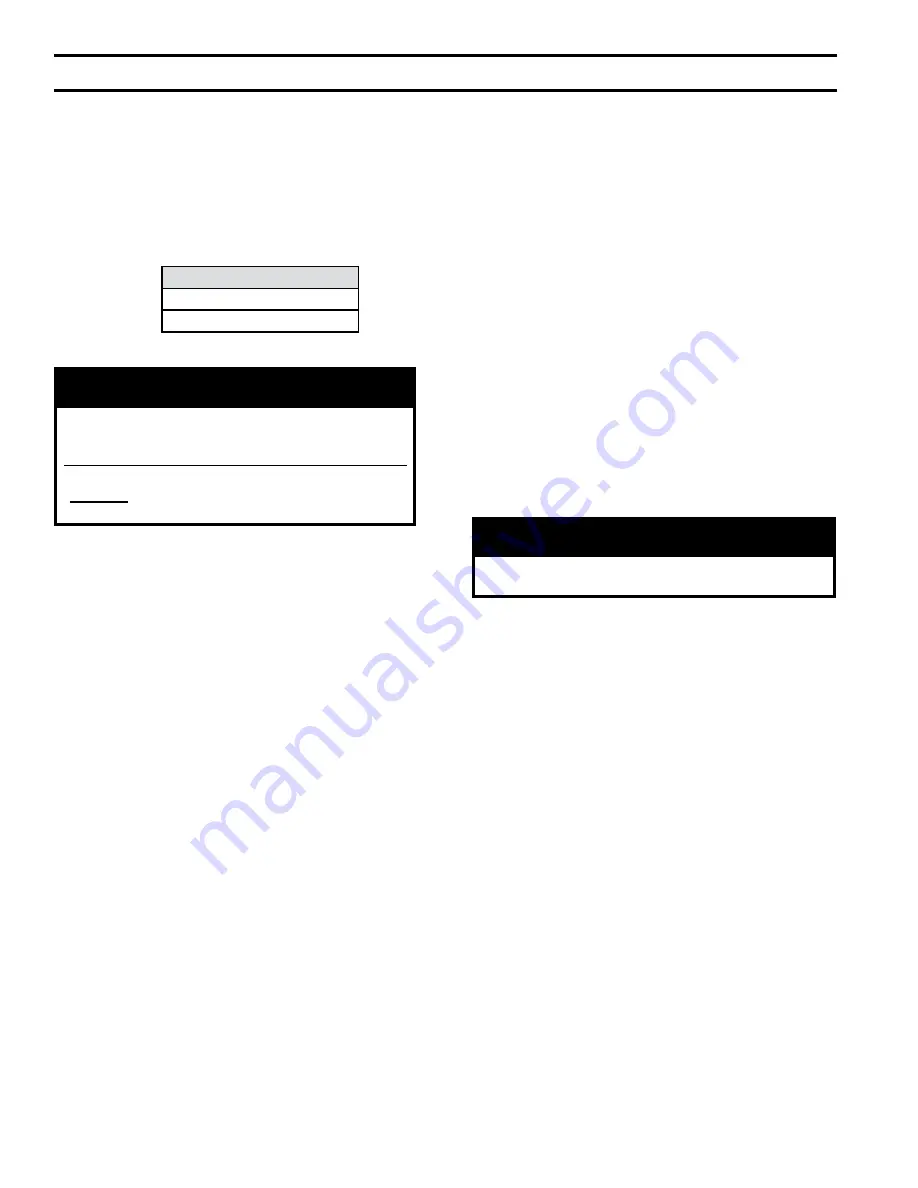
34
VIII. SySTEm START-UP (continued)
vii.
Cad Cell Resistance Check
:
For proper
operation it is important that the cad
cell resistance is below 1600 ohms. During
a normal call for heat, the cad cell leads
can be unplugged from the control and the
resistance measured with a meter in the
conventional way.
Conduct these tests with flame present, see
chart below.
Flame Detection Range
Normal (0 - 1600 ohms)
Limited (1600 ohms to lockout)
3. CHECK OIL PRIMARy CONTROL
CAUTION
Due to the potential hazard of line voltage, only a
trained, experienced service technician should
perform the following safety checks.
This control contains no field-serviceable parts.
DO NOT attempt to take it apart. Replace entire
control if operation is not as described.
a.
Preliminary Steps
•
Check wiring connections and power supply.
•
Make sure power is on to the controls.
•
Make sure limit control is closed.
•
Check contacts between ignitor and the
electrodes.
•
Check the oil pump pressure.
•
Check the piping to the oil tank.
•
Check the oil nozzle, oil supply and oil filter.
b. Check Safety Features
Safe Start:
•
Place a jumper across cad cell terminals.
•
Follow procedure to turn on burner. Burner
must not start, indicator light turns on and
control remains in Idle Mode.
•
Remove jumper.
c. Simulate Ignition or Flame Failure:
•
Follow procedure to turn on burner.
•
Check cad cell resistance. If resistance is
below 1600 OHMS and burner runs beyond
safety cut-out time, cad cell is good.
•
If safety switch shuts down burner and
resistance is above 1600 OHMS, open line
switch to boiler. Access cad cell under ignitor,
clean face of cad cell and see that cell is
securely in socket. Check gasket around
perimeter of ignitor lid for proper seal. If
gasket is missing or damaged, replace gasket.
Room light can effect cad cell resistance. Reset
safety switch.
•
Close line switch to boiler. If burner starts
and runs beyond safety switch cut-off
time, cell is good. If not, install new cell.
•
Close hand valve in oil supply line.
•
Failure occurs, device enters Recycle Mode.
•
Device tries to restart system after
approximately 60 seconds.
•
After third Recycle Mode trial, safety
switch locks out within safety switch
timing indicated on label and control
enters Restricted Mode. Ignition and
motor stop and oil valves closes.
d. Power Failure Check: After Flame is estab-
lished, turn the power off to the control/burner.
The burner should shut down safely. When
power is restored a normal ignition sequence
should be started.
WARNING
Cad Cell Jumper must be removed after this
check.
4. CHECK HIGH LIMIT
a. Adjust system thermostat(s) to highest setting.
b. Allow burner to run until boiler water tempera-
ture exceeds high limit setting. The burner
should shut down and circulators continue
running.
c. Allow the temperature to drop below control
setting. The burner must restart.
d. Boiler installation is not considered complete
until this check has been made.
5. CHECK LOW WATER CUT-OFF CONTROL, if
required on this boiler application. See Appendix
"A" at the rear of this manual for 'How to Test'.
6. CHECK OPERATING CONTROL on boiler
applications equipped with tankless heater(s). With
burner off, draw hot water until burner starts, then
turn off hot water and check burner shut-down.
M.
IF CONTROLS MEET REQUIREMENT
outlined in
Paragraph L.
1. Allow boiler to operate for approximately 30
minute, confirm the boiler and system have no leaks.
N.
IF CONTROLS DO NOT MEET REQUIREMENTS
outlined in Paragraphs L-1 thru L-6, replace control
and repeat checkout procedures.
Summary of Contents for LE DV Series
Page 5: ...5 I General Information Figure 1A LEDV Packaged Water Boiler with Beckett AFII Burner ...
Page 6: ...6 I General Information continued Figure 1B LEDV Packaged Water Boiler with Riello BF Burner ...
Page 19: ...19 v venting continued Figure 11 Vent Installation Figure 12 Vent Connector Un Assembled ...
Page 20: ...20 v venting continued Figure 13 Vent Connector Assembled Figure 14 Air Intake Installation ...
Page 48: ...48 xiii Repair Parts continued Figure 29 LEDV Bare Boiler Assembly ...
Page 50: ...50 xiii Repair Parts continued Figure 30 LEDV Boiler Jacket Insulation ...
Page 55: ...55 xiii Repair Parts continued Figure 33 Vent Kit Repair Parts ...
Page 60: ...60 U S Boiler Company Inc P O Box 3020 Lancaster PA 17604 1 888 432 8887 www usboiler net ...