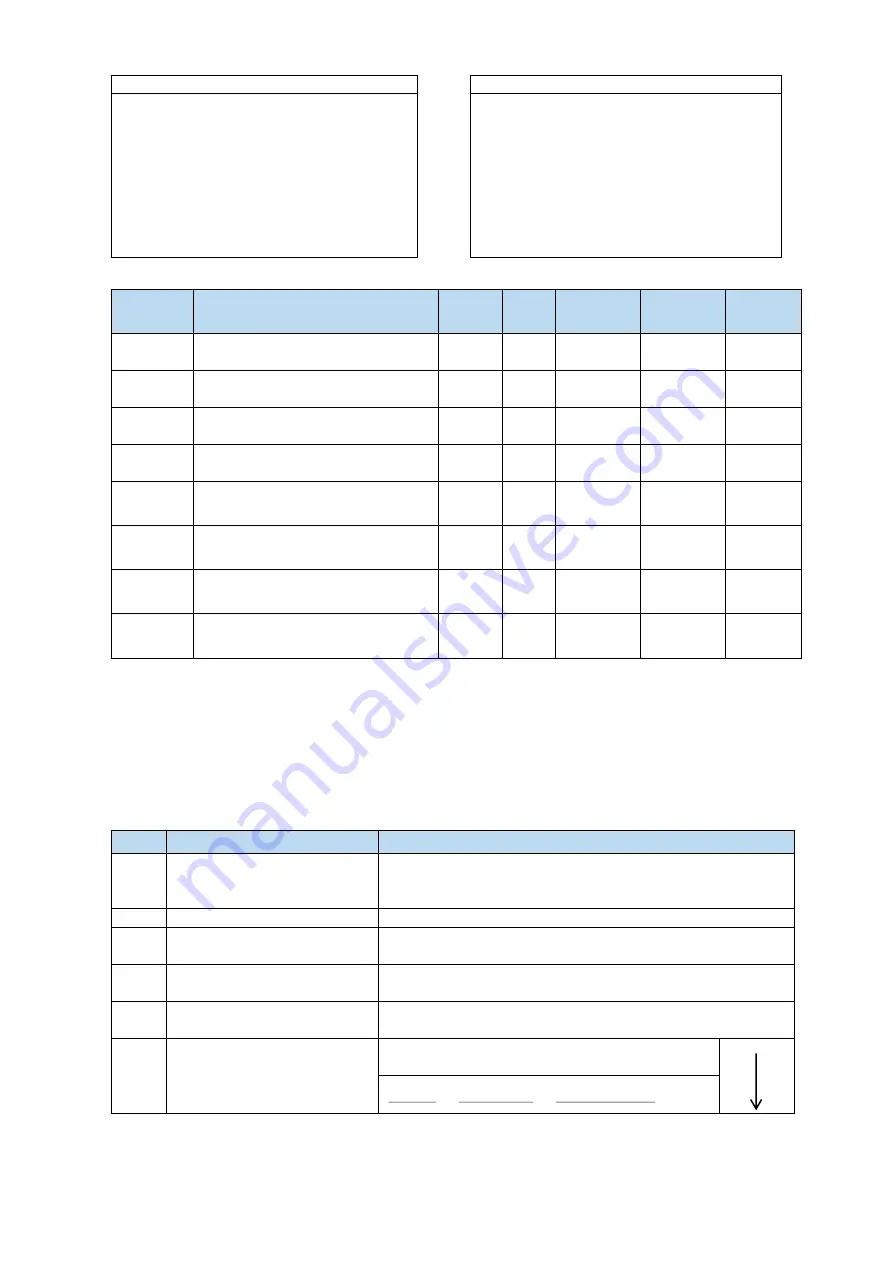
Do not change the electronic gear ratio
Change the electronic gear ratio
Without changing the ratio of the electronic
gear to the motor, the rotating cycle is
131072 pulses (P 0-11=0, P 0-12=0).
If the workpiece is moved 6 mm in one turn,
the number of pulses needed is 131072. If the
workpiece is moved 10 mm, it will need
10/6*131072=218453.333 pulses. When the
decimal number is omitted, the error will
occur.
By changing the electronic gear ratio, the
motor needs 6000 pulses to rotate one circle.
If the workpiece moves 6 mm in one turn, the
number of pulses needed is 6 000. If the
workpiece is moved 10 mm, it needs
10/6*6000 = 10000 pulses. When the pulse is
sent, the decimal number will not be produced
and the error will not be produced.
Related parameters
Parameter
Meaning
Default
setting
Unit
Setting
range
Modify
Effective
P0-11
Pulse numbers per rotation *1
0
pul
0
~
9999
Servo
OFF
At once
P0-12
Pulse numbers per rotation *10000
1
pul
0
~
9999
Servo
OFF
At once
P0-13
Electronic gear ratio (numerator)
1
-
0
~
65535
Servo
OFF
At once
P0-14
Electronic gear ratio (denominator)
1
-
0
~
65535
Servo
OFF
At once
P0-92
Group 2 Electronic gear ratio
(numerator) low bit*1
1
-
1
~
9999
Servo
OFF
At once
P0-93
Group 2 Electronic gear ratio
(numerator) high bit*10000
0
-
1
~
65535
Servo
OFF
At once
P0-94
Group 2 Electronic gear ratio
(denominator) low bit*1
1
-
1
~
9999
Servo
OFF
At once
P0-95
Group 2 Electronic gear ratio
(denominator) high bit*10000
0
-
1
~
65535
Servo
OFF
At once
Note:
(1) P0-11~P0-14 is all about the parameters of electronic gear ratio, P0-11, P0-12 is group 1, P0-13,
P0-14 is group 2, but the priority of P0-11 and P0-12 is higher than that of P0-13 and P0-14. Only
when P0-11 and P0-12 are set to 0, the ratio of electronic gear P0-13 and P0-14 will take effect.
(2) When P0-11, P0-12, P0-13 and P0-14 are all set to 0, P0-92, P0-93, P0-94 and P0-95 will take
effect.
2. Calculation of Pulse Number per Rotation and Electronic Gear Ratio
Steps
Content
Description
1
Confirm
the
machine
specification
Confirm the deceleration ratio n:m(servo motor turns m
rotations while load turns n rotations), ball screw distance,
pulley diameter.
2
Confirm the encoder pulse
Confirm the servo motor encoder accuracy
3
Set the command unit
Determine the actual distance or angle corresponding to 1
pulse of the controller
4
Calculate the command pulses
the load shaft rotates 1 circle
Based on the determined command unit, calculate the
command quantity n of the load shaft rotating for 1 revolution.
5
Calculate
the
pulses
per
rotation M
Command pulse number of motor shaft rotating for 1 turn
M=N/(m/n).
6
Set the pulses per rotation
(P0-11/P0-12) or
Electronic
gear
ratio
(P0-13/P0-14)/(P0-92~95)
P0-11=M%10000
P0-12=M/10000
priority
n
N
m
M
14
0
P
13
0
P
resolution
encoder
resolution
encoder
Note:
(1) In step 6, the effective priority of the number of pulses per revolution is higher than the
electronic gear ratio, that is, when P0-11 ~ P0-12 are all 0, P0-13 ~ P0-14 will take effect. In special
Summary of Contents for DS5K Series
Page 1: ...DS5K series servo driver User manual WUXI XINJE ELECTRIC CO LTD Data No SC5 03 20200217 1 1...
Page 2: ......
Page 6: ......
Page 107: ...3 Set the auto tuning interface 4 Click ok to start inertia identification...
Page 114: ...3 set the auto tuning interface 4 click ok to estimate the inertia...
Page 116: ...6 Start auto tuning 7 Wait for the end of the auto tuning...
Page 120: ...with higher rigidity 6 Start auto tune 7 Open the servo enable then click ok...
Page 186: ...Appendix 9 Torque speed characteristic curve...
Page 187: ......
Page 188: ......