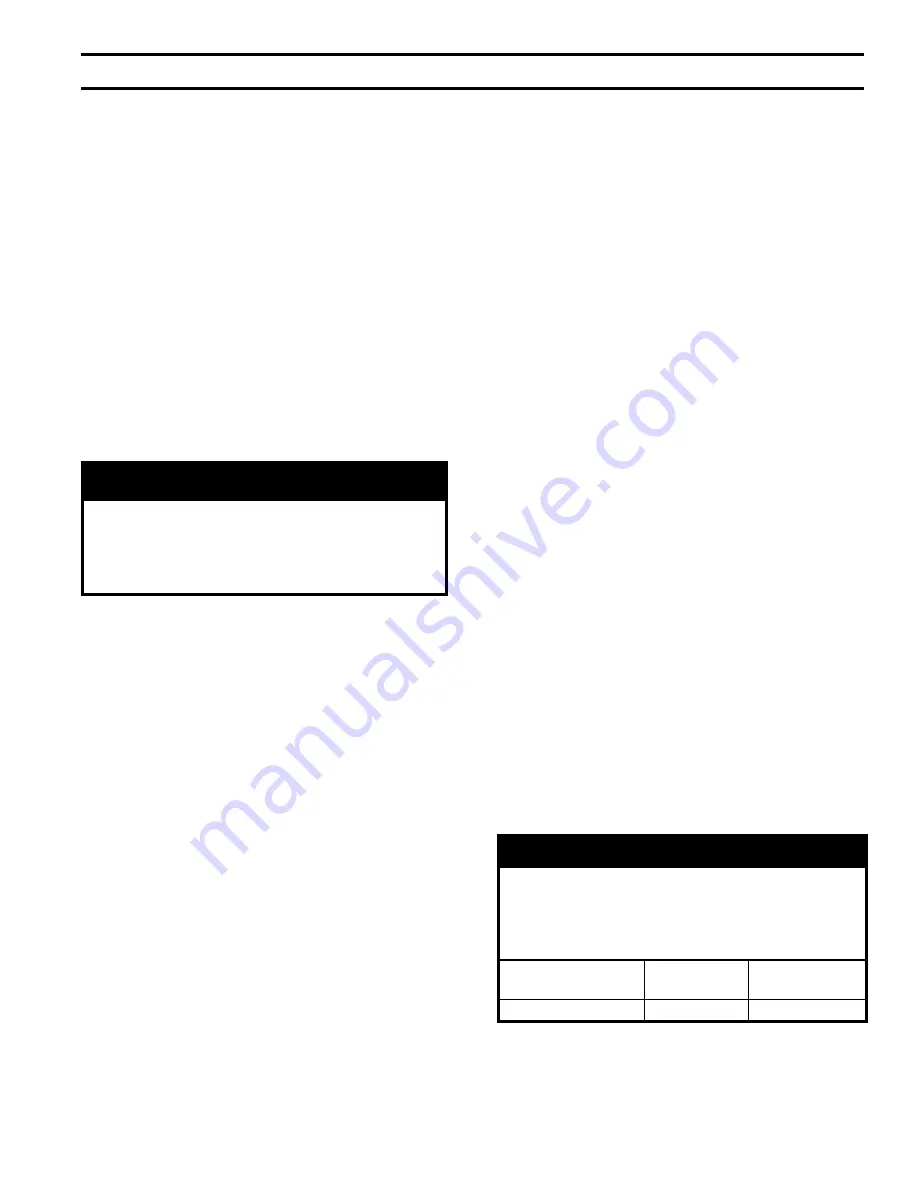
39
X. mAINTENANCE AND SERVICE INSTRUCTIONS
A.
WATER BOILERS:
1.
Filling of boiler and system.
GENERAL
—
In a hot water heating system, the
boiler and entire system (other than the expansion
tank) must be full of water for satisfactory opera-
tion. Water should be added to the system until the
boiler pressure gauge registers 12 psi. To insure that
the system is full, water should come out of all air
vents when opened.
2. BOILING OUT OF BOILER AND SySTEM
.
The
oil and grease which accumulate in a new hot water
boiler can be washed out in the following manner:
a. Ideally, shut off valves have been installed
between the boiler return manifold and the rest
of the system, to minimize the amount of system
draining.
b. Drain the boiler to a level below the relief valve
tapping.
DANGER
Assure that the boiler is at zero pressure before
removing the relief valve. Open the safety valve
to relieve all internal pressure prior to proceeding.
Safety valve discharge piping must be piped such
that the potential for burns is eliminated.
c. Remove relief valve using extreme care to avoid
damaging it.
d. Add an appropriate amount of recommended boil
out compound.
e. Replace relief valve.
f. Fill the entire system with water.
g. Start firing the boiler.
h. Circulate the water through the entire system.
i. Vent the system, including the radiation.
j. Allow boiler water to reach operating tempera-
ture, if possible.
k. Continue to circulate the water for a few hours.
l. Stop firing the boiler.
m. Drain the system in a manner and to a location
that hot water can be discharged with safety.
n. Remove plugs from all available returns and
wash the water side of the boiler as thoroughly as
possible, using a high-pressure water stream.
o. Refill the system with fresh water.
3. Add appropriate boiler water treatment compounds
as recommended by your qualified water treatment
company.
4. Make pH or Alkalinity Test.
After boiler and system have been cleaned and
refilled as previously described, test the pH of the
water in the system. This can easily be done by
drawing a small sample of boiler water and testing
with hydrion paper which is used in the same
manner as litmus paper, except it gives specific read
-
ings. A color chart on the side of the small hydrion
dispenser gives the reading pH. Hydrion paper is
inexpensive and obtainable from any chemical
supply house or through your local druggist. The pH
should be higher than 7 but lower than 11. Add some
of the washout chemical (caustic soda), if necessary,
to bring the pH within the specified range. With this
lower level of protection, care must be exercised to
eliminate all of the free oxygen in the system.
5. Boiler is now ready to be put into service.
B.
EXCESSIVE MAKE-UP WATER
A leaky system will increase the volume of make-up
water supplied to the boiler, which can significantly
shorten the life of the boiler. Entrained in make-up
water are dissolved minerals, salts and oxygen. When
the fresh, cool make-up water is heated in the boiler, the
minerals fall out as sediment, the salts coat the inside of
the boiler, and the oxygen escapes as a gas. The
accumulation of sediment eventually isolates the water
from contacting the steel. When this happens the steel
in that area gets extremely hot and eventually cracks.
The presence of free oxygen or chloride salts in the
boiler creates a corrosive atmosphere which, if the
concentration becomes high enough, can corrode the
steel through from the inside. More make-up water and
higher concentrations of contaminants damage the
boiler sooner.
Our warranty does not cover
corrosion and sediment-related damage.
Clearly it is
in everyone’s best interest to prevent this type of
failure. you can do your part by ensuring that your
system is leak-free, keeping leakage to less than 2
percent of the boiler water volume each month. Refer
to Chart below.
ImPORTANT
IF, DURING NORmAL OPERATION, IT IS
NECESSARy TO ADD mORE WATER THAN
INDICATED BELOW, CONSULT A qUALIFIED
SERVICE TECHNICIAN TO CHECK yOUR SySTEm
FOR LEAKS.
model No.
Gallons Per
month
Gallons Per
year
LEDV1
0.20
2.0
Summary of Contents for LE DV Series
Page 5: ...5 I General Information Figure 1A LEDV Packaged Water Boiler with Beckett AFII Burner ...
Page 6: ...6 I General Information continued Figure 1B LEDV Packaged Water Boiler with Riello BF Burner ...
Page 19: ...19 v venting continued Figure 11 Vent Installation Figure 12 Vent Connector Un Assembled ...
Page 20: ...20 v venting continued Figure 13 Vent Connector Assembled Figure 14 Air Intake Installation ...
Page 48: ...48 xiii Repair Parts continued Figure 29 LEDV Bare Boiler Assembly ...
Page 50: ...50 xiii Repair Parts continued Figure 30 LEDV Boiler Jacket Insulation ...
Page 55: ...55 xiii Repair Parts continued Figure 33 Vent Kit Repair Parts ...
Page 60: ...60 U S Boiler Company Inc P O Box 3020 Lancaster PA 17604 1 888 432 8887 www usboiler net ...