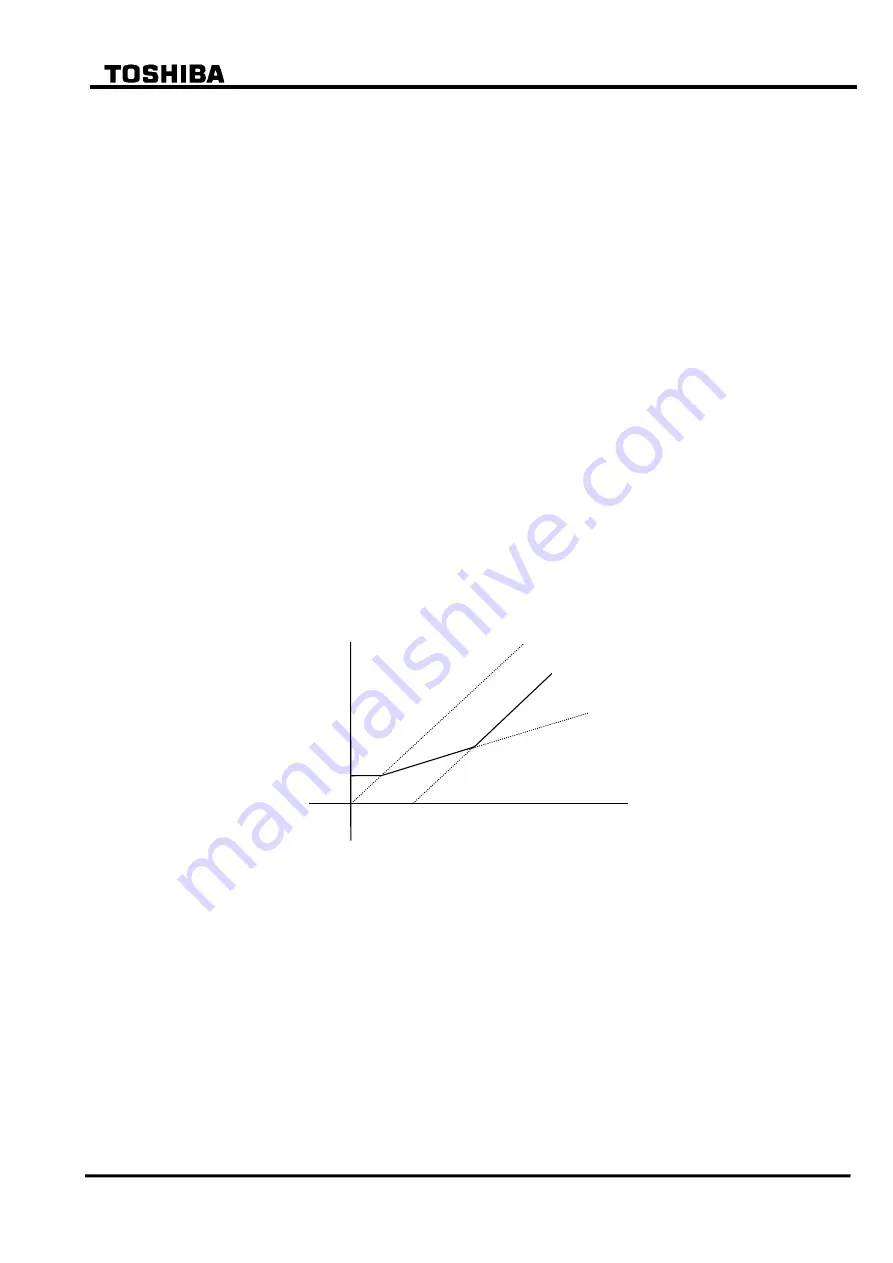
39
6
F
2
S
0
7
8
9
CT saturation during through faults.
2.11.2 High-set Overcurrent Element HOC
High-set overcurrent element HOC is an instantaneous overcurrent characteristic, and is applied
in the differential circuit. The characteristic is expressed by the following equation:
Id
kh
Id is defined as follows for three-winding transformer.
I
d
= |kct1
I
1
+ kct2
I
2
+ kct3
I
3
|
where,
kct1, kct2, kct3: CT ratio matching settings of primary, secondary and tertiary winding
HOC is an un-restrained current differential element which can protect a transformer against
damage due to a heavy internal fault, because it has a simple operation principle and high-speed
operation. Note that HOC is not immune to transformer inrush currents and therefore cnnot be
applied with a sensitive setting.
2.11.3 Restricted Earth Fault Element REF
The restricted earth fault element REF has dual percentage restraining characteristics. Figure
2.11.2 shows the characteristics on the differential current (Id) and restraining current (Ir) plane.
Id is a differential current between the residual current of each winding and the neutral current
and Ir is a restraining current which is the larger of the residual current and the neutral current.
I
d
I
d =
I
r (one-end infeed)
DF2
DF1
kct
ik
kp
I
r
Figure 2.11.2 Restricted Earth Fault Element
Characteristic DF1 is expressed by the following equation:
I
d
p1
I
r
+ (1-p1)
ik
kct
where,
p1: slope of DF1 (fixed to 10%)
ik: minimum operating current
kct: CT ratio matching of line CT to neutral CT (when plural line CTs are applied, maximum
kct is employed.)
For the 1REF element, I
d
and I
r
are calculated by the following equations when applied to a
circuit with one neutral CT and three line CTs. (For the REF element application, see Appendix
Summary of Contents for GRT100 Series
Page 142: ... 141 6 F 2 S 0 7 8 9 Appendix A Block Diagram ...
Page 144: ... 143 6 F 2 S 0 7 8 9 Appendix B Signal List ...
Page 159: ... 158 6 F 2 S 0 7 8 9 ...
Page 160: ... 159 6 F 2 S 0 7 8 9 Appendix C Variable Timer List ...
Page 162: ... 161 6 F 2 S 0 7 8 9 Appendix D Binary Output Default Setting List ...
Page 165: ... 164 6 F 2 S 0 7 8 9 ...
Page 166: ... 165 6 F 2 S 0 7 8 9 Appendix E Details of Relay Menu and LCD and Button Operation ...
Page 174: ... 173 6 F 2 S 0 7 8 9 Appendix F Case Outline Flush Mount Type Rack Mount Type ...
Page 179: ... 178 6 F 2 S 0 7 8 9 ...
Page 180: ... 179 6 F 2 S 0 7 8 9 Appendix G External Connections ...
Page 185: ... 184 6 F 2 S 0 7 8 9 ...
Page 200: ... 199 6 F 2 S 0 7 8 9 ...
Page 201: ... 200 6 F 2 S 0 7 8 9 Appendix J Return Repair Form ...
Page 205: ... 204 6 F 2 S 0 7 8 9 Customer Name Company Name Address Telephone No Facsimile No Signature ...
Page 206: ... 205 6 F 2 S 0 7 8 9 ...
Page 207: ... 206 6 F 2 S 0 7 8 9 Appendix K Technical Data ...
Page 220: ... 219 6 F 2 S 0 7 8 9 ...
Page 221: ... 220 6 F 2 S 0 7 8 9 Appendix M Symbols Used in Scheme Logic ...
Page 224: ... 223 6 F 2 S 0 7 8 9 ...
Page 225: ... 224 6 F 2 S 0 7 8 9 Appendix N Implementation of Thermal Model to IEC60255 8 ...
Page 228: ... 227 6 F 2 S 0 7 8 9 ...
Page 229: ... 228 6 F 2 S 0 7 8 9 Appendix O IEC60870 5 103 Interoperability and Troubleshooting ...
Page 241: ... 240 6 F 2 S 0 7 8 9 Appendix P Modbus Interoperability ...
Page 255: ... 254 6 F 2 S 0 7 8 9 ...
Page 256: ... 255 6 F 2 S 0 7 8 9 Appendix Q Inverse Time Characteristics ...
Page 259: ... 258 6 F 2 S 0 7 8 9 ...
Page 260: ... 259 6 F 2 S 0 7 8 9 Appendix R Failed Module Tracing and Replacement ...
Page 266: ... 265 6 F 2 S 0 7 8 9 Appendix S Ordering ...
Page 269: ... 268 6 F 2 S 0 7 8 9 3 1 Oct 2 2017 Republished under spin off company ...
Page 270: ......