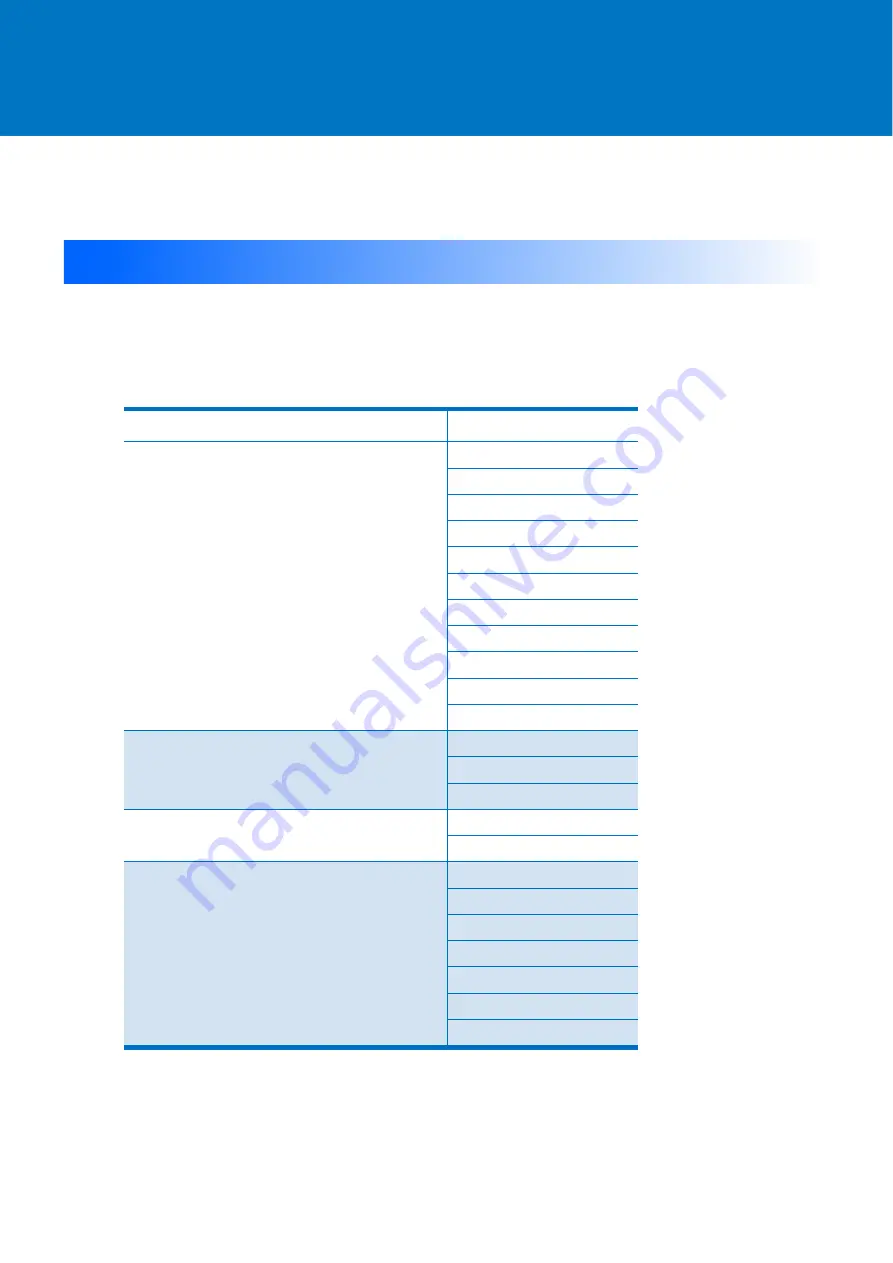
52
YO20-0938-DI-001-00
Appendix
The list of parts that must be replaced during an overhaul is as follows. The replacement timing differs
depending on the part. The recommended replacement periods indicated in the table below are for reference.
Actual periods may differ depending on usage conditions and the environment.
Table 14:
Major replacement parts
Category
Parts Name
Parts that must be replaced during an overhaul
Bearing
Power lock
Cooling water piping
O-ring
Lubricating oil
Oil seal
Level gauge
Check valve
Parallel key
LAN cable
Vibration-proof rubbers
Parts that must be replaced every two years
Bearing case
Seal sleeve
Slinger
Parts that must be replaced every three years
Inverter
Cooling fan
Parts that must be replaced every five years
Cylinder
Rotor shaft
Side cover
Motor
Timing gear
Controller
Noise filter
Major Replacement Parts
Summary of Contents for MS120A
Page 2: ......
Page 10: ......
Page 14: ......
Page 47: ...33 YO20 0938 DI 001 00 Figure 16 I O block diagram for remote control wiring...
Page 65: ...51 YO20 0938 DI 001 00 7 2 External Dimensions Figure 17 External dimensions of MS120A MS120A...
Page 67: ...53 YO20 0938 DI 001 00...
Page 68: ...54 YO20 0938 DI 001 00...
Page 69: ...55 YO20 0938 DI 001 00...