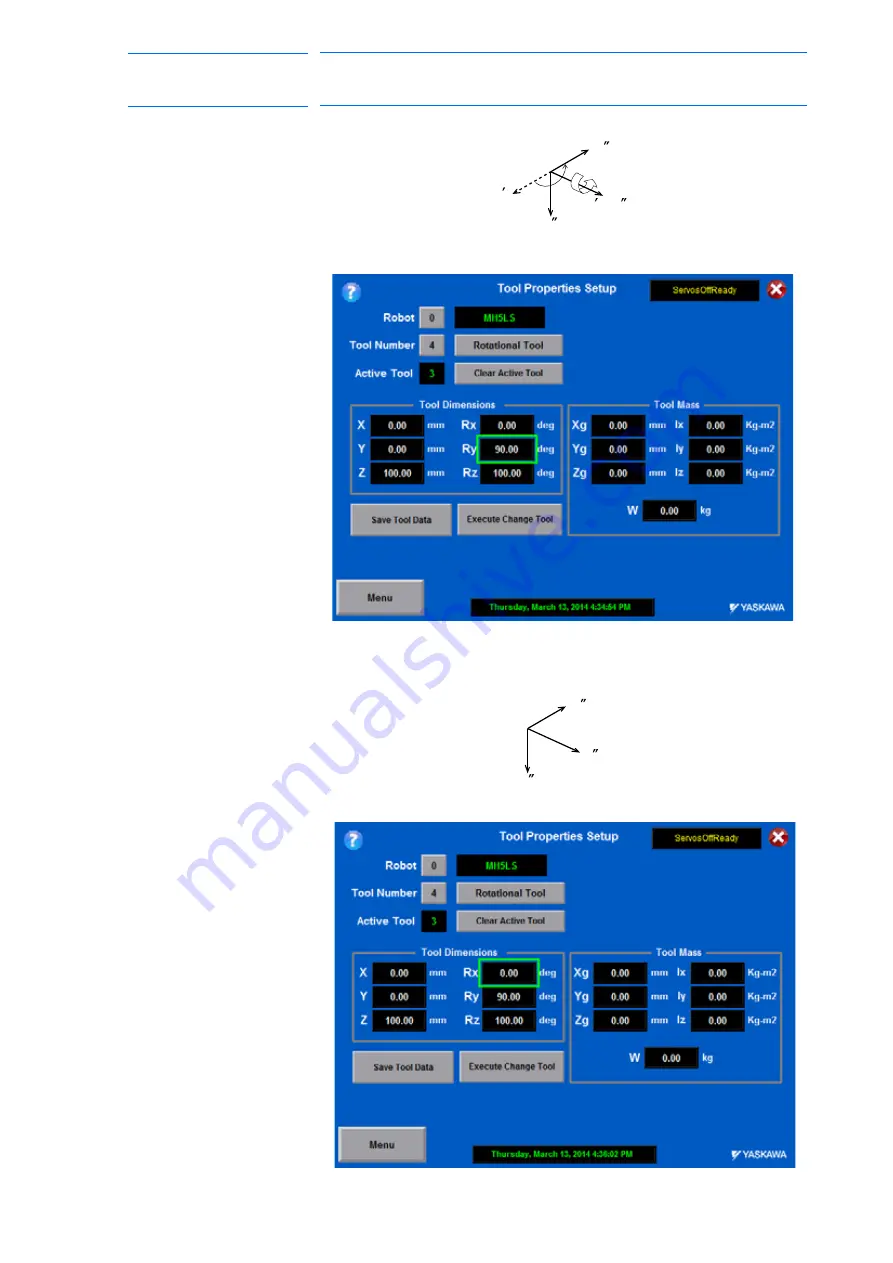
7-14
168283-1CD
168283-1CD
Hardware Installation &
Software Upgrade
7 System Setup
7.2 Tool Data Setting
Ry must be the input rotation angle around Y’
F
flange coordinates.
– Rx must be the input rotation angle around X’
F
of flange
coordinates.
Z
F
Z
F
Y
F
(Y
)
F
X
F
Ry = 90
Z
F
Y
F
X
F
Rx = 0
64 of 121