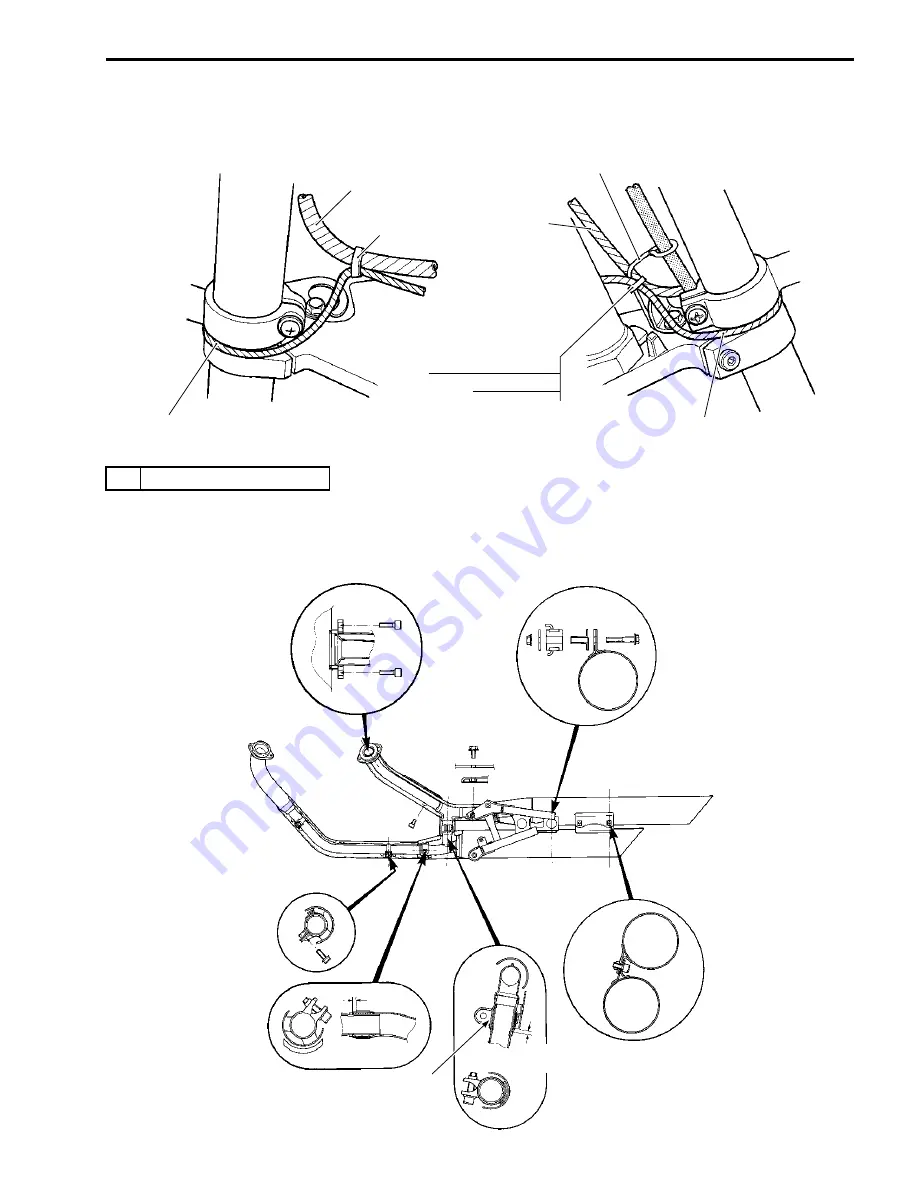
SERVICING INFORMATION 10-23
FRONT TURN SIGNAL LEAD WIRE ROUTING
MUFFLER & EXHAUST PIPE INSTALLATION
*1 Cut after clamping.
Clamp
*1
Left handle switch harness
Brake hose guide
Right front turn signal
Clamp
Right front turn signal
Speed sensor
Wiring harness
Left front turn signal
Apply PERMATEX 1372.
5 mm
(0.12 in)
5 mm
(0.12 in)
SA
MP
LE
Summary of Contents for Boulevard M50
Page 1: ...VZ800 9 9 5 0 0 3 8 0 5 0 0 1 E...
Page 42: ...2 26 PERIODIC MAINTENANCE SAMPLE...
Page 413: ...SERVICING INFORMATION 10 25 LUBRICATION POINTS 5 3 mm 2 1 in SAMPLE...
Page 414: ...10 26 SERVICING INFORMATION FUEL TANK INSTALLATION 1 Cut after clamping 2 Frame Inside SAMPLE...
Page 418: ...10 30 SERVICING INFORMATION LEFT SIDE COVER INSTALLATION SAMPLE...
Page 453: ...Prepared by December 2004 Part No 99500 38050 01E Printed in Japan 456 SAMPLE...
Page 454: ......