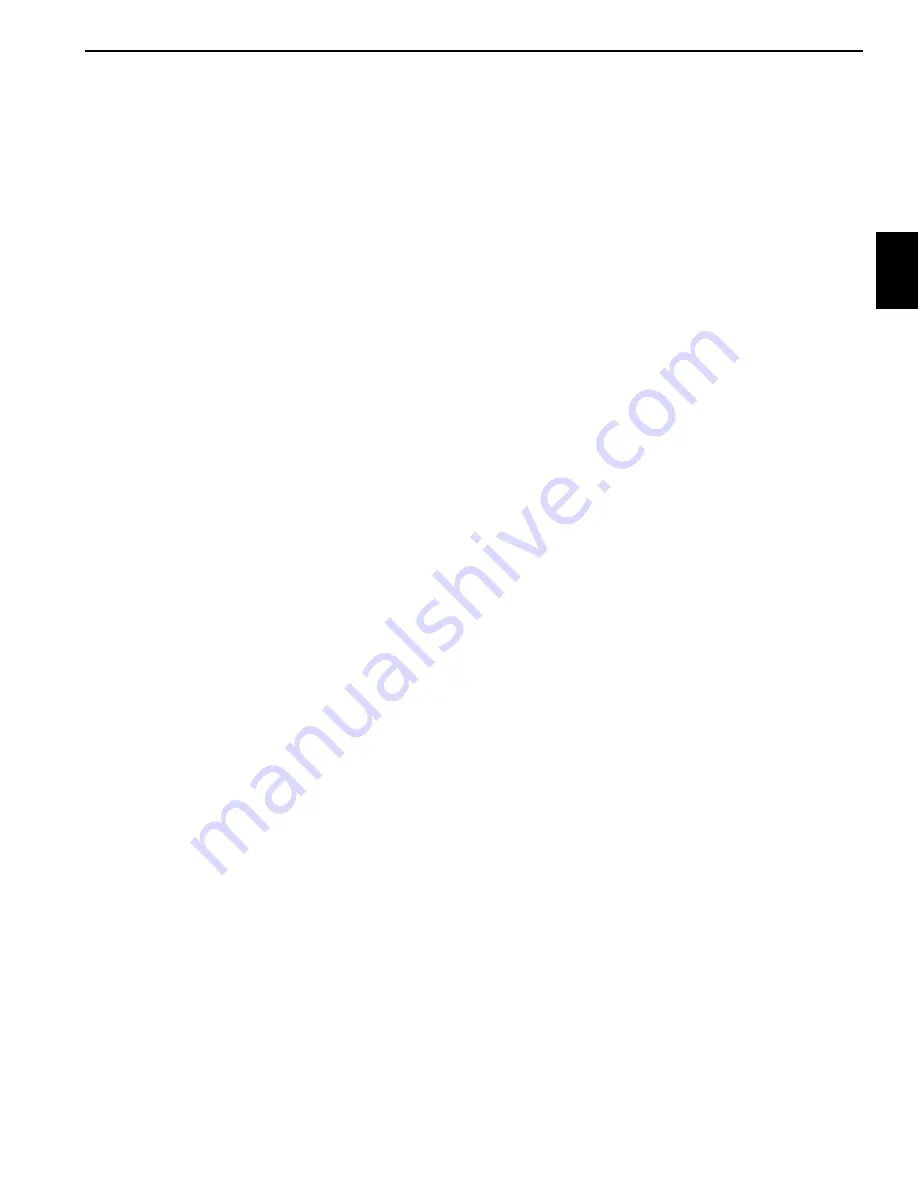
Table of Contents 1- i
1
Section 1
CONTENTS
Engine
Precautions .................................................1-1
Precautions............................................................. 1-1
Precautions for Engine.......................................... 1-1
Engine General Information and
Diagnosis ................................................. 1A-1
Precautions...........................................................1A-1
Precautions on Engine Service ........................... 1A-1
Precautions in Diagnosing Trouble ..................... 1A-1
Precautions For DTC Troubleshooting................ 1A-2
Precautions of ECM Circuit Inspection................ 1A-2
Precautions of Electric Throttle Body
System Calibration............................................ 1A-2
General Description .............................................1A-2
Statement on Cleanliness and Care ................... 1A-2
Engine Diagnosis General Description ............... 1A-3
On-Board Diagnostic System Description........... 1A-3
Engine and Emission Control System
Description ........................................................ 1A-6
CAN Communication System Description........... 1A-6
Air Intake System Description............................. 1A-9
Description of Electric Throttle Body System .... 1A-10
Description of Electric Throttle Body
System Calibration..........................................1A-11
Generator Control System Description .............1A-11
A/F Sensor Description ..................................... 1A-12
Electronic Control System Description.............. 1A-13
Engine and Emission Control Input / Output
Table ............................................................... 1A-21
Schematic and Routing Diagram......................1A-22
Engine and Emission Control System
Diagram ..........................................................1A-22
Component Location .........................................1A-23
Electronic Control System Components
Location ..........................................................1A-23
Diagnostic Information and Procedures..........1A-25
Engine and Emission Control System
Check.............................................................. 1A-25
Malfunction Indicator Lamp (MIL) Check .......... 1A-28
DTC Check .......................................................1A-28
DTC Clearance ................................................. 1A-29
DTC Table.........................................................1A-30
Fail-Safe Table.................................................. 1A-36
Scan Tool Data ................................................. 1A-37
Visual Inspection...............................................1A-43
Engine Basic Inspection.................................... 1A-44
Engine Symptom Diagnosis.............................. 1A-48
Malfunction Indicator Lamp Does Not Come
ON with Ignition Switch ON and Engine
Stop (but Engine Can Be Started)...................1A-57
Malfunction Indicator Lamp Remains ON
after Engine Starts ..........................................1A-59
DTC P0010: Camshaft Position Actuator
Circuit (For M16 Engine) .................................1A-60
DTC P0011 / P0012: Camshaft Position -
Timing Over-Advanced or System Performance
/ -Retarded (For M16 Engine) .........................1A-62
DTC P0030: HO2S Heater Control Circuit
(Sensor-1) .......................................................1A-64
DTC P0031 / P0032: HO2S Heater Control
Circuit Low / High (Sensor-1) ..........................1A-65
DTC P0037 / P0038: HO2S Heater Control
Circuit Low / High (Sensor-2) ..........................1A-69
DTC P0101: Mass Air Flow Circuit Range
/ Performance..................................................1A-72
DTC P0102: Mass Air Flow Circuit Low
Input ................................................................1A-75
DTC P0103: Mass Air Flow Circuit High
Input ................................................................1A-77
DTC P0106: Manifold Absolute Pressure
Range / Performance ......................................1A-79
DTC P0107: Manifold Absolute Pressure
Circuit Low Input .............................................1A-80
DTC P0108: Manifold Absolute Pressure
Circuit High Input.............................................1A-82
DTC P0111: Intake Air Temperature Circuit
Range / Performance ......................................1A-84
DTC P0112: Intake Air Temperature
Sensor Circuit Low ..........................................1A-87
DTC P0113: Intake Air Temperature
Sensor Circuit High .........................................1A-89
DTC P0116: Engine Coolant Temperature
Circuit Range / Performance...........................1A-91
DTC P0117: Engine Coolant Temperature
Circuit Low ......................................................1A-94
DTC P0118: Engine Coolant Temperature
Circuit High......................................................1A-95
DTC P0122: Throttle Position Sensor
(Main) Circuit Low ...........................................1A-98
DTC P0123: Throttle Position Sensor
(Main) Circuit High ........................................1A-101
DTC P0131 / P0132 / P0134: O2 Sensor
(HO2S) Circuit Low Voltage / High Voltage
/ No Activity Detected (Sensor-1)..................1A-104
DTC P0133: O2 Sensor (HO2S) Circuit
Slow Response (Sensor-1) ...........................1A-105
www.CarGarage.ir
www.CarGarage.ir
www.CarGarage.ir