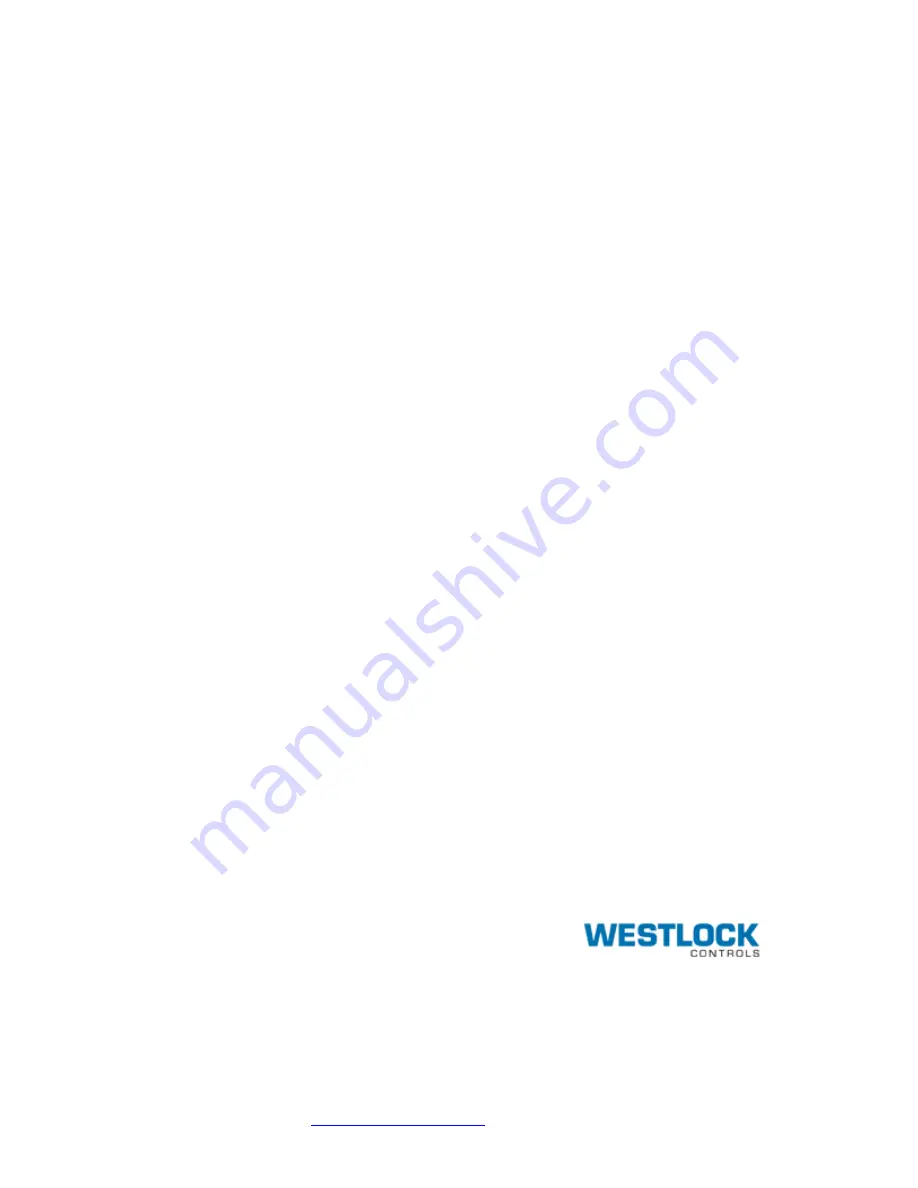
5/12/2017
TECH-538/D.W.O. 23160
Page 189 of 189
Westlock, ICoT are marks owned by one of the companies by the Westlock Controls business.
All other marks are the property of their respective owners.
The contents of this publication are presented for informational purposes only, and while every effort has been
made to ensure their accuracy, they are not to be construed as warranties or guarantees, express or implied,
regarding the products or services described herein or their use or applicability. Westlock reserve the right to
modify or improve the designs or specifications of such products at any time without notice.
Neither Westlock nor any of their affiliated entities assumes responsibility for the selection, use and maintenance
of any product. Responsibility for the selection, use and maintenance of any product remains with the purchaser
and end-user.
USA
Westlock Controls Corp.
280 North Midland Ave. Ste 258
Saddle Brook, NJ 07663
© Westlock Controls Corp All rights reserved