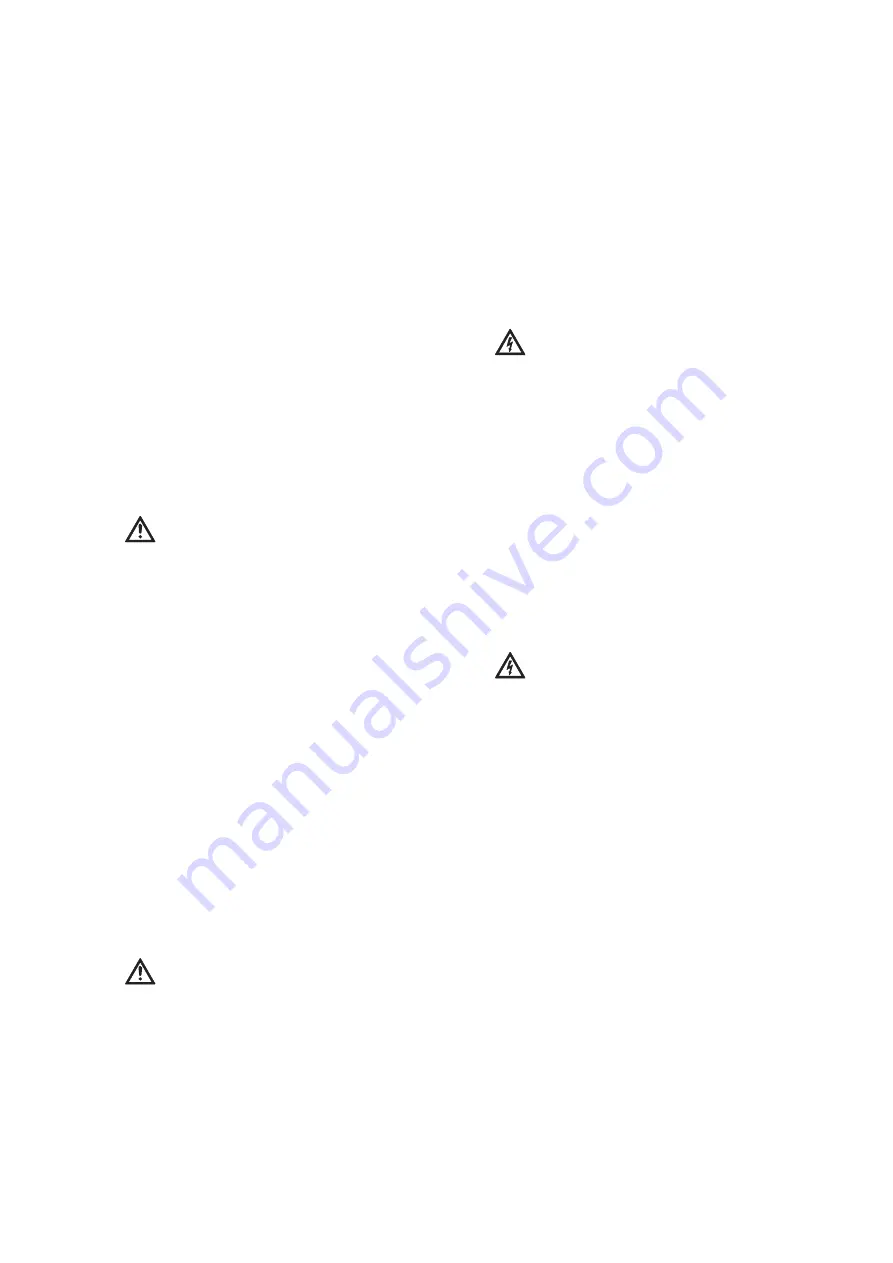
English
32
WILO SE 07/2019
8 Commissioning/decommissioning
We recommend that the initial commissioning of
the system is performed by Wilo’s customer ser-
vice. Contact your dealer, your nearest Wilo repre-
sentative or contact our central customer service
department directly for details.
8.1 General preparations and control measures
Check that all on-site wiring has been performed
correctly, in particular the earthing, prior to the
initial start-up.
• Check that the pipe joints are stress-free.
• Restore all connections between break tank and
pump module (chapter 7.2.2).
Visual inspection of whether the bypass line
(Fig. 1a/b and Fig. 11, item 15) is steadily rising
from the pump to the break tank.
• Remove the securing mechanism (49) on the float
valve (30) (Fig. 10a/10b).
• Filling the system and pipes via the float valve in
the break tank as well as checking for leakages as
well as safe closing of the float valves by visual
inspection.
• The pumps are automatically vented using the
bypass line.
CAUTION! Risk of damage!
Do not allow the pump to run dry. Running dry
will destroy the mechanical seal.
• Check the diaphragm expansion tank (8) for a cor-
rectly adjusted supply pressure (Fig. 4a/b and 5). In
this case, depressurise the tank on the water side
[(close the flow-through fixture or shut-off
device (Fig. 4a, item A) and allow the residual
water to drain (Fig. 4, item B)].
Now check the gas pressure on the air valve (top;
remove the dust cap) of the diaphragm expansion
tank by means of an air pressure gauge (Fig. 4b,
item C), if necessary, correct the pressure if too
low, [(PN 2 = pump start-up pressure pmin
minus 0.2 ... 0.5 bar) or value according to the
table on the tank (Fig. 5)] by filling up with nitro-
gen (Wilo customer service)). If the pressure is too
high, release nitrogen from the valve until the
required value is reached. Then replace the pro-
tective cap, close the drainage valve and open the
flow-through fixture/shut-off device.
• With system pressures greater than PN 16, the
manufacturer’s filling instructions given in the
attached installation and operating instructions
must be observed for the diaphragm expansion
tank.
DANGER! Risk of fatal injury!
Excessive supply pressure (nitrogen) in the dia-
phragm expansion tank can lead to damage or
destruction of the tank and thereby also to per-
sonal injury.
The safety measures for the handling of pres-
surised vessels and technical gases must be
observed.
The pressure specifications in this documenta-
tion (Fig. 5) are made in bar(!). If other units of
pressure measurement are used, always be sure
to convert the figures correctly!
• Check that there is sufficient water in the break
tank.
• Check position of the dry-running protection
(low water sensor) in the tank.
• Position the float switch for the protection against
low water level in the break tank so that the signal
is correctly reported at minimum water level
(check).
• Direction of rotation on the pump motor: Switch
on briefly to check whether the direction of rota-
tion of the pumps (direction of rotation fan wheel)
matches the arrow on the rating plate of the
pump. Swap 2 phases if the direction of rotation is
incorrect.
DANGER! Risk of fatal injuries!
Switch off the system’s main switch before
swapping the phases.
• Check the motor protection to make sure that the
right rated current is set according to the specifi-
cations on the motor rating plate. Observe the
installation and operating instructions for the
control device when doing so.
• Check and set the operating parameters required
on the control device according to the attached
installation and operating instructions.
If necessary, the setting of the pressure switch
must be checked and corrected as an adjustment
to the required parameters. This setting is tuned
at the factory for the optimum volumetric flow
rate for operation without supply pressure (only
water column as a result of the determined level in
the break tank).
DANGER! Risk of fatal injuries!
Contact with live components can cause death!
Use an insulated screwdriver when setting the
pressure switch.
Proceed as follows when setting the pressure
switch:
Pressure switch type FF4....(Fig. 3)
• Open the pressure switch cover by unscrewing the
screw plug and remove the cover.
• Open the gate valve on the pressure side and one
tap.
• Set the switch-off pressure using the
adjusting
screw
(item 19). The pressure can be read in bar on
the
dial
(item 24). Factory setting is as shown on
the attached acceptance test certificate.
• Slowly close the tap.
• Monitor the deactivation point on the pressure
gauge and correct it if necessary by turning the
adjusting screw
(item 19).
• Slowly open the tap.
• Set the start-up pressure using the
adjusting
screw
(item 20). The pressure difference can be
read on the
dial
(item 25). (The factory setting for
the pressure difference
Δ
p between deactivation
and start-up pressure is about 1.0 bar.)
• Close the tap again.
• Replace the pressure switch cover and tighten the
screw plug.
Summary of Contents for FLA Compact-1 Helix V16
Page 2: ...Fig 1a Fig 1b...
Page 3: ...Fig 2a Fig 2b...
Page 4: ...Fig 3...
Page 5: ...Fig 4a...
Page 6: ...Fig 4b C Fig 5...
Page 7: ...Fig 6a Fig 6b...
Page 8: ...Fig 7a Fig 7b...
Page 9: ...Fig 8a...
Page 10: ...Fig 8b...
Page 11: ...Fig 9a Fig 9b...
Page 12: ...Fig 10a Fig 10b...
Page 13: ...Fig 10c Fig 10d...
Page 14: ...Fig 11...
Page 55: ...Fran ais Notice de montage et de mise en service Wilo FLA Compact 41...
Page 73: ...Fran ais Notice de montage et de mise en service Wilo FLA Compact 59...