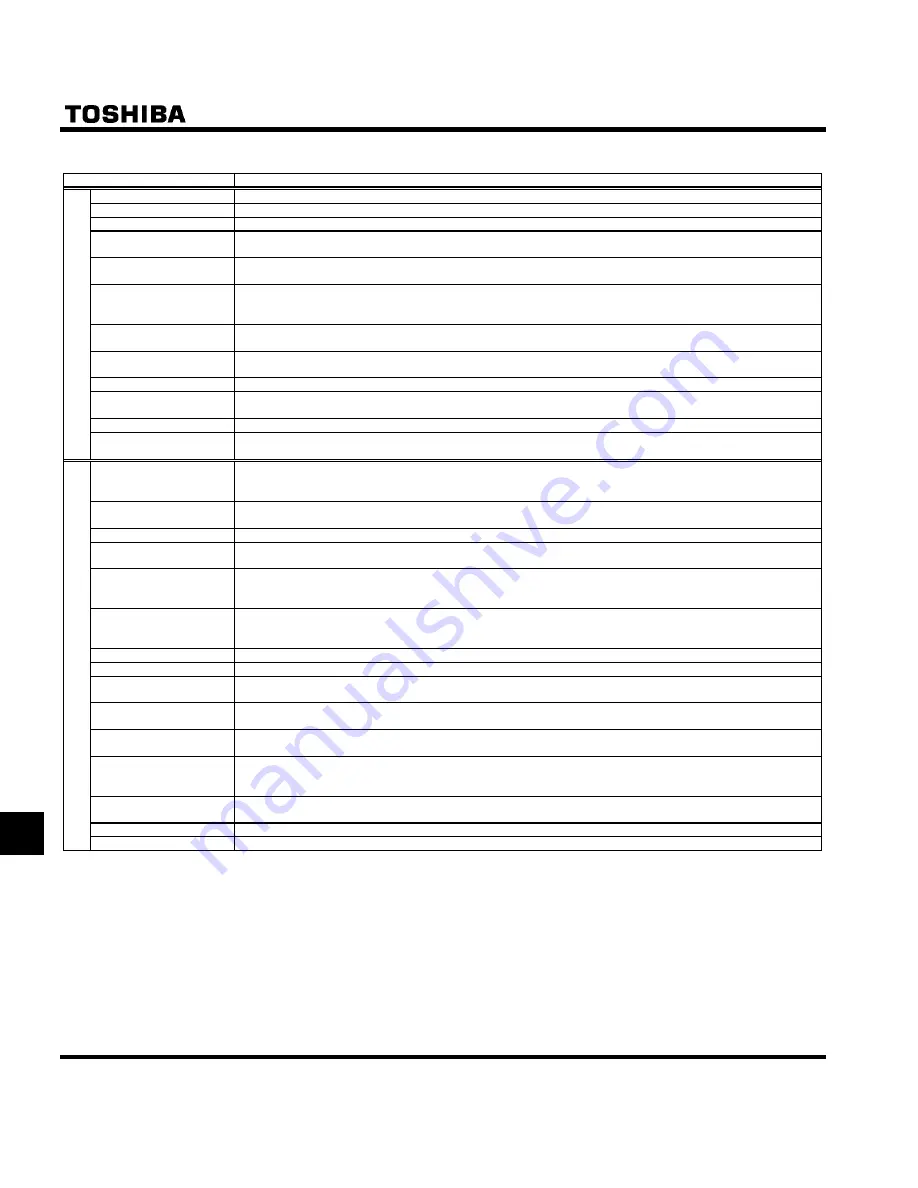
E6581158
L-2
12
Q
Common specification
Item
Specification
Control system
Sinusoidal PWM control
Rated output voltage
Adjustable within the range of 50 to 600V by correcting the supply voltage (not adjustable above the input voltage)
Output frequency range
0.5 to 500.0Hz, default setting: 0.5 to 80Hz, maximum frequency: 30 to 500Hz
Minimum setting steps of
frequency
0.1Hz: operation panel setting, 0.2Hz: analog input (when the max. frequency is 100Hz).
Frequency accuracy
Digital setting: within ±0.01% of the max. frequency (-10 to +60°C)
Analog setting: within ±0.5% of the max. frequency (25°C ±10°C)
Voltage/frequency char-
acteristics
V/f constant, variable torque, automatic torque boost, vector control, automatic energy-saving, dynamic automatic
energy-saving control, PM motor control. Auto-tuning. Base frequency (25 - 500Hz) adjusting to 1 or 2, torque boost
(0 - 30%) adjusting to 1 or 2, adjusting frequency at start (0.5 - 10Hz)
Frequency setting signal
Potentiometer on the front panel, external frequency potentiometer (connectable to a potentiometer with a rated im-
pedance of 1 - 10k
ȍ
), 0 - 10Vdc (input impedance: VIA/VIB=30k
ȍ
, 4 - 20mAdc (Input impedance: 250
ȍ
).
Terminal board base fre-
quency
The characteristic can be set arbitrarily by two-point setting. Possible to set individually for three functions: analog
input (VIA and VIB) and communication command.
Frequency jump
Three frequencies can be set. Setting of the jump frequency and the range.
Upper- and lower-limit
frequencies
Upper-limit frequency: 0 to max. frequency, lower-limit frequency: 0 to upper-limit frequency
PWM carrier frequency
Adjustable within a range of 2.0 to 16.0Hz (default: 12kHz).
P
ri
n
c
ipal c
ont
ro
l
func
ti
ons
PID control
Setting of proportional gain, integral gain, differential gain and control wait time. Checking whether the amount of
processing amount and the amount of feedback agree.
Acceleration/deceleration
time
Selectable from among acceleration/deceleration times 1, 2 and 3 (0.0 to 3200 sec.). Automatic accelera-
tion/deceleration function. S-pattern acceleration/deceleration 1 and 2 and S-pattern adjustable. Control of forced
rapid deceleration and dynamic rapid deceleration
DC braking
Braking start-up frequency: 0 to maximum frequency, braking rate: 0 to 100%, braking time: 0 to 20 seconds, emer-
gency DC braking, motor shaft fixing control
Dynamic braking
Control and drive circuit is built in the inverter with the braking resistor outside (optional).
Input terminal function
(programmable)
Possible to select from among 65 functions, such as forward/reverse run signal input, jog run signal input, operation
base signal input and reset signal input, to assign to 8 input terminals. Logic selectable between sink and source.
Output terminal functions
(programmable)
Possible to select from among 58 functions, such as upper/lower limit frequency signal output, low speed detection
signal output, specified speed reach signal output and failure signal output, to assign to FL relay output, open col-
lector output and RY output terminals.
Forward/reverse run
The RUN and STOP keys on the operation panel are used to start and stop operation, respectively. The switching
between forward run and reverse run can be done from one of the three control units: operation panel, terminal
board and external control unit.
Jog run
Jog mode, if selected, allows jog operation from the operation panel or the terminal board.
Preset speed operation
Base fre 15-speed operation possible by changing the combination of 4 contacts on the terminal board.
Retry operation
Capable of restarting automatically after a check of the main circuit elements in case the protective function is acti-
vated. 10 times (Max.) (selectable with a parameter)
Various prohibition set-
tings
Possible to write-protect parameters and to prohibit the change of panel frequency settings and the use of operation
panel for operation, emergency stop or resetting.
Regenerative power ride-
through control
Possible to keep the motor running using its regenerative energy in case of a momentary power failure (default:
OFF).
Auto-restart operation
In the event of a momentary power failure, the inverter reads the rotational speed of the coasting motor and outputs
a frequency appropriate to the rotational speed in order to restart the motor smoothly. This function can also be
used when switching to commercial power.
Drooping function
When two or more inverters are used to operate a single load, this function prevents load from concentrating on one
inverter due to unbalance.
Override function
The sum of two analog signals (VIA/VIB) can be used as a frequency command value.
O
per
at
ion s
pec
if
ic
a
ti
ons
Failure detection signal
1c-contact output: (250Vac-0.5A-
cos
ij
=0.4)
<Continued overleaf>