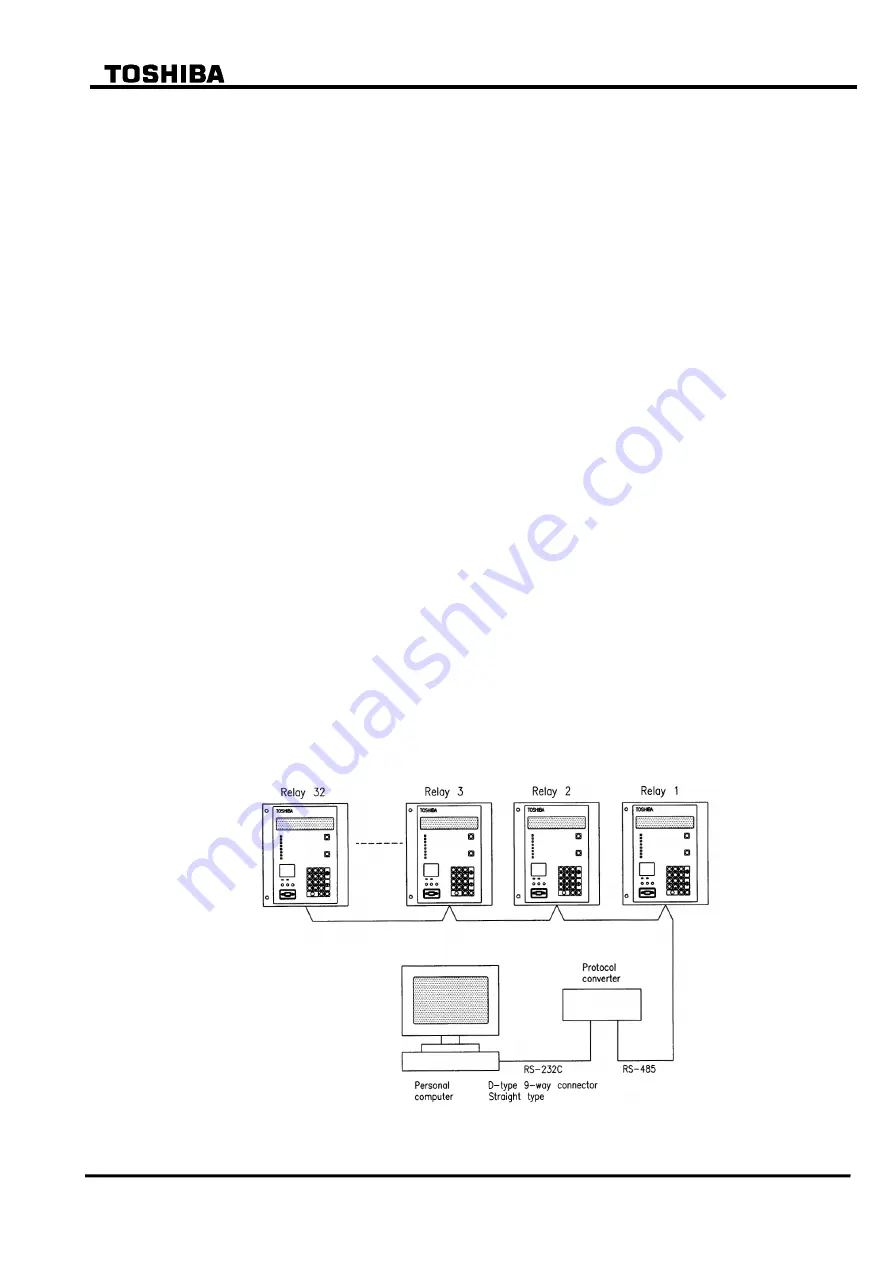
102
6
F
2
S
0
7
8
9
4.3 Personal Computer Interface
The relay can be operated from a personal computer using an RS-232C port on the front panel.
On the personal computer, the following analysis and display of the fault voltage and current are
available in addition to the items available on the LCD screen.
Display of voltage and current waveform:
Oscillograph, vector display
Symmetrical component analysis:
On arbitrary time span
Harmonic analysis:
On arbitrary time span
Frequency analysis:
On arbitrary time span
For the details, see the separate instruction manual "PC INTERFACE RSM100".
4.4 Relay Setting and Monitoring System
The Relay Setting and Monitoring (RSM) system is a system that retrieves and analyses the data
on power system quantities, fault and event records and views or changes settings in individual
relays via a telecommunication network using a remote PC.
For the details, see the separate instruction manual "PC INTERFACE RSM100".
Figure 4.4.1 shows the typical configuration of the RSM system via a protocol converter G1PR2.
The relays are connected through twisted pair cables, and the maximum 256 relays can be
connected since the G1PR2 can provide up to 8 ports. The total length of twisted pair wires
should not exceed 1200 m. Relays are mutually connected using an RS485 port on the relay rear
panel and connected to a PC RS232C port via G1PR2. Terminal resistor (150 ohms) is connected
the last relay. The transmission rate used is 64 kbits/s.
Figure 4.4.2 shows the configuration of the RSM system with Ethernet LAN (option). The relays
are connected to HUB through UTP cable using RJ-45 connector at the rear of the relay. The
relay recognizes the transmission speed automatically.
In case of the optional fiber optic interface (option), the relays are connected through
graded-index multi-mode 50/125
m or 62.5/125
m type optical fiber using ST connector at the
rear of the relay.
G1PR2
Figure 4.4.1 Relay Setting and Monitoring System (1)
Twisted paired
cable
Summary of Contents for GRT100 Series
Page 142: ... 141 6 F 2 S 0 7 8 9 Appendix A Block Diagram ...
Page 144: ... 143 6 F 2 S 0 7 8 9 Appendix B Signal List ...
Page 159: ... 158 6 F 2 S 0 7 8 9 ...
Page 160: ... 159 6 F 2 S 0 7 8 9 Appendix C Variable Timer List ...
Page 162: ... 161 6 F 2 S 0 7 8 9 Appendix D Binary Output Default Setting List ...
Page 165: ... 164 6 F 2 S 0 7 8 9 ...
Page 166: ... 165 6 F 2 S 0 7 8 9 Appendix E Details of Relay Menu and LCD and Button Operation ...
Page 174: ... 173 6 F 2 S 0 7 8 9 Appendix F Case Outline Flush Mount Type Rack Mount Type ...
Page 179: ... 178 6 F 2 S 0 7 8 9 ...
Page 180: ... 179 6 F 2 S 0 7 8 9 Appendix G External Connections ...
Page 185: ... 184 6 F 2 S 0 7 8 9 ...
Page 200: ... 199 6 F 2 S 0 7 8 9 ...
Page 201: ... 200 6 F 2 S 0 7 8 9 Appendix J Return Repair Form ...
Page 205: ... 204 6 F 2 S 0 7 8 9 Customer Name Company Name Address Telephone No Facsimile No Signature ...
Page 206: ... 205 6 F 2 S 0 7 8 9 ...
Page 207: ... 206 6 F 2 S 0 7 8 9 Appendix K Technical Data ...
Page 220: ... 219 6 F 2 S 0 7 8 9 ...
Page 221: ... 220 6 F 2 S 0 7 8 9 Appendix M Symbols Used in Scheme Logic ...
Page 224: ... 223 6 F 2 S 0 7 8 9 ...
Page 225: ... 224 6 F 2 S 0 7 8 9 Appendix N Implementation of Thermal Model to IEC60255 8 ...
Page 228: ... 227 6 F 2 S 0 7 8 9 ...
Page 229: ... 228 6 F 2 S 0 7 8 9 Appendix O IEC60870 5 103 Interoperability and Troubleshooting ...
Page 241: ... 240 6 F 2 S 0 7 8 9 Appendix P Modbus Interoperability ...
Page 255: ... 254 6 F 2 S 0 7 8 9 ...
Page 256: ... 255 6 F 2 S 0 7 8 9 Appendix Q Inverse Time Characteristics ...
Page 259: ... 258 6 F 2 S 0 7 8 9 ...
Page 260: ... 259 6 F 2 S 0 7 8 9 Appendix R Failed Module Tracing and Replacement ...
Page 266: ... 265 6 F 2 S 0 7 8 9 Appendix S Ordering ...
Page 269: ... 268 6 F 2 S 0 7 8 9 3 1 Oct 2 2017 Republished under spin off company ...
Page 270: ......