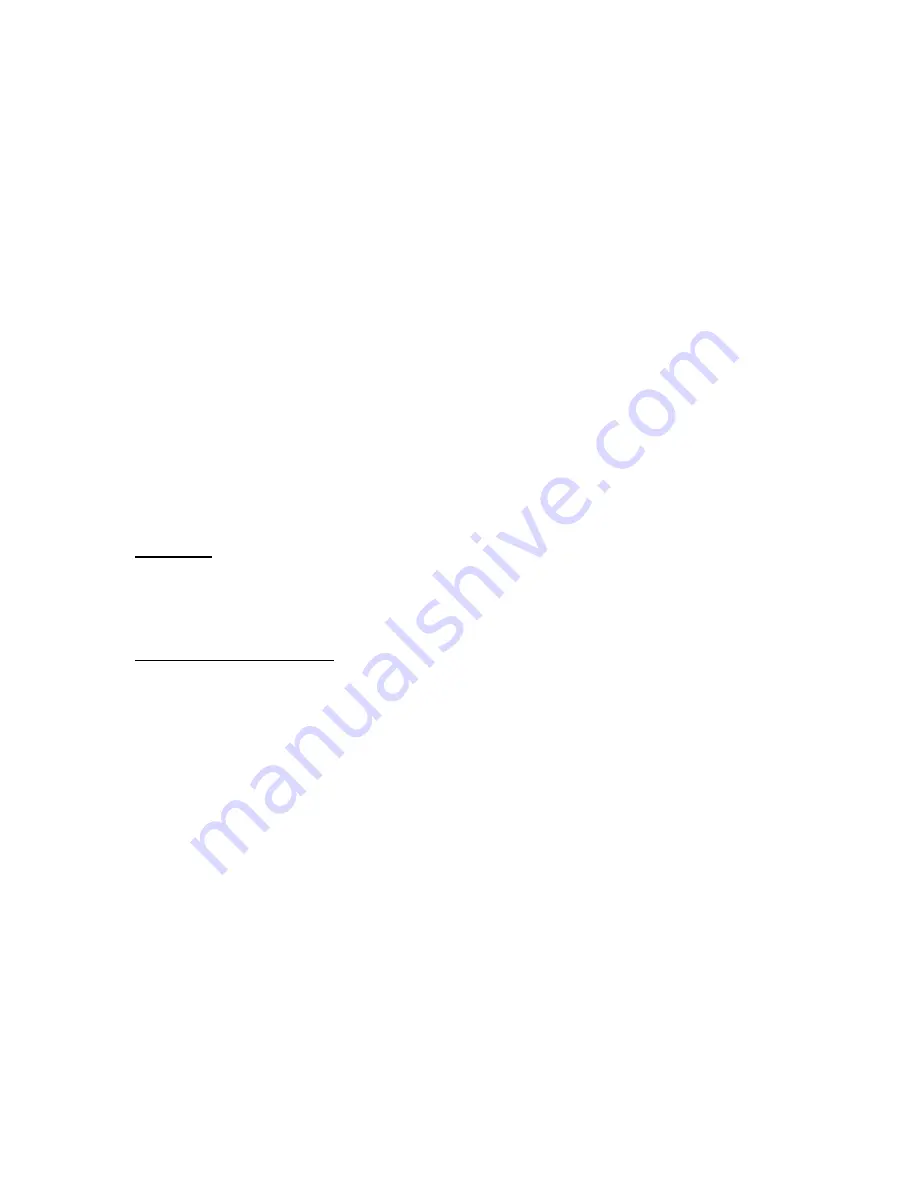
DISOCONT® Tersus (DT-9) Configuration and Operations Manual
©Schenck Process Group
11
The microprocessor computes the feeder belt load by repeatedly reading the voltage signal from each
load cell and converting the signal into a digital value (binary number) using an analog to digital (A/D)
converter. Each value is then compared to parameters stored in permanent memory to determine if
the signal is within acceptable limits, and if it is, it is stored for use. The same operation is then
performed on the other load cell, and the signals are compared to each other to test their validity. If
the signals are determined to be invalid, the feeder is switched to volumetric operation and the
controller uses a simulated belt load calculated from an historical average stored in memory. If the
signals are determined to be valid, the two load cell signals are summed, the tare is subtracted and
the result is multiplied by a scaling factor based on the load cell data specified in P04.01 LC
Characteristic Value and P04.02 LC Rated Capacity to determine the nominal weight of material on
the belt. This nominal value is then multiplied by the three range correction factors (P10.03, P10.04
and P10.05) to determine the actual weight (QB).
The belt load (Q) is computed from the total weight (QB) as follows:
Q = QB / Leff
Q = Belt load in kg/m
QB = Weight of load on platform in kg
NOTE:
The 196NT parameter 10 Weigh Span Length is the full distance between the two weigh span
rollers. The DT-9 parameter P04.03 Effective Platform Length is half the distance between the two
weigh span rollers. For any given feeder, the value used by the DT-9 should be one half of the value
used by the 196NT.
Belt Speed
During normal feeder operation, the belt speed is calculated from the motor RPM rather then being
measured directly. The relation ship between motor speed and belt speed is determined during
calibration and is displayed as P10.02 Pulses per Length.
Feedrate Control and Totals
The weigh and speed information is used to calculate the actual feedrate as shown.
Feedrate (I) = Belt load (Q) x Belt Speed (V)
The feeder control accepts a feedrate set point from the source selected using parameter P03.02
Feedrate Setpoint. This signal is compared with a computed feedrate derived from measured weight
and speed signals to generate the system error signal which is used to adjust the speed of the motor.
Compensation for system stability is provided in the software using parameters P11.01 P-Component
KP and P11.02 I-Component TN. These calculations are repeated periodically and at each iteration,
the actual feedrate is multiplied by the time interval to calculate the totalizer increment. Separate
totals are kept for gravimetric and volumetric operation.
Summary of Contents for DISOCONT Tersus DT-9
Page 2: ......
Page 8: ...DISOCONT Tersus DT 9 Configuration and Operations Manual Schenck Process Group 6 ...
Page 30: ...DISOCONT Tersus DT 9 Configuration and Operations Manual Schenck Process Group 28 ...
Page 40: ...DISOCONT Tersus DT 9 Configuration and Operations Manual Schenck Process Group 38 ...
Page 50: ...DISOCONT Tersus DT 9 Configuration and Operations Manual Schenck Process Group 48 ...
Page 150: ...DISOCONT Tersus DT 9 Configuration and Operations Manual Schenck Process Group 148 ...
Page 154: ...DISOCONT Tersus DT 9 Configuration and Operations Manual Schenck Process Group 152 ...