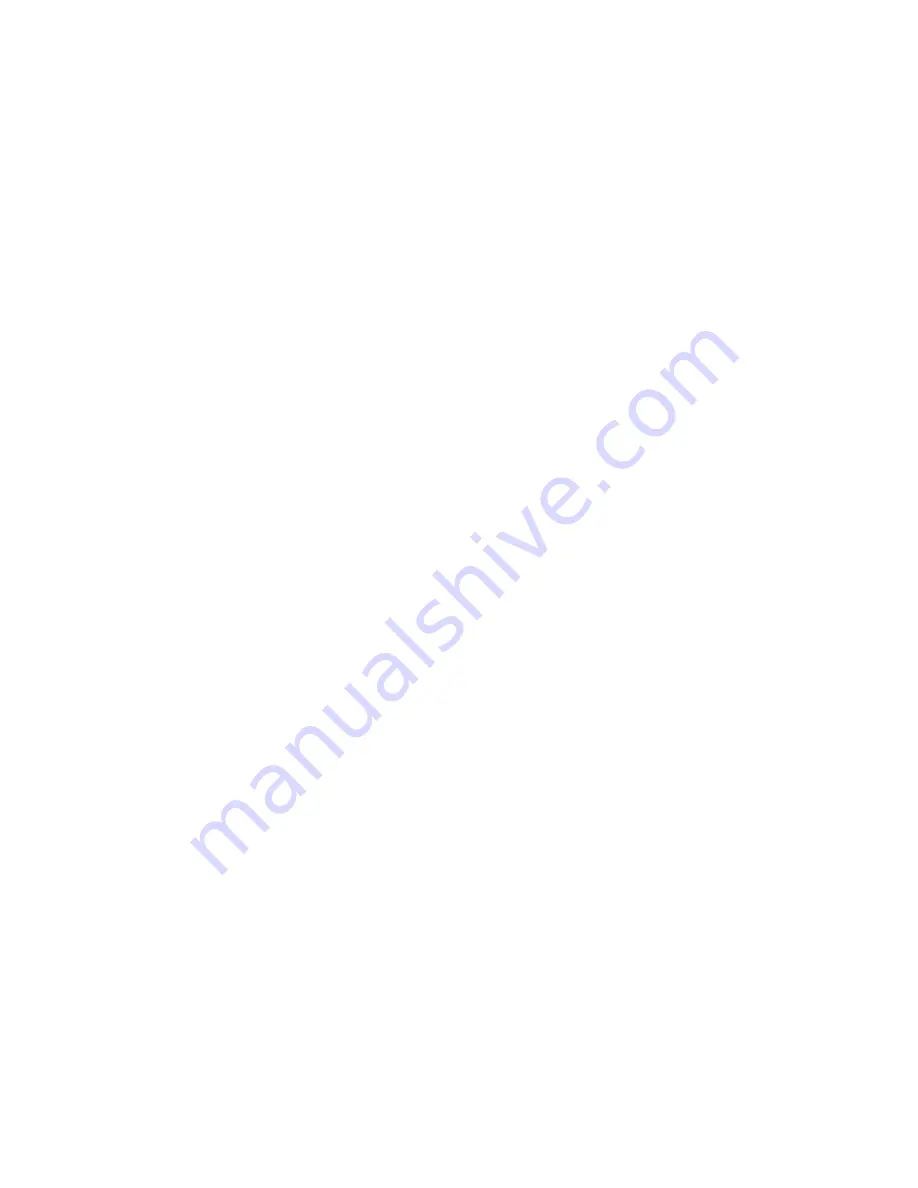
xiv
Sun Enterprise Tape Library 7/3500 Field Service Manual • July 1997
▼
To Use These Procedures for Troubleshooting
47
Fault Isolation Entry MAP
48
Error Message Entry MAP
49
Mechanical Inspection Entry MAP
50
Online Initialization Entry MAP
51
Online Test Entry MAP
52
Diagnostic Test Entry MAP
53
Host Interface Failure MAP
54
Library Operation Failure MAP
55
Control Panel and Load Port Debug MAP
56
Control Panel and Load Port Debug MAP (Cont.)
57
Motor Power Interlock Clearing MAP
58
Run Diagnostics MAP
59
Diagnostics Initialization MAP
60
Power Entry MAP
61
Self-Test All MAP
62
Self-Test All MAP (Cont.)
63
Home All MAP
64
Inventory MAP
65
Calibration MAP
66
Robotics Controller Fuse Isolation Entry MAP
67
Actuator Driver Fuse Isolation Entry Map
68
Power Supply Evaluation Entry MAP
69
Power Supply Evaluation Entry MAP (Cont.)
70
Gripper Self-Test Failure MAP
71
Extension Self-Test Failure MAP
72
Vertical Self-Test Failure MAP
73
Summary of Contents for Enterprise Tape Library 7/3500
Page 10: ...x Sun Enterprise Tape Library 7 3500 Field Service Manual July 1997 ...
Page 26: ...xxvi Sun Enterprise Tape Library 7 3500 Field Service Manual July 1997 ...
Page 28: ...xxviii Sun Enterprise Tape Library 7 3500 Field Service Manual July 1997 ...
Page 76: ...46 Sun Enterprise Tape Library 7 3500 Field Service Manual July 1997 ...
Page 118: ...88 Sun Enterprise Tape Library 7 3500 Field Service Manual July 1997 ...
Page 192: ...162 Sun Enterprise Tape Library 7 3500 Field Service Manual July 1997 ...
Page 231: ...Glossary 3 ZIF connector Zero insertion force connector ...
Page 232: ...4 Sun Enterprise Tape Library 7 3500 Field Service Manual July 1997 ...
Page 242: ...10 Sun Enterprise Tape Library 7 3500 Field Service Manual July 1997 ...