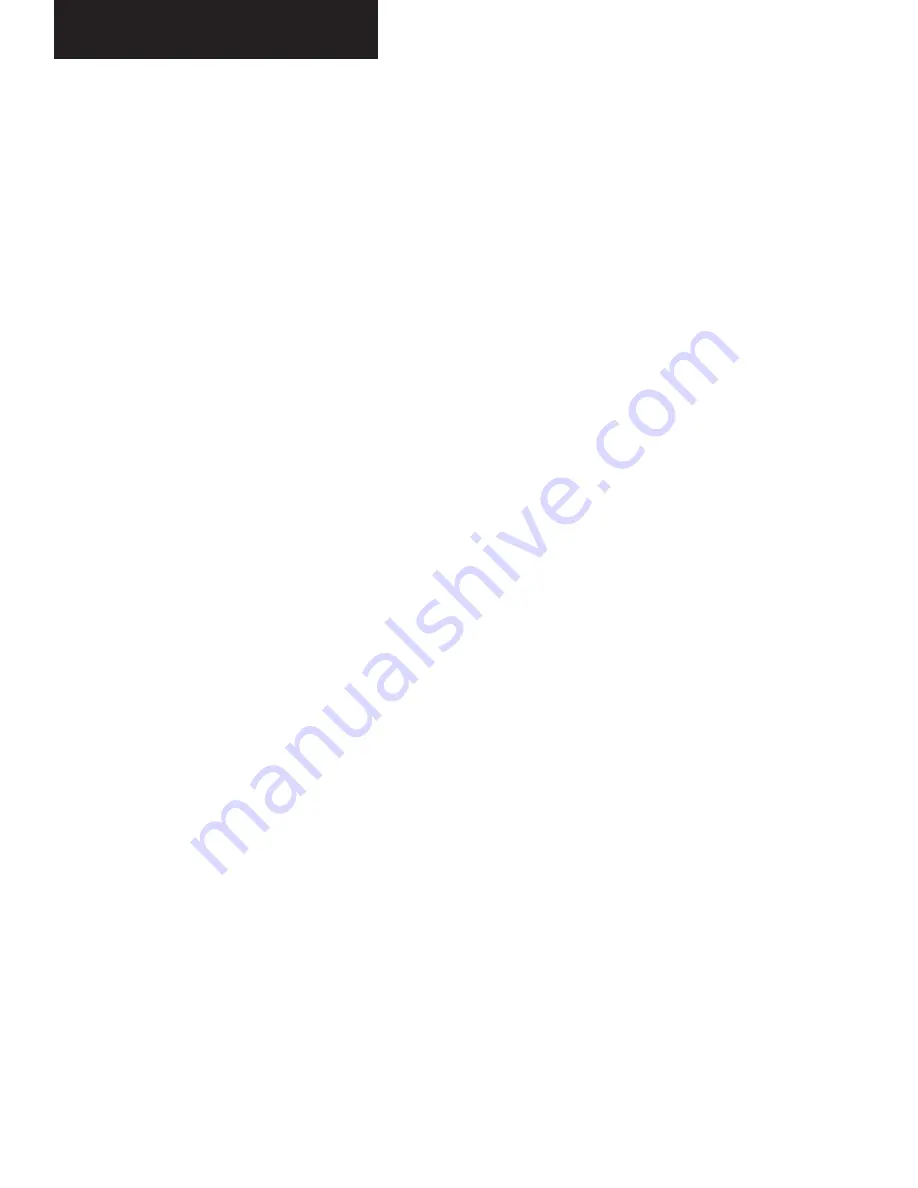
YORK INTERNATIONAL
108
FORM 100.50-NOM1 (604)
Parameter Description and Options
Next, the Primary Unit Controller will open the Econo-
mizer to the 100% position and wait three minutes
before closing it to the Minimum Position.
During the RUN TEST, the Primary Unit Controller
will read all the installed sensors and verify that their
readings are reliable. If an unreliable sensor is de-
tected, an appropriate sensor fault will be identi
Þ
ed.
PANEL TEST
The PANEL TEST is only used for factory testing
when no equipment is connected to the Primary Unit
Controller. THIS FEATURE IS NOT TO BE USED
IN THE FIELD.
HEAT/COOL SYSTEM
Number of Compressors
This con
Þ
guration setting tells the control the num-
ber of compressors available. There are two options,
4 com pres sors (50-65 Ton units) and 6 compressors
(70-90 Ton units).
Number of Heat Steps
This con
Þ
guration setting tells the control the num-
ber of heating steps available. This option will be se-
lect able from 0 to 6. Note, zero (0) must be selected
if hydronic heat is enabled.
Freezestat
This con
Þ
guration setting tells the control that a hot
water freeze protection Freezestat is installed on the
unit and that the control should monitor the
hot water
Freezestat
input. This option is used only on units with
hydronic heat (
Hydronic Heat
option is turned ON).
Transducer Package
This con
Þ
guration setting tells the control if a pressure
transducer package is installed and on what re frig -
er a tion system. If this setting is set to:
• 0, then - no pressure transducer pack age is in-
stalled on any refrigeration systems.
• 1 indicates that- a pressure transducer pack age is
in stalled on system #1 only.
• 2 indicates that- a pressure transducer pack age is
in stalled on system #1 and system #2.
• 3 indicates that- a pressure transducer pack age is
in stalled on system #1, #2, and #3.
The purpose of this setting is for establishing a fault
status. This setting will tell the control what analog
in puts should receive a signal from installed pressure
trans duc ers. For example, if there are pressure trans-
duc ers installed on system #1 only, then the control
will ignore the other four (4) inputs dedicated to op-
tional pressure transducers. If the pressures read at the
in puts for the pressure transducers are determined to
be unreliable, the control will generate a fault.
Low Ambient Confi g
This setting tells the control that low ambient hardware
is installed and the refrigeration system(s) on which
it is installed. Low ambient hardware can be installed
on any or all systems. This setting can be set to 0 – 3
which indicates the following:
0 indicates no low ambient hardware is in-
stalled.
1 indicates that low ambient hardware is in stalled
only on system #1.
2 indicates that low ambient hardware is in stalled
on system #1 and system #2.
3 indicates that low ambient hardware is in stalled
on systems #1, #2, and #3.
Dischrg Press Cntrl
This setting tells the control what the Discharge
Pres sure Control Setpoint is for Low Ambient Op-
eration.
Sys Unloading Press
This setting tells the control at what discharge pres-
sure to unload the compressor system. This parameter
ap plies to all compressor systems.
Reset Lead Lag
Setting Reset Lead Lag to ON tells the control to set
the accumulated compressor run times to zero. This
causes all compressors to be considered as if they
have no runtime history. This is a one time action.
The con trol resets the ON to OFF as soon as the run-
times are zeroed.
EXCESSIVE SAT
SAT Temper Available
This tells the control that equipment necessary to do
SAT Tempering is installed. SAT Tempering will be
avail able for all heat options.