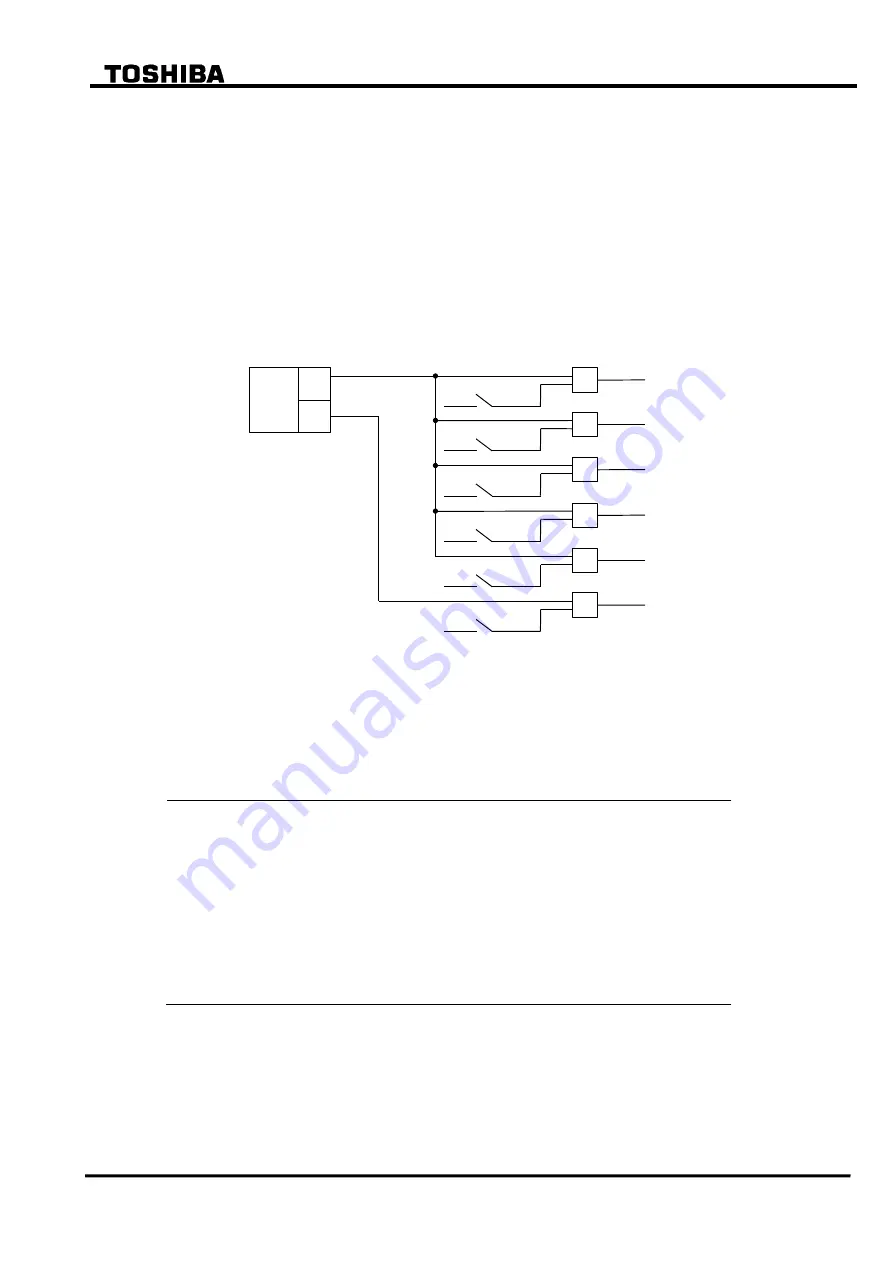
31
6
F
2
S
0
7
8
9
2.6 Thermal Overload Protection
The thermal overload protection is applied to protect transformers from electrical thermal
damage. A-phase current is used to detect the thermal overload of a transformer. The
characteristics are exponential functions according to IEC 60255-8 standards and take into
account the
I
2
R
losses due to the particular operational current and the simultaneous cooling due
to the coolant. In this way the tripping time during an overload condition takes the pre-load into
consideration. An alarm stage can be set to operate before reaching the tripping condition.
Figure 2.6.1 shows the scheme logic of thermal overcurrent protection. THR tripping output can
be given to up to five breakers. Any of the five breaker tripping signals THR-1 to THR-5 can be
blocked by the scheme switch [THR1] to [THR5] settings. Alarming signal THR-A can be
blocked by the scheme switch [THRA] setting.
THR
A
S
THR-1
&
[THR1]
THR-2
&
[THR2]
THR-3
&
[THR3]
THR-4
&
[THR4]
THR-5
&
[THR5]
THR-A
&
[THRA]
“ON”
“ON”
“ON”
“ON”
“ON”
“ON”
Figure 2.6.1 Scheme Logic of Thermal Overload Protection
Setting
The following shows the setting elements for the thermal overload protection and their setting
ranges.
Element
Range
Step
Default
Remarks
0.5
500.0min
0.1min
60.0min
Thermal time constant
k
0.10
4.00
0.01
1.30
Constant
IB
0.50
2.50(*1)
0.01
1.00
Basic current
Ip
0.00
1.00(*1)
0.01
0.00
Pre-specified load current
TA
0
10min
1min
10min
Time for alarm (before trip) (*3)
Scheme switch
THR1 to THR5
THRA
Off/On
Off/On
(*2)
On
Enable or disable
Trip
Alarm
(
1): Multiplier of CT secondary rated current
(*2): Default settings are dependent on the models. See Appendix H.
(*3):
Alarming time = THR trip time (operating time)
TA (setting time)
Note: Ip sets a minimum level of previous load current to be used by the thermal element, and is
typically used when testing the element. For the majority of applications, Ip should be set to
zero, in which case the previous load current, Ip, is calculated internally by the thermal
model, providing memory of conditions occurring before an overload.
Summary of Contents for GRT100 Series
Page 142: ... 141 6 F 2 S 0 7 8 9 Appendix A Block Diagram ...
Page 144: ... 143 6 F 2 S 0 7 8 9 Appendix B Signal List ...
Page 159: ... 158 6 F 2 S 0 7 8 9 ...
Page 160: ... 159 6 F 2 S 0 7 8 9 Appendix C Variable Timer List ...
Page 162: ... 161 6 F 2 S 0 7 8 9 Appendix D Binary Output Default Setting List ...
Page 165: ... 164 6 F 2 S 0 7 8 9 ...
Page 166: ... 165 6 F 2 S 0 7 8 9 Appendix E Details of Relay Menu and LCD and Button Operation ...
Page 174: ... 173 6 F 2 S 0 7 8 9 Appendix F Case Outline Flush Mount Type Rack Mount Type ...
Page 179: ... 178 6 F 2 S 0 7 8 9 ...
Page 180: ... 179 6 F 2 S 0 7 8 9 Appendix G External Connections ...
Page 185: ... 184 6 F 2 S 0 7 8 9 ...
Page 200: ... 199 6 F 2 S 0 7 8 9 ...
Page 201: ... 200 6 F 2 S 0 7 8 9 Appendix J Return Repair Form ...
Page 205: ... 204 6 F 2 S 0 7 8 9 Customer Name Company Name Address Telephone No Facsimile No Signature ...
Page 206: ... 205 6 F 2 S 0 7 8 9 ...
Page 207: ... 206 6 F 2 S 0 7 8 9 Appendix K Technical Data ...
Page 220: ... 219 6 F 2 S 0 7 8 9 ...
Page 221: ... 220 6 F 2 S 0 7 8 9 Appendix M Symbols Used in Scheme Logic ...
Page 224: ... 223 6 F 2 S 0 7 8 9 ...
Page 225: ... 224 6 F 2 S 0 7 8 9 Appendix N Implementation of Thermal Model to IEC60255 8 ...
Page 228: ... 227 6 F 2 S 0 7 8 9 ...
Page 229: ... 228 6 F 2 S 0 7 8 9 Appendix O IEC60870 5 103 Interoperability and Troubleshooting ...
Page 241: ... 240 6 F 2 S 0 7 8 9 Appendix P Modbus Interoperability ...
Page 255: ... 254 6 F 2 S 0 7 8 9 ...
Page 256: ... 255 6 F 2 S 0 7 8 9 Appendix Q Inverse Time Characteristics ...
Page 259: ... 258 6 F 2 S 0 7 8 9 ...
Page 260: ... 259 6 F 2 S 0 7 8 9 Appendix R Failed Module Tracing and Replacement ...
Page 266: ... 265 6 F 2 S 0 7 8 9 Appendix S Ordering ...
Page 269: ... 268 6 F 2 S 0 7 8 9 3 1 Oct 2 2017 Republished under spin off company ...
Page 270: ......