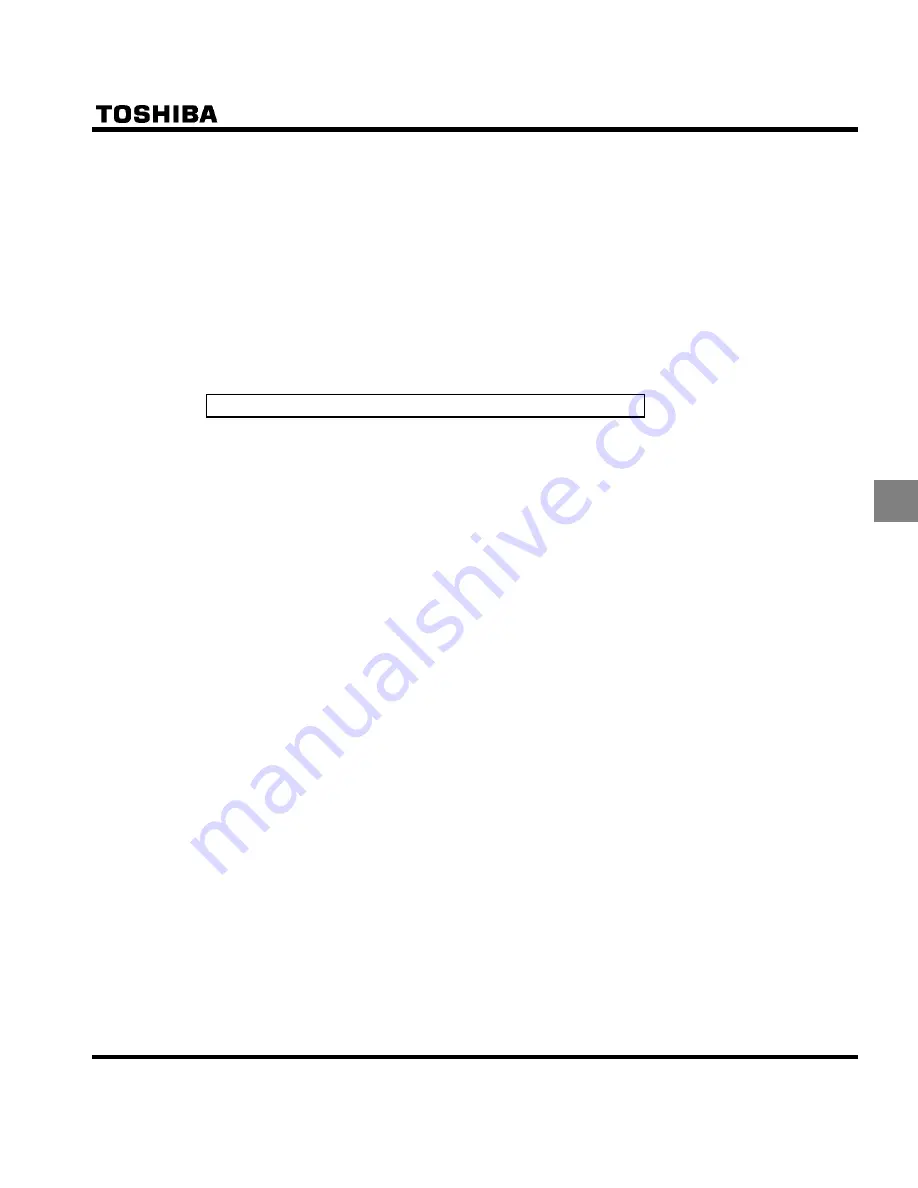
E6581158
E-21
5
+
Motor constant must be set
If the motor you are using is a 4P Toshiba standard motor and if it has the same capacity as the inverter,
there is no need to set the motor constant. In any other case, be sure to set the parameters
H
to
H
properly.
Be sure to set
H
(rated current of motor) and
H
(rated speed of motor) correctly, as specified on
the motor’s nameplate. For the setting of
H
(no-load current of motor), refer to the motor test report.
For other types of motors, there are two ways to set a motor constant.
1) The motor constant can be set automatically (auto-tuning). Set the extended parameter
H
to
.
⇒
For details, see selection 2 in 6.17.
2) Each motor constant can be set individually
⇒
For details, see selection 3 in 6.17.
7) Operating a permanent magnet motor
Setting of V/F control mode selection
RV
to
(PM motor control)
Permanent magnet motors (PM motors) that are light, small in size and highly efficient, as compared to in-
duction motors, can be operated in sensor-less operation mode.
Note that this feature can be used only for specific motors. For more information, contact your Toshiba dealer.
8) Precautions on vector control
1) When exercising vector control, be sure to set the extended parameters
H
to
H
properly. Be
sure to set
H
(rated current of motor) and
H
(rated speed of motor) correctly, as specified on
the motor’s nameplate. For the setting of
H
(no-load current of motor), refer to the motor test report.
2) The sensorless vector control exerts its characteristics effectively in frequency areas below the base fre-
quency (
XN
). The same characteristics will not be obtained in areas above the base frequency.
3) Set the base frequency to anywhere from 40 to 120Hz during vector control (
RV
=
).
4) Use a general purpose squirrel-cage motor with a capacity that is the same as the inverter's rated capacity or
one rank below.
The minimum applicable motor capacity is 0.1kW.
5) Use a motor that has 2-8 P.
6) Always operate the motor in single operation (one inverter to one motor). Sensorless vector control can-
not be used when one inverter is operated with more than one motor.
7) The maximum length of wires between the inverter and motor is 30 meters. If the wires are longer than 30
meters, set standard auto-tuning with the wires connected to improve low-speed torque during sensorless
vector control.
However the effects of voltage drop cause motor-generated torque in the vicinity of rated frequency to be
somewhat lower.
8) Connecting a reactor or surge voltage suppression filter between the inverter and the motor may reduce
motor-generated torque. Setting auto-tuning may also cause a trip (
GVP
) rendering sensorless vector
control unusable.