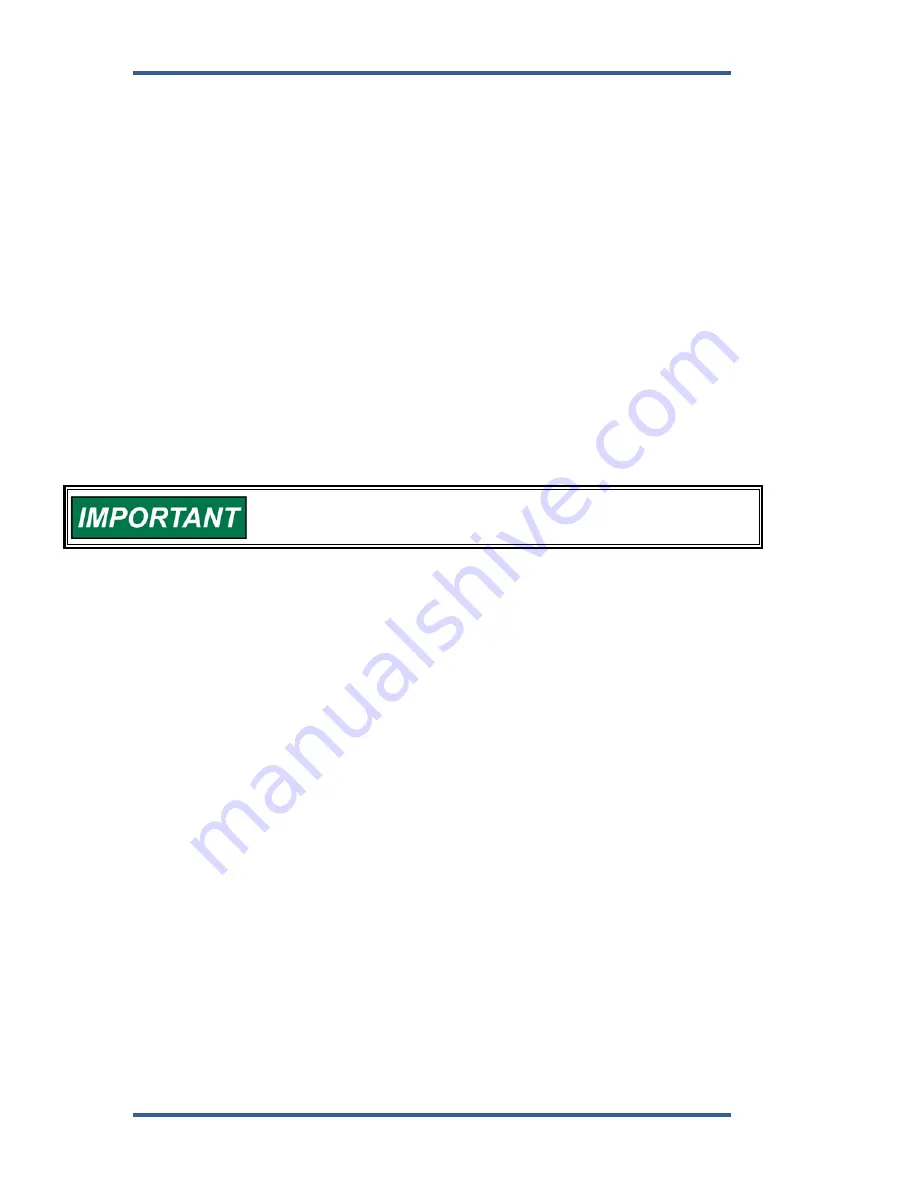
ProAct P-Series FL Position Controller
Manual 26659
8
Woodward
Temperature
The ProAct P-Series FL is designed to operate within a temperature range of
–40 °C to +85 °C (–40 °F to +185 °F). However, maintaining the actuator
operating temperature near normal ambient temperatures (~20 °C) reduces the
input and output temperature drift and improves actuator life (MTTF).
Heat Sink Capability
The ProAct P-Series FL generates heat, especially when stalled or during other
conditions requiring maximum torque output. The installer must consider the heat
conductivity of the installation bracket, and the operating temperature of the
ultimate heat sink to which the bracket will be attached.
The thermal design of the ProAct P-Series FL is based on the cooling of critical
electrical components coupled to the aluminum frame of the actuator. If a
temperature of 90 °C is maintained at the mounting surfaces, the temperature of
the electronics will remain within acceptable limits. Therefore, when applying the
ProAct P-Series FL, the temperature at the mounting bracket must not exceed 90
°C regardless of the surrounding thermal conditions. If the temperature of this
zone exceeds 90 °C, the actuator will limit the available torque to compensate.
The CSA hazardous location listing is not applicable if the
surrounding air ambient temperature exceeds 85 °C.
Mounting the ProAct P-Series FL
Models II through IV actuators may be installed on a bracket in either base or
flange mount configuration with the exception of the model IV. The mass of the
model IV requires that it be mounted only in the base mount configuration.
The base mount configuration requires the use of four M8x1.25 screws with a
minimum engagement of 16 mm. The flange mount configuration requires the
use of four M8 screws through the flange. Whether base mounting or flange
mounting the actuator, torque the four M8 screws to 22.6 N-m (200 lb-in). Both
mounting features are shown in Figure 1-1. The actuator can be mounted in any
attitude. All exterior and mounting dimensions and exterior fasteners are metric.
The brackets and attaching hardware must be designed to hold the weight and to
withstand the vibration associated with engine mounting.
The ProAct P-Series FL weighs approximately:
Model II
11 kg (25 lb)
Model III
15 kg (32 lb)
Model IV
24 kg (52 lb)
As shown in Specifications, the ProAct P-Series FL actuators have been
designed for and verified to a given accelerated life vibration test level at the
mounting surface of the actuator. The user should be aware that in any
application, bracket design can significantly change the vibration levels at the
actuator. Therefore, every effort should be made to make the bracket as stiff as
possible so that engine vibrations are not amplified, creating an even more
severe environment at the actuator. Additionally, when possible, orienting the
actuator shaft parallel to the crankshaft of the engine will often reduce the
vibration load on the actuator's rotor system in reciprocating engine applications.