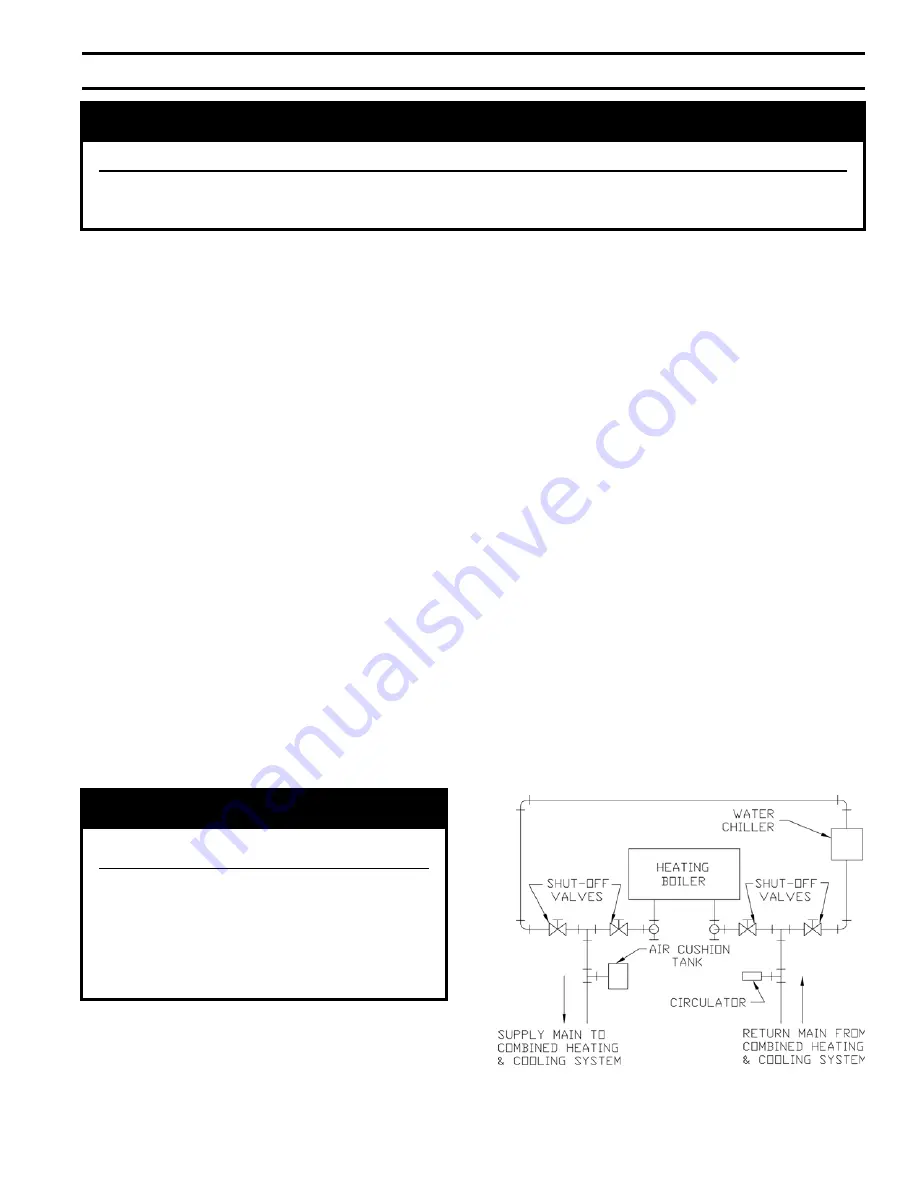
13
IV. WATER PIPING AND TRIm
WARNING
Failure to properly pipe boiler may result in improper operation and damage to boiler or structure.
Oxygen contamination of boiler water will cause corrosion of iron and steel boiler components, and
can lead to boiler failure. U.S. Boiler Company’s Warranty does not cover problems caused by oxygen
contamination of boiler water or scale (lime) build-up caused by frequent addition of water.
A.
DESIGN A PIPING SySTEM and install boiler
which will prevent oxygen contamination of boiler
water and frequent water additions.
1. There are many possible causes of oxygen contami-
nation such as:
a. Addition of excessive make-up water as a result
of system leaks.
b. Absorption through open tanks and fittings.
c. Oxygen permeable materials in the distribution
system.
2. In order to insure long product life, oxygen sources
should be eliminated. This can be accomplished by
taking the following measures:
a. Repairing system leaks to eliminate the need for
addition of make-up water.
b. Eliminating open tanks from the system.
c. Eliminating and/or repairing fittings which allow
oxygen absorption.
d. Use of non-permeable materials in the distribu-
tion system.
e. Isolating the boiler from the system water by
installing a heat exchanger.
3. Connect System supply and return piping to boiler.
See Figures 8A and 8B. Also, consult "I=B=R,
Residential Hydronic Heating Installation and
Design Guide". Maintain minimum ½ inch clear-
ance from hot water piping to combustible materials.
WARNING
System supply and return piping must be
connected to correct boiler pipe.
U.S. Boiler Company recommends sizing
the system circulator to supply sufficient
flow (GPm) to allow a 20°F temperature
differential in the system. When sizing the
system circulator, the pressure drop of all
radiators, baseboard and radiant tubing and
all connecting piping must be considered.
a. Use a system bypass if the boiler is to be
operated in a system which has a large volume or
excessive radiation where low boiler water
temperatures may be encountered (i.e. converted
gravity circulation system, etc.) The bypass
should be the same size as the supply and return
lines with valves located in the bypass and return
line as illustrated in Figures 8A and 8B in order
to regulate water flow for maintenance of higher
boiler water temperature.
Set the bypass and return valves to a half throttle
position to start. Operate boiler until the system
water temperature reaches its normal operating
range.
Adjust the valves to maintain 180°F to 200°F
boiler water temperature and greater the 120°F
return temperature. Adjust both valves simulta-
neously. Closing the boiler return valve while
opening the bypass valve will raise the boiler
return temperature. Opening the boiler return
valve while closing the by-pass valve will lower
the boiler return temperature.
b. If this boiler is used in connection with refrigera-
tion systems, the boiler must be installed so that
the chilled medium is piped in parallel with the
heating boiler using appropriate valves to
prevent the chilled medium from entering the
boiler. See Figure 7. Also, consult "I=B=R,
Residential Hydronic Heating Installation and
Design Guide".
c. If this boiler is connected to heating coils located
in air handling units where they may be exposed
to refrigerated air, the boiler piping must be
equipped with flow control valves to prevent
Figure 7: Recommended Piping for Combination
Heating and Cooling (Refrigeration) System
Summary of Contents for LE DV Series
Page 5: ...5 I General Information Figure 1A LEDV Packaged Water Boiler with Beckett AFII Burner ...
Page 6: ...6 I General Information continued Figure 1B LEDV Packaged Water Boiler with Riello BF Burner ...
Page 19: ...19 v venting continued Figure 11 Vent Installation Figure 12 Vent Connector Un Assembled ...
Page 20: ...20 v venting continued Figure 13 Vent Connector Assembled Figure 14 Air Intake Installation ...
Page 48: ...48 xiii Repair Parts continued Figure 29 LEDV Bare Boiler Assembly ...
Page 50: ...50 xiii Repair Parts continued Figure 30 LEDV Boiler Jacket Insulation ...
Page 55: ...55 xiii Repair Parts continued Figure 33 Vent Kit Repair Parts ...
Page 60: ...60 U S Boiler Company Inc P O Box 3020 Lancaster PA 17604 1 888 432 8887 www usboiler net ...