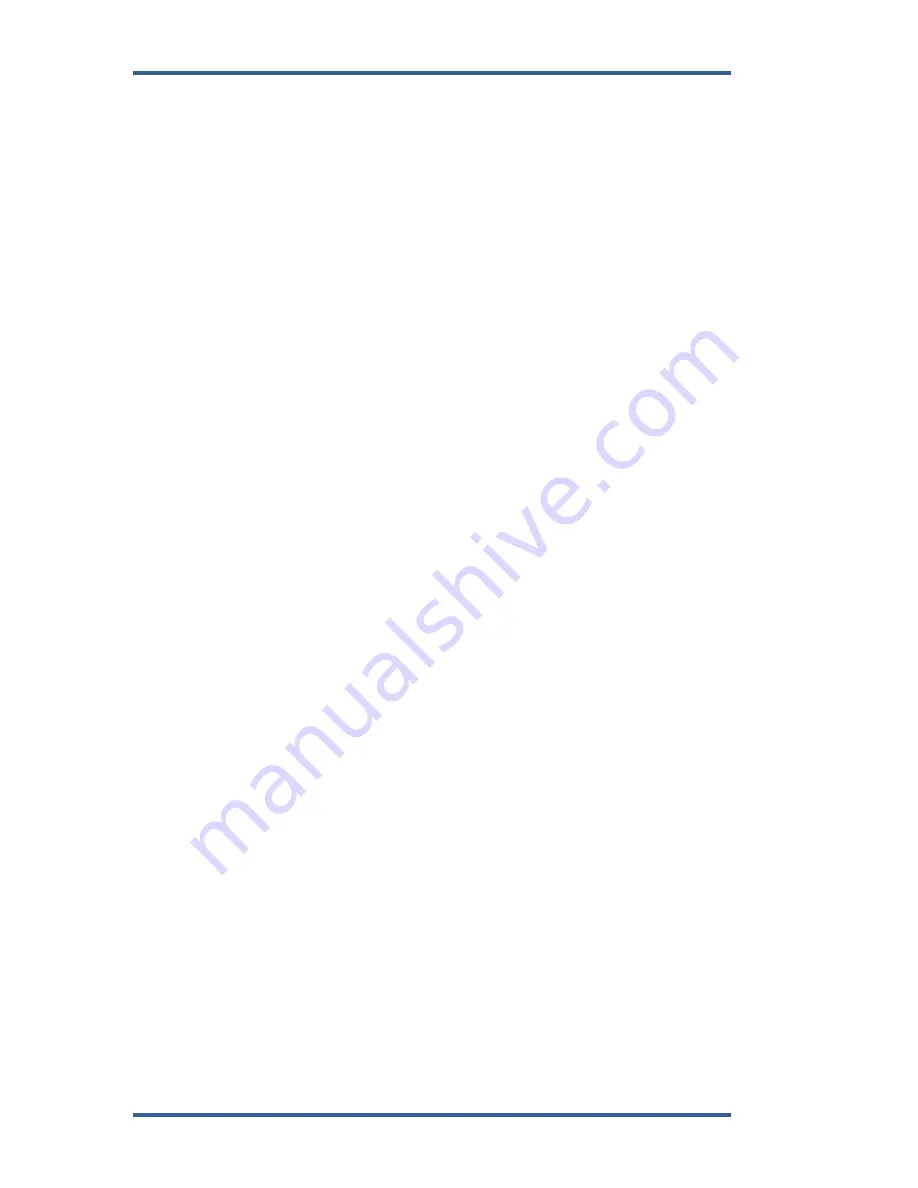
ProAct P-Series FL Position Controller
Manual 26659
2
Woodward
Introduction
The ProAct P-Series FL provides a building block approach to total engine
management. The modular bi-directional actuator design easily attaches to fuel
pumps, fuel valves, or throttle bodies. There are three ProAct P-Series FL
models (II, III, IV) that provide a wide range of work outputs. Available ITBs
(integrated throttle bodies) include 85, 95, 105, 120, 135, 160, and 180 mm
versions.
Two similar variations of the P-Series are available, the standard version and the
FL version. The standard ProAct P-Series FL, covered by manual 26578, utilizes
a 24-pin circular connector for customer I/O, while the FL version has terminal
block connections. The FL (flex) version can be adapted into a variety of existing
systems by adding a connector kit or by directly landing wires to terminal blocks.
The P-Series FL also provides additional options of (0 to 200) mA Analog Input
range and (0 to 5) V (dc) Analog Output range.
Woodward also offers a ProAct version for speed control applications. Refer to
manual 26246, ProAct ISC—Integrated Speed Control. The ProAct ISC is a
microprocessor-based speed control incorporated into the actuator, creating a
single integrated actuator/speed control. This eliminates the need for an
additional driver box and speed control box.
The ProAct P-Series FL is a positioning device that accepts a position command
and drives the 0 to 75 degree output shaft to the commanded position based on
an internal shaft position sensor. The high-efficiency torque motor delivers up to
10.4 N
m (92 lb-in), for a Model IV, nominally over 75° travel range to operate
fuel or air control devices. See specifications in the Appendix for torque
performance of all actuator model sizes over the full product temperature range.
The ProAct P-Series FL actuator accepts either a PWM command, a CAN
command, or an analog command for output shaft positioning. The analog
command input signal range is jumper selectable for (0 to 5) V (dc), (4 to 20) mA,
or (0 to 200) mA. The position command input can also be set up with a primary
and a backup input, providing redundancy. Automatic failover and fallback logic
is provided when using redundant position commands.
For status purposes, a relay driver output is available that changes state
whenever a fault or error condition is experienced by the ProAct P-Series FL
actuator.
An analog position output signal provides an external position indication after
installation and while the unit is operating. It is jumper-selectable as either
(4 to 20) mA or (0 to 5) V (dc).
Input power is nominally 24 V (dc) (18 V to 32 V), but the device is functional in
the range of (8 to 40) V (dc) for short periods (e.g., starting or transients);
however, accuracy and/or torque can be diminished at the extreme ends of this
range.
Product configuration and tuning is performed using a PC-based Service Tool.
More detail on the features of the ProAct P-Series FL can be found later in this
manual.