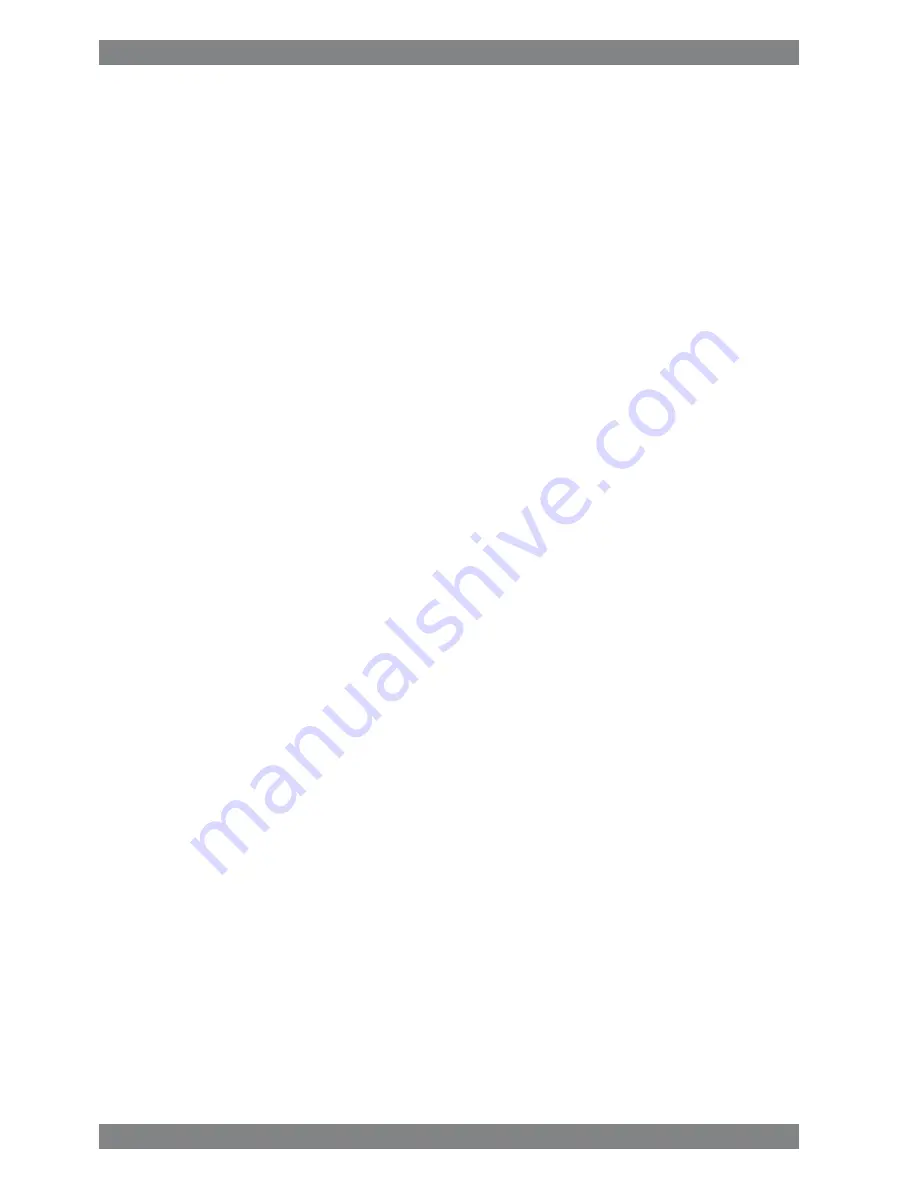
number of through-flows of tank volume per day: 5 for HFO, 4 for MDF
n =
operating time [h/day]: 24 for continuous separator operation, 23 for normal dimensioning
t =
Sludge tank (2T06)
The sludge tank should be located directly beneath the separators, or as close as possible
below the separators, unless it is integrated in the separator unit. The sludge pipe must be
continuously falling.
7.3.1.2
Renovating oil tank (2T04)
In case of wet sump engines the oil sump content can be drained to this tank prior to separation.
7.3.1.3
Renovated oil tank (2T05)
This tank contains renovated oil ready to be used as a replacement of the oil drained for
separation.
7.3.2
System oil tank (2T01)
Recommended oil tank volume is stated in chapter Technical data.
The system oil tank is usually located beneath the engine foundation. The tank may not protrude
under the reduction gear or generator, and it must also be symmetrical in transverse direction
under the engine. The location must further be such that the lubricating oil is not cooled down
below normal operating temperature. Suction height is especially important with engine driven
lubricating oil pump. Losses in strainers etc. add to the geometric suction height. Maximum
suction ability of the pump is stated in chapter Technical data.
The pipe connection between the engine oil sump and the system oil tank must be flexible to
prevent damages due to thermal expansion. The return pipes from the engine oil sump must
end beneath the minimum oil level in the tank. Further on the return pipes must not be located
in the same corner of the tank as the suction pipe of the pump.
The suction pipe of the pump should have a trumpet shaped or conical inlet to minimise the
pressure loss. For the same reason the suction pipe shall be as short and straight as possible
and have a sufficient diameter. A pressure gauge shall be installed close to the inlet of the
lubricating oil pump. The suction pipe shall further be equipped with a non-return valve of flap
type without spring. The non-return valve is particularly important with engine driven pump
and it must be installed in such a position that self-closing is ensured.
Suction and return pipes of the separator must not be located close to each other in the tank.
The ventilation pipe from the system oil tank may not be combined with crankcase ventilation
pipes.
It must be possible to raise the oil temperature in the tank after a long stop. In cold conditions
it can be necessary to have heating coils in the oil tank in order to ensure pumpability. The
separator heater can normally be used to raise the oil temperature once the oil is pumpable.
Further heat can be transferred to the oil from the preheated engine, provided that the oil
viscosity and thus the power consumption of the pre-lubricating oil pump does not exceed
the capacity of the electric motor.
7-14
Wärtsilä 32 Product Guide - a21 - 7 September 2016
Wärtsilä 32 Product Guide
7. Lubricating Oil System
Summary of Contents for WARTSILA32
Page 18: ...This page intentionally left blank...
Page 72: ...This page intentionally left blank...
Page 130: ...This page intentionally left blank...
Page 150: ...This page intentionally left blank...
Page 186: ...This page intentionally left blank...
Page 204: ...This page intentionally left blank...
Page 210: ...This page intentionally left blank...
Page 216: ...This page intentionally left blank...
Page 238: ...This page intentionally left blank...
Page 246: ...This page intentionally left blank...
Page 248: ...This page intentionally left blank...
Page 251: ......
Page 252: ......
Page 253: ......