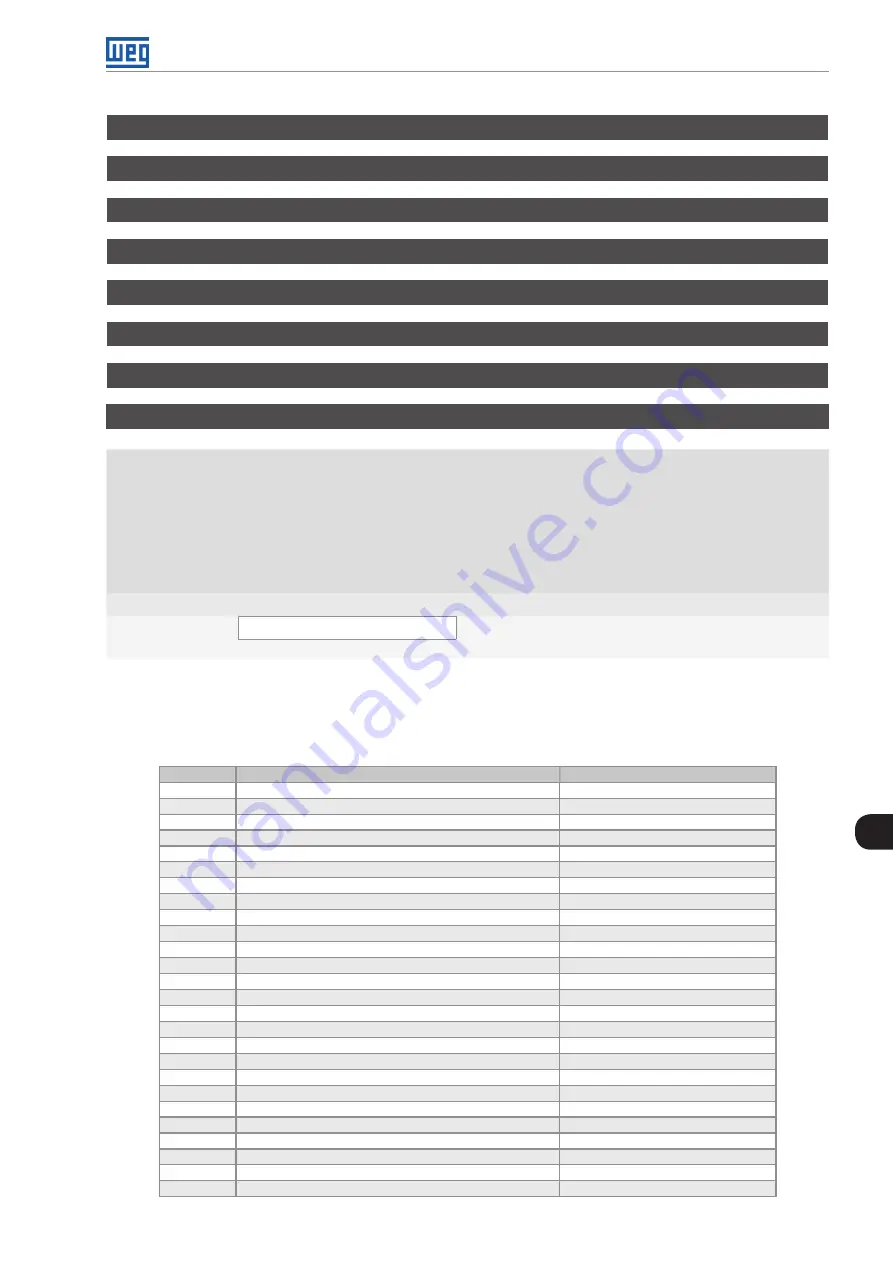
Digital and Analog Inputs and Outputs
CFW501 | 12-17
12
P0263 – Function of Digital Input DI1
P0264 – Function of Digital Input DI2
P0265 – Function of Digital Input DI3
P0266 – Function of Digital Input DI4
P0267 – Function of Digital Input DI5
P0268 – Function of Digital Input DI6
P0269 – Function of Digital Input DI7
P0270 – Function of Digital Input DI8
Adjustable
Range:
0 to 25
Factory
Setting:
P0263 = 1
P0264 = 0
P0265 = 20
P0266 = 21
P0267 = 0
P0268 = 0
P0269 = 0
P0270 = 0
Properties:
cfg
Access groups
via HMI:
I/O
Description:
These parameters allow configuring the digital input function, according to the adjustable range listed in
12.8: Digital input functions on page 12-17
.
Table 12.8:
Digital input functions
Value
Description
Dependence
0
Not Used
-
1
Run/Stop Command
P0224 = 1 or P0227 = 1
2
General Enable Command
P0224 = 1 or P0227 = 1
3
Quick Stop Command
P0224 = 1 or P0227 = 1
4
Forward/Reverse
P0223 = 4 or P0226 = 4
5
Local/Remote Selection
P0220 = 4
6
JOG
P0225 = 2 or P0228 = 2
7
SoftPLC
Prog. SoftPLC
8
2
nd
Ramp Selection
P0105 = 2
9
Not Used
-
10
Not Used
-
11
Not Used
-
12
No External Alarm
-
13
No External Fault
-
14
Reset
Active fault
15
Disab. Flying-Start
P0320 = 1 ou 3
16
Not Used
-
17
Lock Programming
-
18
Load User 1
Inverter disabled
19
Load User 2
Inverter disabled
20
Auto/Man main PID (1)
-
21
Auto/Man external PID (1)
-
22
Not Used
-
23
Bypass Mode
-
24
Activate Fire Mode
-
25
PTC
-
(1)
For digital inputs DI5, DI6, DI7 and DI8, those options do not present associated functions.
Summary of Contents for CFW501 V1.8X
Page 2: ......
Page 8: ...Summary...
Page 34: ...General Information 2 4 CFW501 2...
Page 38: ...About the CFW501 3 4 CFW501 3...
Page 42: ...HMI and Basic Programming 4 4 CFW501 4...
Page 58: ...Identification of the Inverter Model and Accessories 6 4 CFW501 6...
Page 72: ...Logical Command and Speed Reference 7 14 CFW501 7...
Page 76: ...Available Motor Control Types 8 4 CFW501 8...
Page 108: ...Functions Common to all the Control Modes 11 14 CFW501 11...
Page 134: ...Digital and Analog Inputs and Outputs 12 26 CFW501 12...
Page 148: ...Faults and Alarms 14 12 CFW501 14...