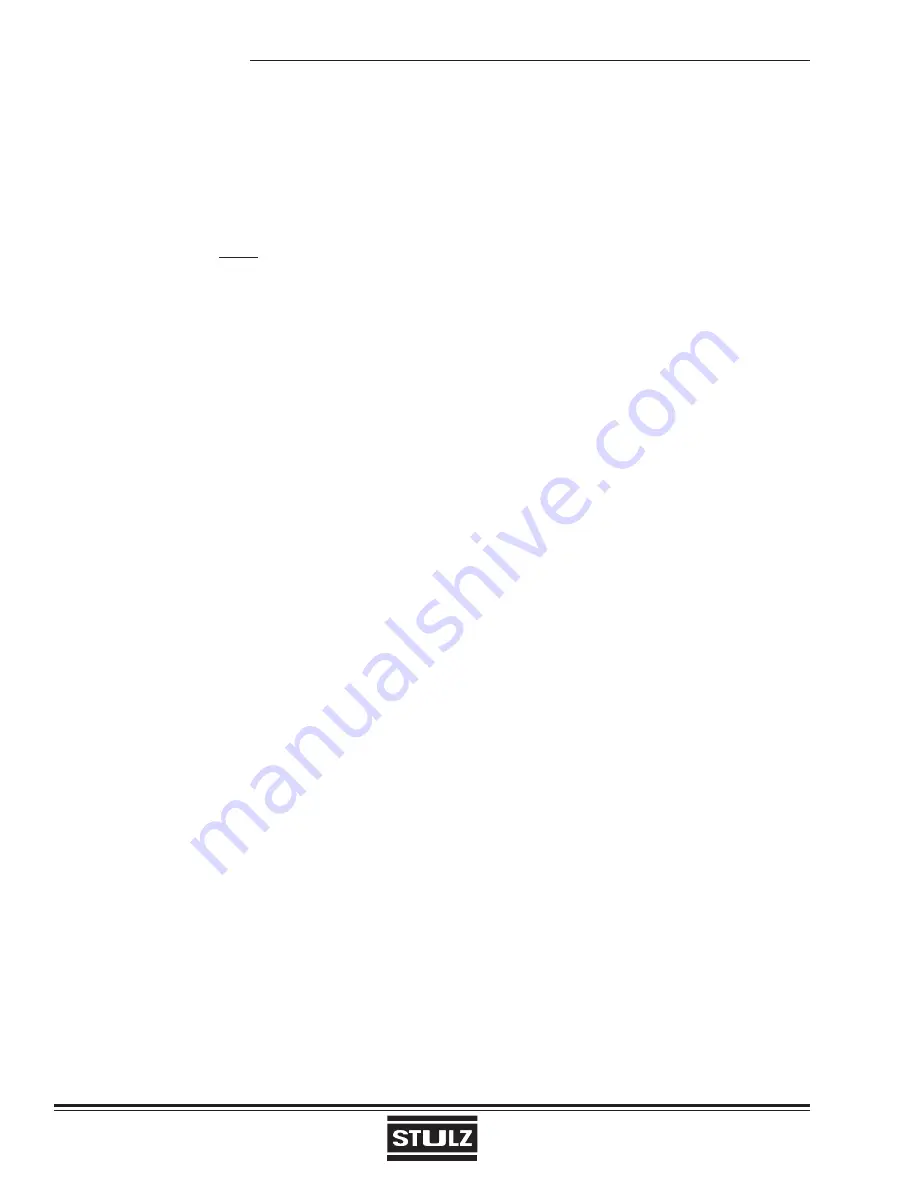
(© Oct, 2007)
Air Technology Systems, Inc.
Compact CW Series Installation, Operation & Maintenance Manual
3-1
3.0
START-UP/COMMISSIONING
3.1
Operation
For new installations, ensure the unit is ready to
operate by going through the Checklist for Completed
Installation, located in Appendix A, prior to start-up.
NOTE
A Warranty Registration and Start-Up Checklist
is provided with the unit data package. It should
be completed during start-up and sent to SATS.
This checklist should be used as a guideline for
items that need to be confirmed during start-up.
Start-up must be performed by a journeyman, refrig-
eration mechanic or an air conditioning technician.
3.2
Step by Step Start-Up Instructions
1.
Replace all equipment removed prior to performing
start-up checks.
2.
Ensure that the control circuit breakers, fan motor
starter switch and additional built in optional
equipment power switches are turned on.
3.
Apply power to the
Compact CW system at the
main power disconnect switch.
4.
Turn on the A/C unit at the system controller and
set the desired values (setpoints) for room
temperature and humidity. (Refer to the separate
controller operation instructions included in the
data package with your unit.)
5.
Ensure that all blowers and fans are rotating
correctly and freely without any unusual noise.
6.
Test cooling operation by setting the temperature
setpoint below actual room temperature. The
chilled water valve should open and the discharge
air should feel cooler than the return air.
7.
Test humidification operation by creating a
demand for humidification. Use an amp meter to
determine current draw of the humidifier. Visually
check for vapor leaving the steam head or feel if
the cylinder is warm to verify if the humidifier is
operational. In all cases, 1 to 6 hours might be
required to see a desired level or rise in humidity
in the conditioned space. Once room conditions
have been programmed or set, a repeat visit to the
conditioned space may be required to ensure the
humidifier is meeting the room's requirements.
8.
Test dehumidification operation by creating a
demand for dehumidification. If necessary, set the
dehumidification setpoint 10% below actual room
conditions (the set point may already be below the
actual room conditions, especially at start-up).
The chilled water valve should open to begin the
dehumidification process. While in this mode, room
temperature may decrease and the reheat function
may activate. As conditions in the room change,
you may have to readjust the setpoint as you
check operation. An adequate heat load within the
space is required.
9.
For Electric Reheat, use an amp meter on the
heater circuit to determine if the heater is opera-
tional. For Hot Water Reheat ensure that the
control signal has energized the control valve and
the temperature of the water has decreased as it
passes through the unit. In all cases, 1 to 6 hours
might be required to see a desired level or decrease
in humidity in the conditioned space. Once room
conditions have been programmed or set, a repeat
visit to the conditioned space may be required to
ensure the dehumidification mode is meeting the
room’s requirements.
3.3
Microprocessor Controller Programming
The microprocessor controller is factory programmed
based on the optional features selected. Most applica-
tions require no field start-up or program adjustment
beyond setting the current date and time. Separate
operating instructions for the controller have been sent
with your unit, including each feature's factory "default"
setting and the available adjustment range, if appli-
cable.