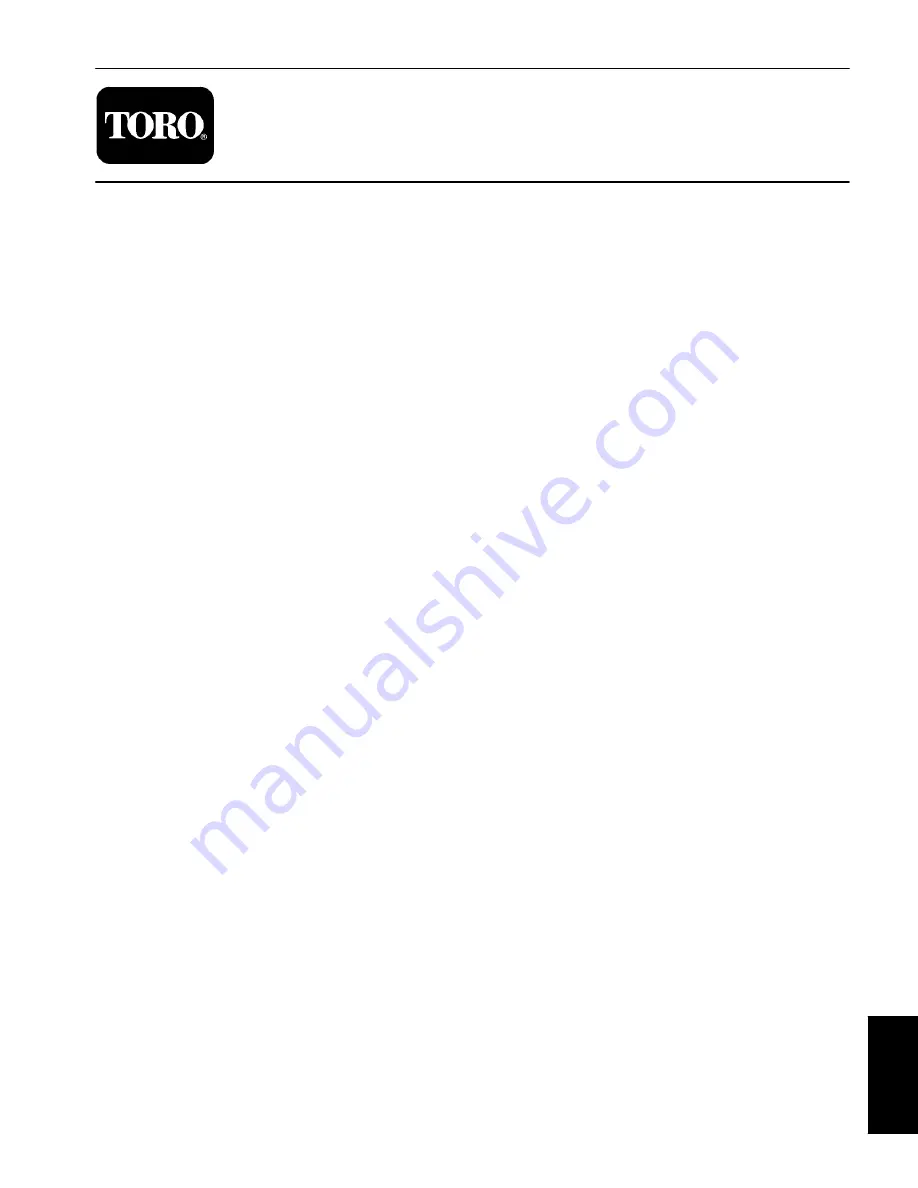
Rev. D
Workman 3000/4000 Series
Page 9 -- 1
Hydraulic System
Chapter 9
Hydraulic System
Table of Contents
SPECIFICATIONS
3
. . . . . . . . . . . . . . . . . . . . . . . . . . . . .
GENERAL INFORMATION
4
. . . . . . . . . . . . . . . . . . . . .
Hydraulic Hoses
4
. . . . . . . . . . . . . . . . . . . . . . . . . . . .
Hydraulic Fitting Installation
4
. . . . . . . . . . . . . . . . . . .
HYDRAULIC SCHEMATICS
6
. . . . . . . . . . . . . . . . . . . .
Vehicle Hydraulic Schematic
6
. . . . . . . . . . . . . . . . . .
High Flow Hydraulic Kit (Optional) Schematic
7
. . .
HYDRAULIC CIRCUIT OPERATION
8
. . . . . . . . . . . . .
Steering Circuit
8
. . . . . . . . . . . . . . . . . . . . . . . . . . . . .
Raise and Lower Bed
9
. . . . . . . . . . . . . . . . . . . . . . . .
SPECIAL TOOLS
10
. . . . . . . . . . . . . . . . . . . . . . . . . . . .
Hydraulic Pressure Test Kit
10
. . . . . . . . . . . . . . . . . .
Hydraulic Tester (Pressure and Flow)
10
. . . . . . . . .
Hydraulic Test Fitting Kit
11
. . . . . . . . . . . . . . . . . . . . .
Male Coupler (For Optional High Flow
Hydraulic Kit)
11
. . . . . . . . . . . . . . . . . . . . . . . . . . . .
TROUBLESHOOTING
12
. . . . . . . . . . . . . . . . . . . . . . . .
TESTING
15
. . . . . . . . . . . . . . . . . . . . . . . . . . . . . . . . . . .
Test No. 1: Gear Pump Flow and System Relief
Pressure
16
. . . . . . . . . . . . . . . . . . . . . . . . . . . . . . . .
Test No. 2: Steering Control Valve and Steering
Cylinder
18
. . . . . . . . . . . . . . . . . . . . . . . . . . . . . . . . .
Test No. 3: Lift Cylinder Internal Leakage
20
. . . . . .
Test No. 4: High Flow Hydraulic Kit (Optional)
Gear Pump Flow and Relief Pressure
22
. . . . . . .
SERVICE and REPAIRS
25
. . . . . . . . . . . . . . . . . . . . . .
General Precautions for Removing and Installing
Hydraulic System Components
25
. . . . . . . . . . . . .
Check Hydraulic Lines and Hoses
25
. . . . . . . . . . . .
Gear Pump (Vehicles With Liquid Cooled
Engine)
26
. . . . . . . . . . . . . . . . . . . . . . . . . . . . . . . . .
Gear Pump (Vehicles With Air Cooled Engine)
27
.
Gear Pump Service Barnes Gear Pump)
28
. . . . . .
Gear Pump Service (Casappa Gear Pump)
29.1
. .
Lift Valve
30
. . . . . . . . . . . . . . . . . . . . . . . . . . . . . . . . . .
Lift Valve Service
32
. . . . . . . . . . . . . . . . . . . . . . . . . . .
Steering Control Valve
34
. . . . . . . . . . . . . . . . . . . . . .
Steering Control Valve Service
36
. . . . . . . . . . . . . . .
Steering Cylinder
38
. . . . . . . . . . . . . . . . . . . . . . . . . . .
Steering Cylinder Service
40
. . . . . . . . . . . . . . . . . . .
Lift Cylinder
42
. . . . . . . . . . . . . . . . . . . . . . . . . . . . . . .
Lift Cylinder Service
44
. . . . . . . . . . . . . . . . . . . . . . . .
Hydraulic Manifold (Optional High Flow
Hydraulic Kit)
46
. . . . . . . . . . . . . . . . . . . . . . . . . . . .
SAUER/DANFOSS STEERING UNIT TYPE OSPM
SERVICE MANUAL
Hydraulic System
Summary of Contents for Workman 3000 Series
Page 2: ...This page is intentionally blank Workman 3000 4000 Series ...
Page 4: ...This page is intentionally blank Workman 3000 4000 Series ...
Page 6: ...This page is intentionally blank Workman 3000 4000 Series ...
Page 42: ...This page is intentionally blank Briggs Daihatsu Gasoline Engine Page 3 22 Workman 3200 4200 ...
Page 91: ...This page is intentionally blank Workman 3000 4000 Series Page 6 19 Drive Train Drive Train ...
Page 136: ...This page is intentionally blank Drive Train Page 6 64 Workman 3000 4000 Series ...
Page 145: ...This page is intentionally blank Workman 3000 4000 Series Page 7 9 Chassis Chassis ...
Page 149: ...This page is intentionally blank Workman 3000 4000 Series Page 7 13 Chassis Chassis ...
Page 155: ...This page is intentionally blank Workman 3000 4000 Series Page 7 19 Chassis Chassis ...
Page 170: ...This page is intentionally blank Chassis Page 7 34 Workman 3000 4000 Series ...
Page 192: ...This page is intentionally blank Hydraulic System Page 9 2 Workman 3000 4000 Series ...
Page 214: ...This page is intentionally blank Hydraulic System Page 9 24 Workman 3000 4000 Series ...
Page 242: ...This page is intentionally blank Hydraulic System Page 9 48 Workman 3000 4000 Series ...
Page 278: ...This page is intentionally blank Front Wheel Drive 4WD Page 10 36 Workman 4000 Series ...
Page 280: ...Workman 3000 4000 Electrical Schematics Page 11 2 This page is intentionally blank ...
Page 287: ...Rev C Page 11 9 This Page Is Intentionally Blank ...
Page 290: ...Rev C Page 11 12 Front Wire Harness Drawing Workman 3000 4000 Serial Number Above 280000000 ...
Page 306: ......