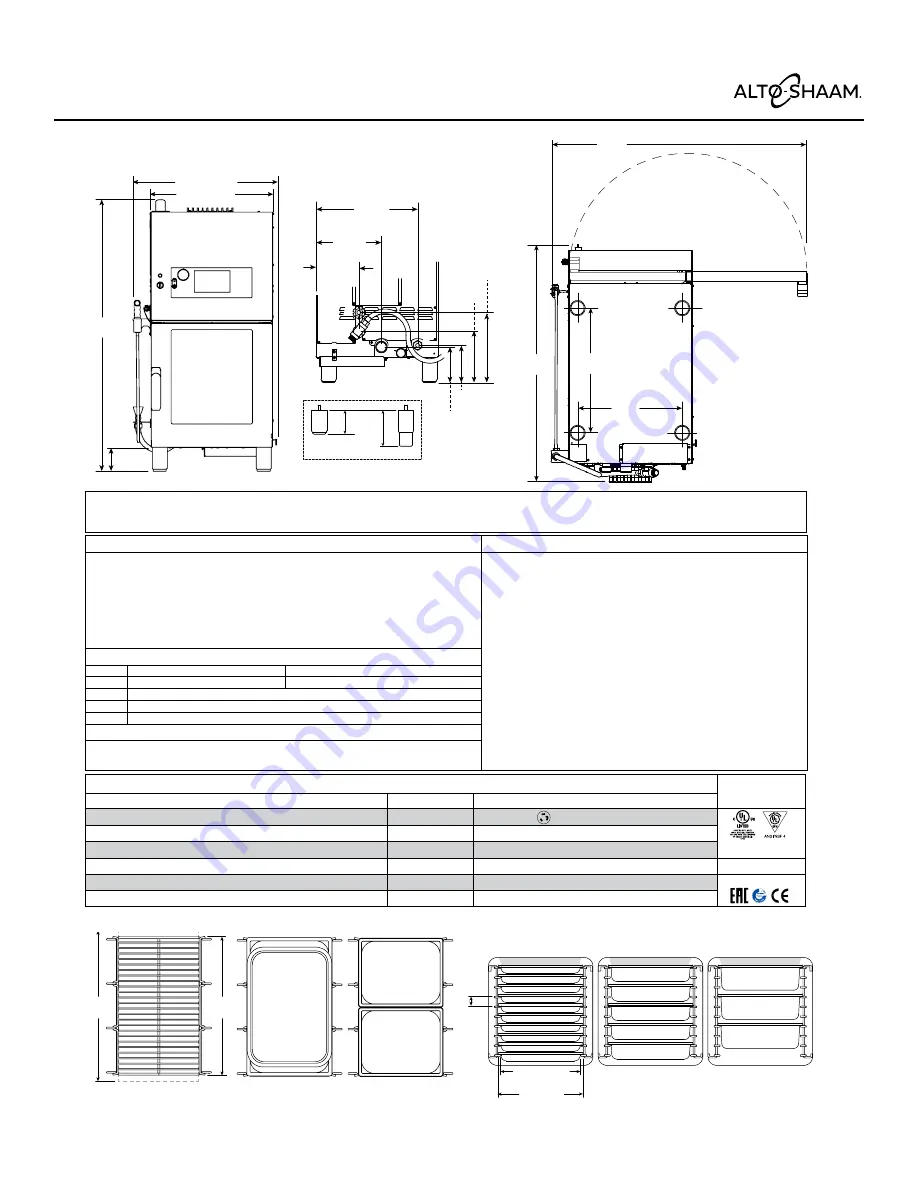
Spec Sheets
16
MN-29805 • Rev 11 • 07/18 • Combitherm CT Express Installation Manual
CTX4-10EVH
ELECTRICAL
(DEDICATED CIRCUIT REQUIRED)
✎
Certification
VOLTAGE
PH
HZ
AMPS
kW
AWG
CORD & PLUG
208
1
60
23.4
4.87
—
NEMA L6-30P - US only
240
1
60
26.3
6.31
8
no cord or plug
208 – 240
3
60
15.9 – 18.8
5.59 – 7.67
10
no cord or plug
208 – 240
1
50
23.4 – 26.3
4.87 – 6.31
—
8/3 cord, no plug
220 – 240
1
50/60
24.9 – 26.3
5.47 – 6.60
8
no cord or plug
380 – 415
3
50/60
9.8 – 10.8
6.49 – 7.67
10
no cord or plug
✎
IP X4
IP X4
IP X4
WATER REQUIREMENTS
WATER QUALITY STANDARDS
TWO (2) COLD WATER INLETS - DRINKING QUALITY*
ONE (1) TREATED WATER INLET: 3/4" NPT connection. Line pressure 30 psi minimum dynamic and
90 psi maximum static (200 to 600 kPa) at a minimum flow rate of 0.13 gpm (0.5 L/min).
ONE (1) UNTREATED WATER INLET: 3/4" NPT connection. Line pressure 30 psi minimum dynamic and
90 psi maximum static (200 to 600 kPa) at a minimum flow rate of 2.64 gpm (10 L/min).
* Both inlets can be from same source. Divide using a manifold. Run one side through treatment device before running to oven.
Must meet line pressure and flow rate specifications for both inlets.
WATER DRAIN: 1-1/2" NPT (50mm) connection with a vertical vent to extend above the exhaust vent.
Materials must withstand temperatures up to 200°F (93°C).
It is the sole responsibility of the owner/operator/purchaser of this equipment
to verify that the incoming water supply is comprehensively tested and
if required, a means of “water treatment” provided that would meet
compliance requirements with the published water quality standards shown
below. Non-compliance with these minimum standards will potentially
damage this equipment and/or components and void the original equipment
manufacturer’s warranty. Alto-Shaam recommends using OptiPure
®
[www.
optipurewater.com] products to properly treat your water.
Contaminant
Free Chlorine
Hardness
Chloride
pH
Silica
Total Dissolved Solids (tds)
Inlet Water Requirements
Less than 0.1 ppm (mg/L)
30-70 ppm
Less than 30 ppm (mg/L)
7.0 to 8.5
Less than 12 ppm (mg/L)
Treated line: 50-125 ppm
Untreated line: 50-360 ppm
CLEARANCE REQUIREMENTS
LEFT:
4" (102mm)
18" (457mm) recommended service access
RIGHT:
4" (102mm) Non-combustible surfaces
2" (51mm) door swing or combustible surfaces
TOP:
20" (508mm) for air movement
BOTTOM: 4” (102mm) for air movement
BACK:
4" (102mm)
INSTALLATION REQUIREMENTS
• Oven must be installed level.
• Water supply shut-off valve and back-flow preventer when required by local code.
Exterior Dimensions (H x W x D) 45-1/2" x 24-1/8" x 39-3/8" (1153mm x 612mm x 999mm)
Net Weight 260 lb (118 kg)
Ship Dimensions (L x W x H) 43" x 42" x 58" (1092mm x 1067mm x 1473mm)*
Ship Weight 415 lb (188 kg)*
*Domestic ground shipping information. Contact factory for export weight and dimensions.
39-3/8"
(999mm)
42-1/2"
(1078mm)
20-3/4" (526mm)
24-1/8" (612mm)
4"
(102mm)
45-1/2"
(1153mm)
6" (152mm)
4" (102mm)
D: 16-7/8"
(428mm)
C:
10-7/8"
(276mm)
C: 5-3/4"
(145mm)
D: 6"
(152mm)
B: 8-1/4"
(211mm)
A: 11-1/2"
(292mm)
A, B:
7-1/8"
(181mm)
A
A
B
C
D
D
20-3/4"
(527mm)
17-3/8"
(442mm)
A = Treated water inlet
B = Untreated water inlet
C = Water drain
D = Electrical connection
Front
Back
Bottom
Floor standing units require a 6" leg.
37-1/4"
(946mm)
42-1/2"
(1078mm)
24-3/8" (619mm)
6" (152mm)
4" (102mm)
D: 16-7/8"
(428mm)
C:
10-7/8"
(276mm)
C: 5-3/4"
(145mm)
D: 6"
(152mm)
B: 8-1/4"
(211mm)
A: 11-1/2"
(292mm)
A, B:
7-1/8"
(181mm)
4"
(102mm)
33-1/2"
(851mm)
12-3/8" (313mm)
13" (335mm)
1-1/2"
(35mm)
22-5/8"
(574mm)
20-7/8"
(529mm)
12-3/8" (313mm)
13" (335mm)
1-1/2"
(35mm)
22-5/8"
(574mm)
20-7/8"
(529mm)
A
A
B
C
D
D
20-3/4"
(527mm)
17-3/8"
(442mm)
20-1/2" (520mm)
#423a - 07/18
DUE TO ONGOING PRODUCT IMPROVEMENT, SPECIFICATIONS ARE SUBJECT TO CHANGE WITHOUT NOTICE.
WWW.ALTO-SHAAM.COM
Half-Size Sheet: 1"
Full-Size Hotel : 1-1/4"
GN 1/1:
20mm
Half-Size Sheet:
18" x 13"
Full-Size Hotel**:
20-7/8 x 12-3/4"
GN 1/1:
530mm x 325mm
Half-Size Hotel**:
10-3/8 x 12-3/4"
GN 1/2:
265mm x 325mm
Full-Size Hotel : 2-1/2"
GN 1/1:
65mm
Full-Size Hotel : 4"
GN 1/1:
100mm
CAPACITY Product Maximum 48 lb (22 kg) Volume Maximum 30 qt (38 L)
Pan Capacity = 10* Pan Capacity = 5* Pan Capacity = 3*
* Broiler option (gray area) reduces pan capacity by one pan.
** Hotel pan width varies by brand. Pans with a width less than 12-1/2" require wire shelves and may require purchase of additional shelves (standard = 2) for maximum capacity.
Cavity Depth
Rack Depth
Rack width
Distance between ledges
Содержание CT Express Combitherm CTX4-10E
Страница 14: ...This page intentionally left blank...
Страница 27: ...Installation MN 29805 Rev 11 07 18 Combitherm CT Express Installation Manual 27 a b c d e f h i j g...
Страница 29: ...Installation MN 29805 Rev 11 07 18 Combitherm CT Express Installation Manual 29 a b d e g h i f c 45 45 90 90...
Страница 52: ...CT Express...