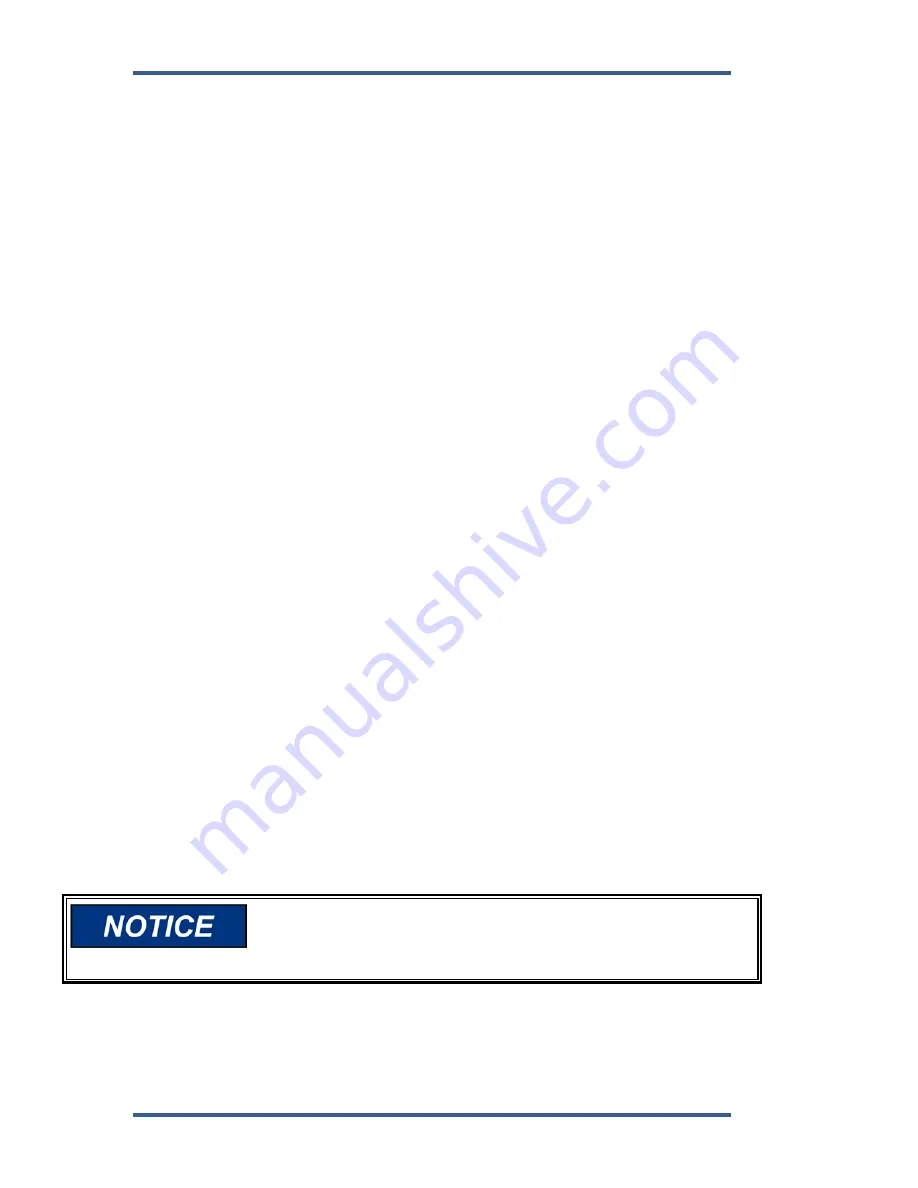
ProAct P-Series FL Position Controller
Manual 26659
88
Woodward
Replacement/Exchange:
Replacement/Exchange is a premium program
designed for the user who is in need of immediate service. It allows you to
request and receive a like-new replacement unit in minimum time (usually within
24 hours of the request), providing a suitable unit is available at the time of the
request, thereby minimizing costly downtime.
This option allows you to call your Full-Service Distributor in the event of an
unexpected outage, or in advance of a scheduled outage, to request a
replacement control unit. If the unit is available at the time of the call, it can
usually be shipped out within 24 hours. You replace your field control unit with
the like-new replacement and return the field unit to the Full-Service Distributor.
Flat Rate Repair
: Flat Rate Repair is available for many of the standard
mechanical products and some of the electronic products in the field. This
program offers you repair service for your products with the advantage of
knowing in advance what the cost will be.
Flat Rate Remanufacture:
Flat Rate Remanufacture is very similar to the Flat
Rate Repair option, with the exception that the unit will be returned to you in “like-
new” condition. This option is applicable to mechanical products only.
Returning Equipment for Repair
If a control (or any part of an electronic control) is to be returned for repair,
please contact your Full-Service Distributor in advance to obtain Return
Authorization and shipping instructions.
When shipping the item(s), attach a tag with the following information:
return
number;
name and location where the control is installed;
name and phone number of contact person;
complete Woodward part number(s) and serial number(s);
description of the problem;
instructions
describing
the desired type of repair.
Packing a Control
Use the following materials when returning a complete control:
protective caps on any connectors;
antistatic protective bags on all electronic modules;
packing materials that will not damage the surface of the unit;
at least 100 mm (4 inches) of tightly packed, industry-approved packing
material;
a packing carton with double walls;
a strong tape around the outside of the carton for increased strength.
To prevent damage to electronic components caused by improper
handling, read and observe the precautions in Woodward manual
82715, Guide for Handling and Protection of Electronic Controls,
Printed Circuit Boards, and Modules.
Replacement Parts
When ordering replacement parts for controls, include the following information:
the part number(s) (XXXX-XXXX) that is on the enclosure nameplate;
the unit serial number, which is also on the nameplate.