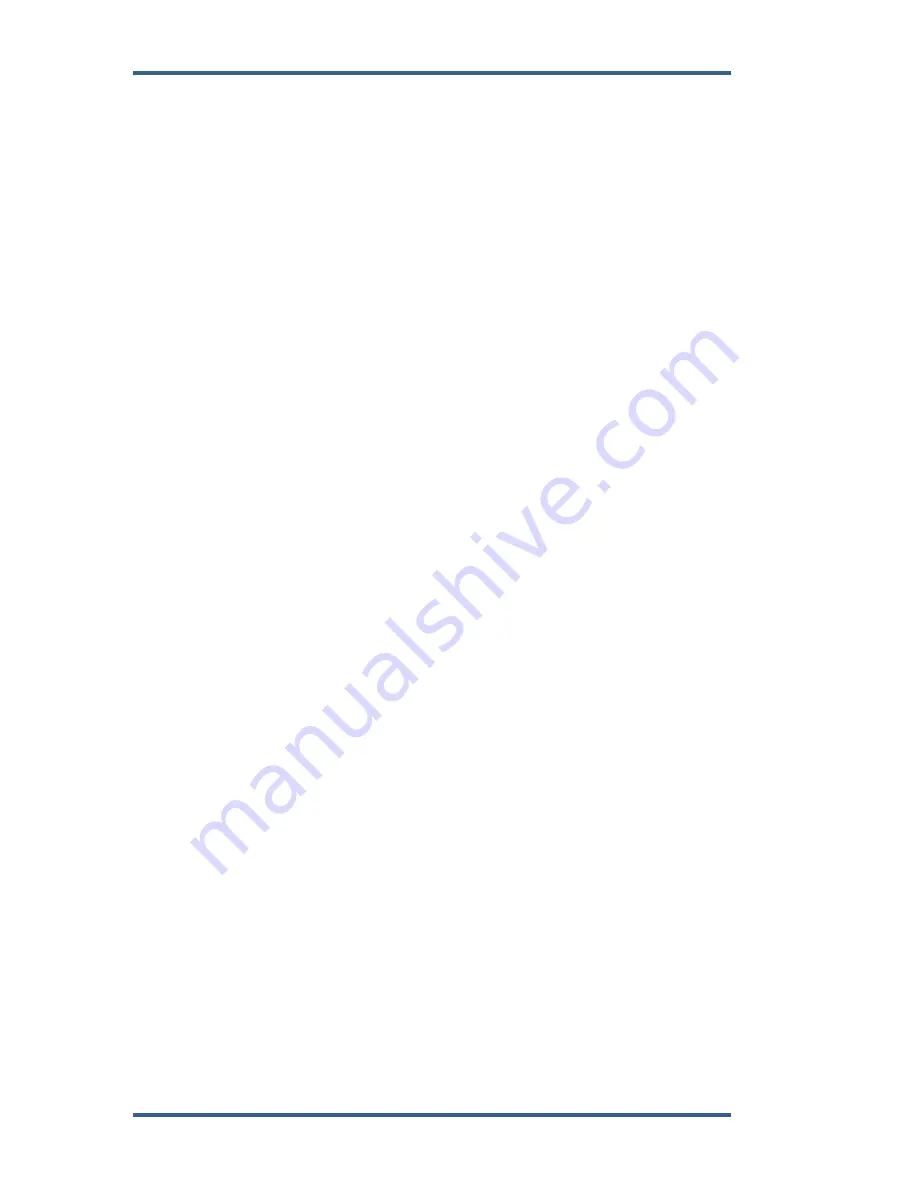
ProAct P-Series FL Position Controller
Manual 26659
28
Woodward
The input failure levels are below 3 % and above 97 % duty cycle by default but
are user-configurable.
A user-configurable offset is available to adjust the input duty-cycle reading, as
needed. This feature is used to compensate duty cycle measurement error
resulting from slow signal edge transitions.
Analog Position Command
The analog input operates from (4 to 20) mA, (0 to 5) V (dc), or (0 to 200) mA
(jumper selected). The scaling of the input to position command is user
selectable but defaults as (4 to 20) mA, (0.5 to 4.5) V (dc), and (20 to 160) mA to
command the throttle from minimum to maximum position. The input is monitored
for out of range condition and the failure levels are user configurable.
CAN Position Command
CANbus can be used to monitor unit status and/or control the commanded
position. The CAN protocol provided is SAE J1939. CAN details are provided in
Chapter 7.
When used as a position command, a minimum update rate is expected or a
CAN fault will be issued. This update rate is user-configurable.
Position Command Redundancy
The position command redundancy determines a commanded position based on
the two possible configured inputs - the primary or backup command selection of
CAN, PWM, or Analog. It provides failover (primary-to-backup) and fallback
(backup-to-primary) logic. Indications are provided for monitoring of the operating
status. These two inputs are expected to track each other such that failure of one
signal will not disrupt overall system operation.
The command redundancy utilizes two command inputs; a primary command
and a backup command (see Figure 3-3). When both inputs are within normal
ranges, as determined by user-configurable failure settings, the primary
command shall be selected and used. If the input position commanded varies by
more than the configured maximum difference, then one will be flagged as failed
and the other command will be used. The selected (primary or backup) command
is user-configurable. In addition, a tracking error can be utilized to ensure the
inputs are tracking each other.
The following operating status indication is provided on the Service Tool and over
CAN.
Primary Demand Used
—Indicates the primary demand is selected and the
backup demand is either not used or not failed.
Primary Demand Used, Backup Failed
—Indicates the primary demand is
selected and the backup demand is failed, indicating the backup signal is out of
range or exceeds the demand difference from the primary.
Backup Demand Used, Primary Failed
—Indicates the backup demand is
selected and the primary demand is failed. The failed may indicate the signal is
out of range or exceeds demand difference from the backup. Note that the
chosen input when the difference is exceeded is configurable.
Primary Enabled but not active
—Indicates the backup demand is selected but
the primary demand will become active after a 10 second signal healthy delay.