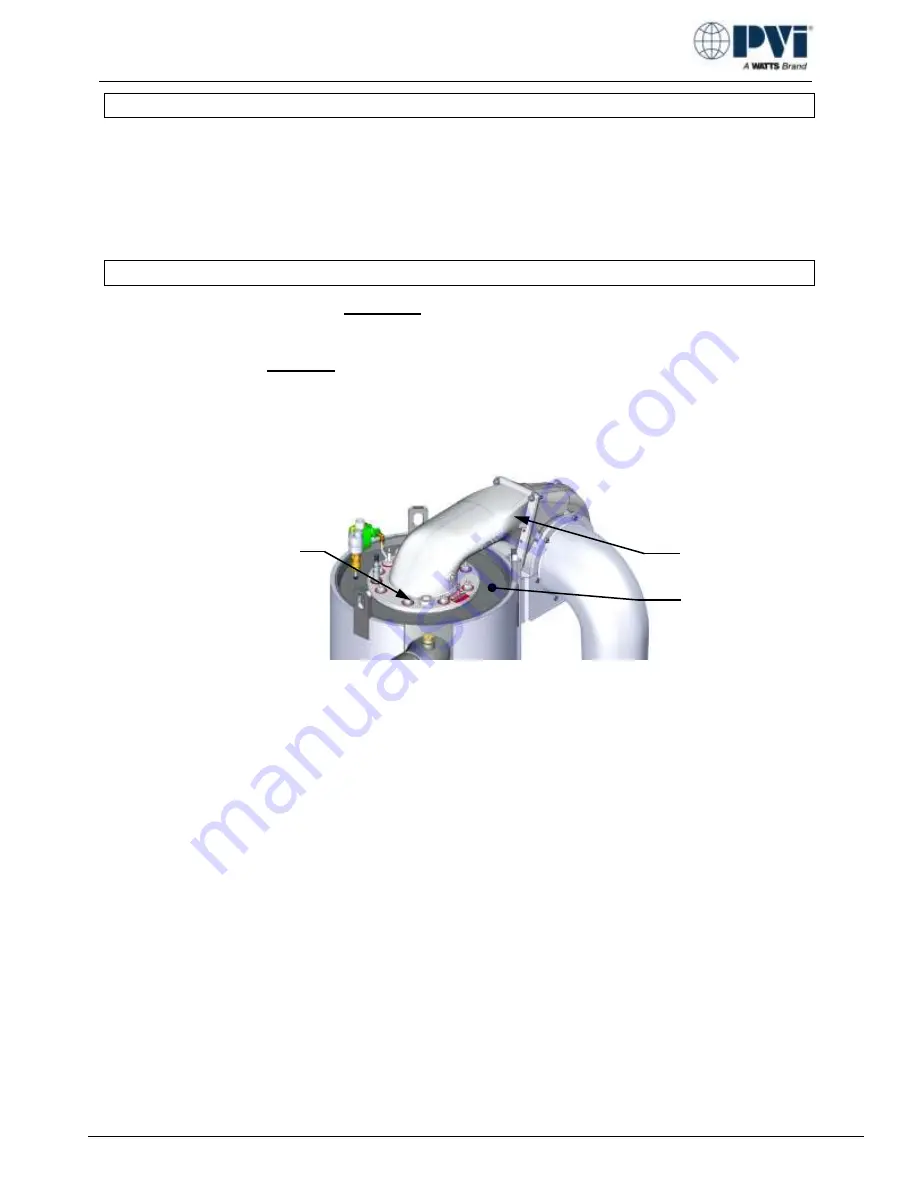
Centurion Water Heater- Edge [ii]: Install-Operation-Service
SECTION 7: MAINTENANCE
OMM-0153_A
• 8/25/2022 Technical Support • (800) 526-0288 • Mon-Fri, 8 am - 5 pm EST Page 69 of 131
7.5 SAFETY DEVICE TESTING
Systematic and thorough tests of the operating and safety devices should be performed to
ensure that they are operating as designed. Certain code requirements, such as ASME CSD-1,
require that these tests be performed on a scheduled basis. Test schedules must conform to
local jurisdictions. The results of the tests should be recorded in a log book. See Section 7 for a
description of and instructions for performing these tests.
7.6 BURNER INSPECTION
The burner assembly should be
inspected
every 24 months to ensure that all components are
intact and functioning as designed. This requires the replacement the burner gasket and blower
and gas train O-Rings, which are included in the 24 Month Maintenance Kit. If the burner is not
fully intact, it must be
replaced
as soon as possible.
The burner assembly is located at the top of the unit's heat exchanger. The burner assembly
may be hot. Therefore, allow the unit to cool sufficiently before removing the burner assembly.
Burner inspection parts are included all 24 Month Maintenance Kit. Instructions are in the
Technical Instruction Documents (TID) included with the kit.
Figure 7-4: Burner Assembly Mounting Details
BLOWER GASKET
BURNER PLATE
3/8”
-16
HEX NUTS
(8 each)