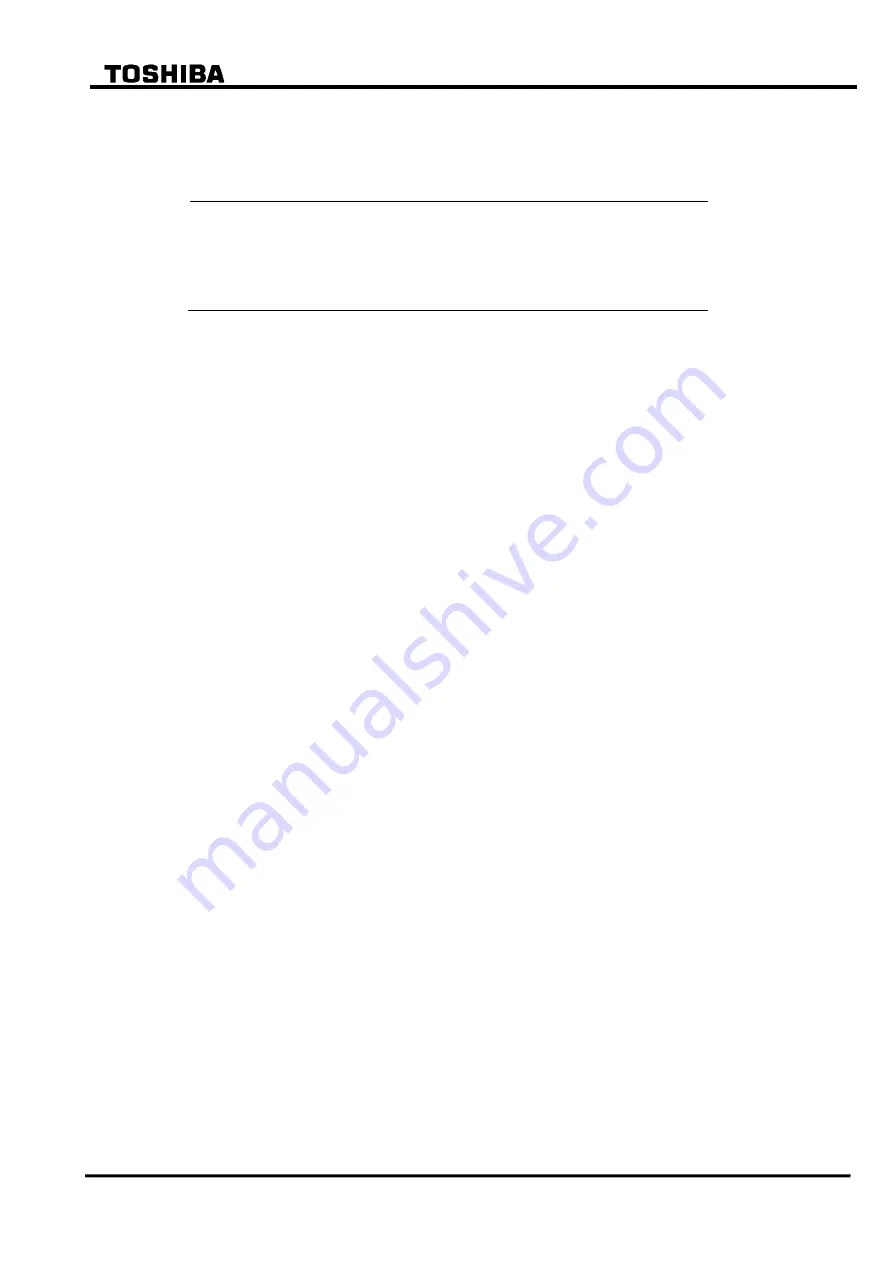
63
6
F
2
S
0
7
8
9
Setting
The recording mode can be set for each event. One of the following four modes is selectable.
Modes
Setting
Not to record the event.
None
To record the event when the status changes to "operate".
Operate
To record the event when the status changes to "reset".
Reset
To record the event when the status changes both to "operate" and "reset".
Both
For the setting, see the Section 4.2.6.5. The default setting is "Both" for all events except those
marked with (*) in Table 3.4.1. The events marked with (*) have a default setting of "Operate".
3.4.3 Disturbance Recording
Disturbance Recording is started when overcurrent starter elements operate or a tripping
command is output, or PLC command by user-setting (max. 4: Signal No. 2632 to 2635) is
output. The records include 13 analog signals (primary: Ia1, Ib1, Ic1, In1, secondary: Ia2, Ib2,
Ic2, In2, tertiary: Ia3, Ib3, Ic3, In3, voltage: V). Following binary signals listed below and the
dates and times at which recording started are also recorded.
-Trip-1
-5F
-2OCI
-FRQ
-Trip-2
-1REF
-3OCI
-V/F
-Trip-3
-2REF
-1EF
-THR
-Trip-4
-3REF
-2EF
-Mec. Trip
-Trip-5
-1OC
-3EF
-DIFT
-2OC
-1EFI
-HOC
-3OC
-2EFI
-2F
-1OCI
-3EFI
The LCD display only shows the dates and times of disturbance records stored. Details can be
displayed on the PC. For how to obtain disturbance records on the PC, see the PC software
instruction manual.
The pre-fault recording time is fixed at 0.3s and post-fault recording time can be set between 0.1
and 3.0s.
The number of records stored depends on the post-fault recording time. The approximate
relationship between the post-fault recording time and the number of records stored is shown in
Table 3.4.2.
Note:
If the recording time setting is changed, all previously recorded data is deleted.
Summary of Contents for GRT100 Series
Page 142: ... 141 6 F 2 S 0 7 8 9 Appendix A Block Diagram ...
Page 144: ... 143 6 F 2 S 0 7 8 9 Appendix B Signal List ...
Page 159: ... 158 6 F 2 S 0 7 8 9 ...
Page 160: ... 159 6 F 2 S 0 7 8 9 Appendix C Variable Timer List ...
Page 162: ... 161 6 F 2 S 0 7 8 9 Appendix D Binary Output Default Setting List ...
Page 165: ... 164 6 F 2 S 0 7 8 9 ...
Page 166: ... 165 6 F 2 S 0 7 8 9 Appendix E Details of Relay Menu and LCD and Button Operation ...
Page 174: ... 173 6 F 2 S 0 7 8 9 Appendix F Case Outline Flush Mount Type Rack Mount Type ...
Page 179: ... 178 6 F 2 S 0 7 8 9 ...
Page 180: ... 179 6 F 2 S 0 7 8 9 Appendix G External Connections ...
Page 185: ... 184 6 F 2 S 0 7 8 9 ...
Page 200: ... 199 6 F 2 S 0 7 8 9 ...
Page 201: ... 200 6 F 2 S 0 7 8 9 Appendix J Return Repair Form ...
Page 205: ... 204 6 F 2 S 0 7 8 9 Customer Name Company Name Address Telephone No Facsimile No Signature ...
Page 206: ... 205 6 F 2 S 0 7 8 9 ...
Page 207: ... 206 6 F 2 S 0 7 8 9 Appendix K Technical Data ...
Page 220: ... 219 6 F 2 S 0 7 8 9 ...
Page 221: ... 220 6 F 2 S 0 7 8 9 Appendix M Symbols Used in Scheme Logic ...
Page 224: ... 223 6 F 2 S 0 7 8 9 ...
Page 225: ... 224 6 F 2 S 0 7 8 9 Appendix N Implementation of Thermal Model to IEC60255 8 ...
Page 228: ... 227 6 F 2 S 0 7 8 9 ...
Page 229: ... 228 6 F 2 S 0 7 8 9 Appendix O IEC60870 5 103 Interoperability and Troubleshooting ...
Page 241: ... 240 6 F 2 S 0 7 8 9 Appendix P Modbus Interoperability ...
Page 255: ... 254 6 F 2 S 0 7 8 9 ...
Page 256: ... 255 6 F 2 S 0 7 8 9 Appendix Q Inverse Time Characteristics ...
Page 259: ... 258 6 F 2 S 0 7 8 9 ...
Page 260: ... 259 6 F 2 S 0 7 8 9 Appendix R Failed Module Tracing and Replacement ...
Page 266: ... 265 6 F 2 S 0 7 8 9 Appendix S Ordering ...
Page 269: ... 268 6 F 2 S 0 7 8 9 3 1 Oct 2 2017 Republished under spin off company ...
Page 270: ......