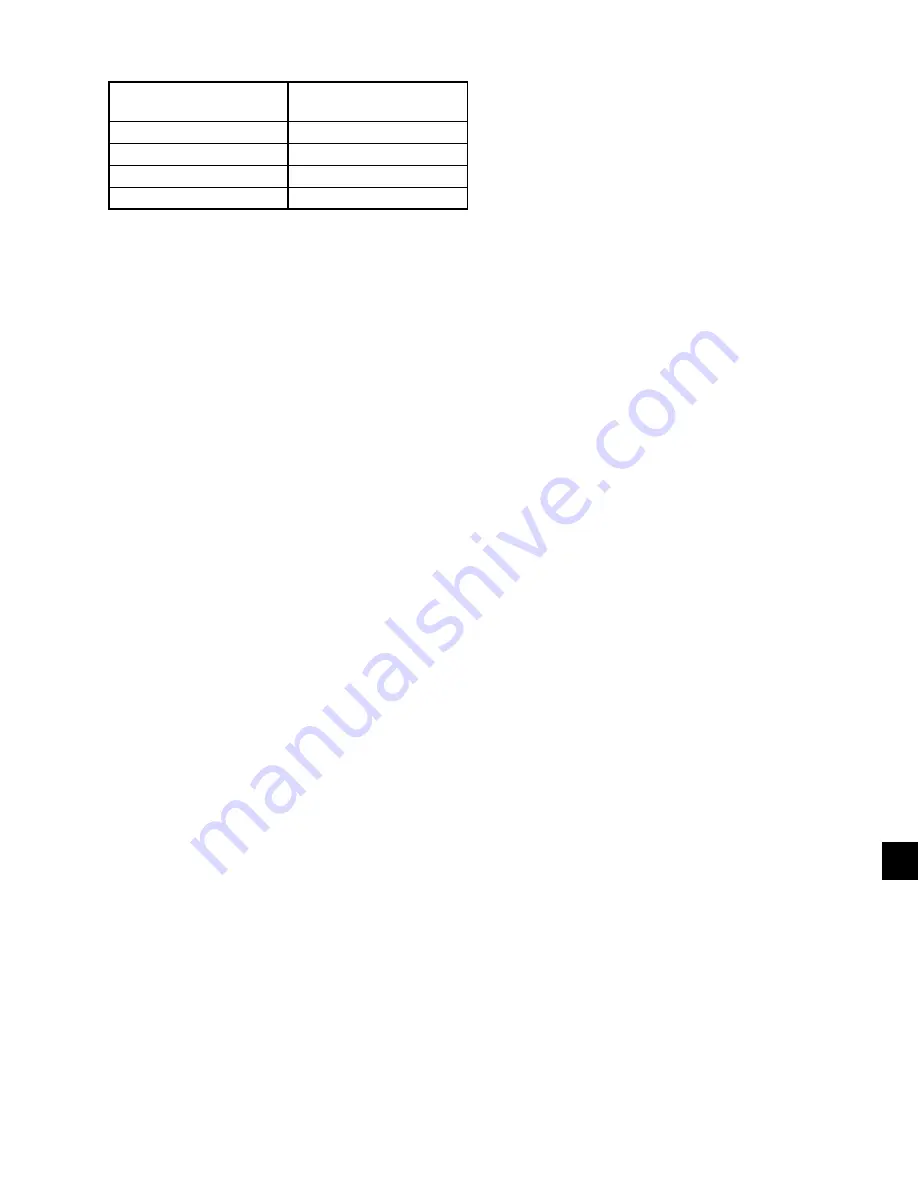
151
SECTION 14 - ADAPTIVE CAPACITY CONTROL BOARD
FORM 160.54-M1
ISSUE DATE: 10/25/2019
JOHNSON CONTROLS
JCI COMPANY CONFIDENTIAL
14
FREQUENCY
COMMAND INCREASE
MOTOR CURRENT
1.0 Hz
> 90% FLA
1.5 Hz
>75% FLA
2.0 Hz
>60% FLA
4.0 Hz
> or = 60% FLA
The Pre-rotation Vanes Position potentiometer is con-
nected to the microboard (See
).
It must be calibrated by a Service technician using the
procedure in
SECTION 33 - SYSTEM CALIBRATION,
SERVICE SETPOINTS, AND RESET PROCEDURES
of this manual.
With software version C.OPT.01.19.307 (and later),
to ensure that frequency increases do not cause exces-
sive motor current resulting in overload shutdowns,
frequency increase limitations are imposed based upon
how close the actual motor current is to the chiller full
load amps. In Automatic Frequency Control Mode,
anytime the microboard ACC function increases the
VSD or MV VSD output frequency, the frequency in-
crease is limited by the motor current as follows. Al-
though the incremental frequency increases can be less
than allowed, they will never be greater than allowed.
These limitations also apply to the frequency ramp that
occurs at chiller start while ramping from start frequen-
cy 30Hz (60Hz applications ) or 25Hz (50Hz applica-
tions) to maximum frequency. These limitations are
not imposed in Manual Frequency Control:
• When motor current is less than or equal to 80%
FLA - No Limiting
• When motor current is more than 80% FLA and
less than or equal to 98% FLA - Increase 0.1Hz ev-
ery {2 + (%FLA-80)} seconds
• When Motor Current more than 98% FLA - In-
crease 0.1Hz every 20 seconds
If heat pump duty is enabled and operating in Heat-
ing Mode, the VSD is commanded to run at maximum
speed at all times. When Heat Pump Duty is set to
Cooling Mode, the VSD operates.
With software version C.OPT.01.21.307 (and later) if
motor current is greater than or equal to 101% FLA,
the VSD speed command is decreased 0.1Hz every 3.0
seconds until the motor current is less than 101% FLA.
The Surge Map takes priority over current limiting.
Thus if there is a mapped surge point in the present
sector, ACC current limiting shall not be allowed to de-
crease the frequency below the mapped point.
In previous software versions, the initial ramp is com-
plete when either of the following conditions occur:
• Delta T is less than ACC Mapping Enable
• VSD Speed Command equals Maximum
In this version, the initial ramp will be complete when
any of the following occur:
• Delta T less than ACC Mapping Enable
• VSD Speed Command equals Maximum
• Motor Current is more than or equal to 100 %FLA
When the VSD initiates a fault shutdown, it opens the
VSD stop contacts on the VSD logic board, notifying
the microboard as described in
The SURGE MAP screen displays the surge map in
TABLE or LIST form, as shown in
OptiView Control
Panel – Operation
(Form 160.54-O1),
FIGURE 37
and 38
. When set to TABLE, the map is shown graphi-
cally. The X-Axis is Delta P/P and the Y-Axis is PRV
position. Each VSD frequency point is represented by
an X in the table. The present operating conditions are
indicated with an * and are detailed at the bottom of the
screen under PRESENT.
If the present condition is the same as a mapped point,
the * will be replaced by an O. To view the details of any
mapped point, position the green box (□) over the desired
X using the arrow keys (▲▼◄ ►). The VSD Output
Frequency, Pre-rotation Vanes Position and Delta P/P of
the selected point is displayed at the bottom of the screen
under SELECTED. Surge points can be inserted manu-
ally using the MANUAL SURGE POINT key, while the
chiller is running. They can be deleted manually using
the REMOVE SURGE POINT key by positioning the □
over the desired X. When set to LIST, the Delta P/P, PRV
Position and VSD Output Frequency of each mapped
point are listed in rows. This is the same report that is
generated when the surge map is sent to a printer. The
PAGE UP and PAGE DOWN keys are used to scroll to
the previous or next listing.
The stability limit programming button was removed
from the ACC DETAILS screen in a previous software
version. The stability limit default and maximum val-
ues are presently set to 7000. If a new version of soft-
ware were installed in a chiller with stability limit set
below 7000, the old value would be retained. The only
way to clear it is to clear the BRAM. To prevent this
from happening, this value is no longer programmable.
It is now always set to 7000.