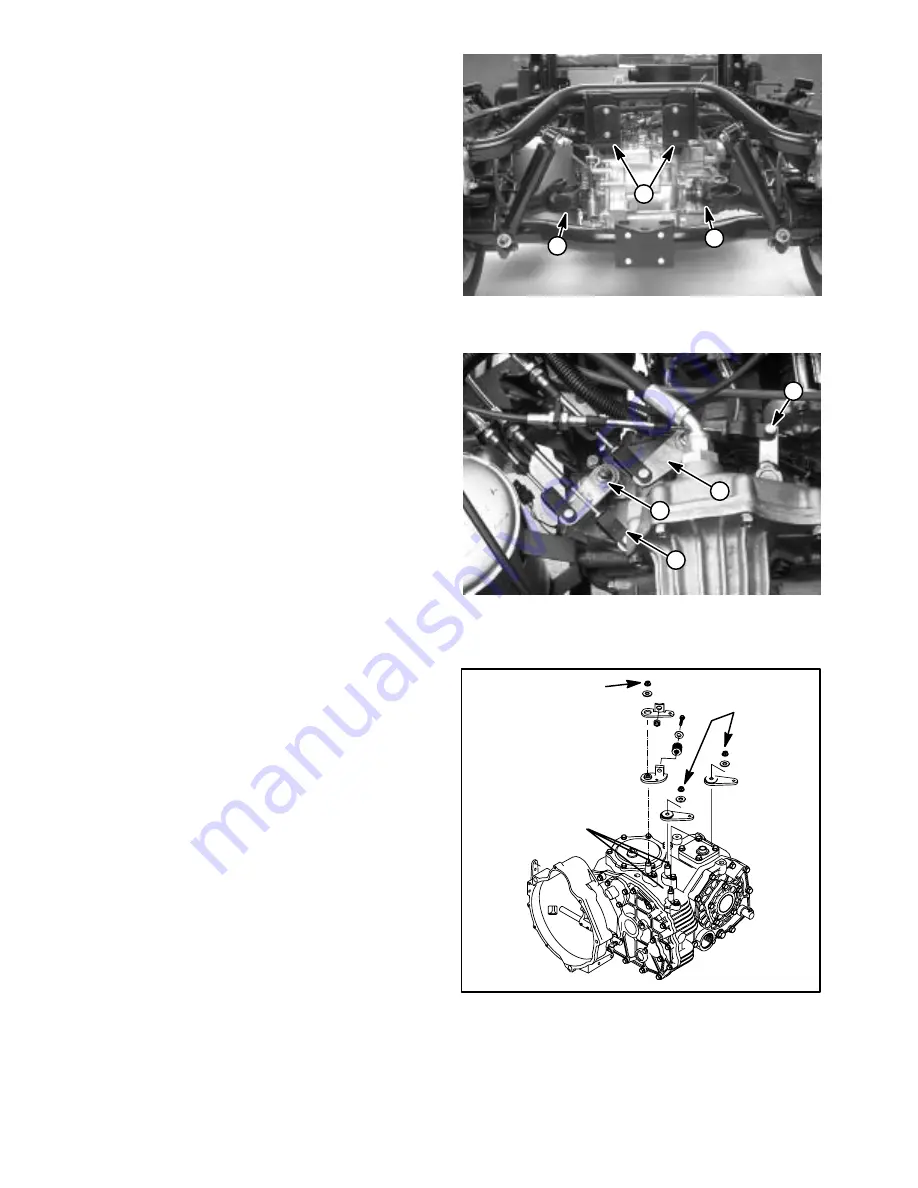
Workman 3000/4000 Series
Page 6 – 18
Drive Train
16.Put blocking under engine for support. Support trans-
axle with a floor jack or suspend transaxle from vehicle
frame rails.
17.Remove transaxle isolation mounts and mount
brackets (Fig. 17).
18.Remove drive shaft clamp bolts, then slide transaxle
side–to–side to disconnect each drive shaft from axle
shafts on transaxle.
19.Remove cap screws securing clutch bell housing to
engine. Note location of washers and harness brackets.
20.Carefully pull transaxle back to disengage transaxle
input shaft from clutch. Use floor jack to lower transaxle
and slide out rear of vehicle under the frame.
21.Note location and retrieve dowel pins from bell hous-
ing.
Installation
1. To install the transaxle, perform Transaxle Removal
procedure in reverse order noting the following:
IMPORTANT: Workman 3100 (air cooled, gasoline
engine) vehicles require application of silicone seal-
ant to mating surface of bell housing and clutch
adapter plate on engine. This will prevent dirt and
debris from getting into bell housing and damaging
clutch or release bearing.
A. When installing driveshafts to transaxle, align
mounting holes in driveshaft with relief in transaxle
shaft. Install cap screws, hardened washers, and
flange nuts to secure driveshaft to transaxle shaft.
Torque fasteners from 35 to 42 ft–lb (47 to 57 N–m).
B. Apply Loctite #242 (or equivalent) to the threads
of cap screws used to secure the control cable sup-
port bracket to the transaxle.
C. Before installing two shift levers and shift arm
onto transaxle shafts, thoroughly clean shafts and
apply Loctite #680 to threads and tapers of shafts.
Secure by torquing nut from 200 to 280 in–lb (22.6 to
31.6 N–m) while holding lever to prevent torque
transfer into transaxle (Fig. 19).
2. Install a new hydraulic oil filter and fill transaxle with
the correct oil (see Operator’s Manual). Check for oil
leaks and repair as necessary.
3. Adjust clutch pedal, shift cables, high–low cable and
differential lock cable (see Operator’s Manual).
4. If equipped with PTO, adjust PTO cable (see PTO
Cable Adjustment in the Adjustments section of this
chapter).
1. Mounting
brackets
2. Drive
shaft
Figure 17
2
1
2
1. First–Reverse
2. High–Low
3. 2nd–3rd
4. PTO
clutch
Figure 18
4
3
2
1
Apply Loctite 680
to threads and tapers
200 to 280 in–lb
200 to 280 in–lb
(22.6 to 31.6 N–m)
(22.6 to 31.6 N–m)
Figure 19
Summary of Contents for Workman 3000 Series
Page 2: ...This page is intentionally blank Workman 3000 4000 Series ...
Page 4: ...This page is intentionally blank Workman 3000 4000 Series ...
Page 6: ...This page is intentionally blank Workman 3000 4000 Series ...
Page 42: ...This page is intentionally blank Briggs Daihatsu Gasoline Engine Page 3 22 Workman 3200 4200 ...
Page 91: ...This page is intentionally blank Workman 3000 4000 Series Page 6 19 Drive Train Drive Train ...
Page 136: ...This page is intentionally blank Drive Train Page 6 64 Workman 3000 4000 Series ...
Page 145: ...This page is intentionally blank Workman 3000 4000 Series Page 7 9 Chassis Chassis ...
Page 149: ...This page is intentionally blank Workman 3000 4000 Series Page 7 13 Chassis Chassis ...
Page 155: ...This page is intentionally blank Workman 3000 4000 Series Page 7 19 Chassis Chassis ...
Page 170: ...This page is intentionally blank Chassis Page 7 34 Workman 3000 4000 Series ...
Page 192: ...This page is intentionally blank Hydraulic System Page 9 2 Workman 3000 4000 Series ...
Page 214: ...This page is intentionally blank Hydraulic System Page 9 24 Workman 3000 4000 Series ...
Page 242: ...This page is intentionally blank Hydraulic System Page 9 48 Workman 3000 4000 Series ...
Page 278: ...This page is intentionally blank Front Wheel Drive 4WD Page 10 36 Workman 4000 Series ...
Page 280: ...Workman 3000 4000 Electrical Schematics Page 11 2 This page is intentionally blank ...
Page 287: ...Rev C Page 11 9 This Page Is Intentionally Blank ...
Page 290: ...Rev C Page 11 12 Front Wire Harness Drawing Workman 3000 4000 Serial Number Above 280000000 ...
Page 306: ......