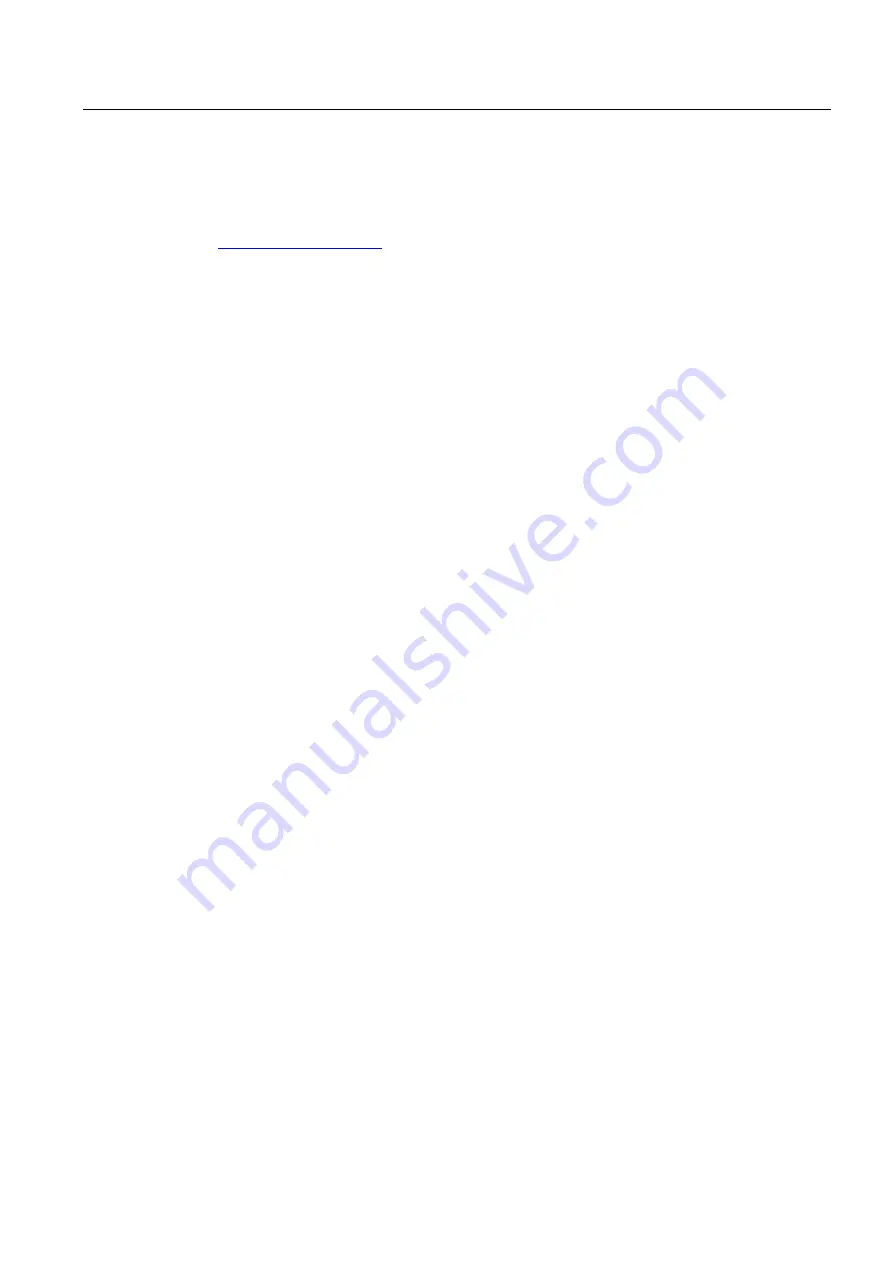
Connection to a fieldbus
6.3 Communication via PROFIBUS
Inverter with CU240B-2 and CU240E-2 Control Units
Operating Instructions, 07/2010, FW 4.3.2, A5E02299792B AA
123
6.3.4
Acyclic communication
The contents of the transferred data set corresponds to the structure of the acyclic
parameter channel according to the PROFIdrive profile, Version 4.1
(
The acyclic data transfer mode generally allows:
● The transfer of large volumes of user data (up to 240 bytes). A parameter
request/response must fit into a data set (max. 240 bytes). The requests/responses are
not distributed over several data sets.
● Transfer of complete fields or field parts or the complete parameter description.
● Transfer of different parameters in one access (multiple request).
● Reading of profile-specific parameters over an acyclic channel
● Acyclic data transfer in parallel with cyclic data transfer.
Only one parameter request is processed at a time (no pipelining). No spontaneous
messages are transferred.
6.3.4.1
Acyclic communication over PROFIBUS DP (DP V1)
The PROFIBUS DP expansions DPV1 comprise the definition of acyclic data exchange.
It supports concurrent access by other PROFIBUS masters (Class 2 master, e.g.
commissioning tool).
Suitable channels are provided in the inverters of the SINAMICS G120 series for the
different masters/different data transfer types:
● Acyclic data exchange with the same Class 1 master using the DPV1 functions READ
and WRITE (with data set 47 (DS47)).
● Acyclic data exchange with the help of a SIEMENS startup tool (Class 2 master, e.g.
STARTER). The startup tool can acyclically access parameters and process data in the
inverter.
● Acyclic data exchange with a SIMATIC HMI (Human Machine Interface) (second Class 2
master). The SIMATIC HMI can acyclically access parameters in the inverter.
● Instead of a SIEMENS startup tool or a SIMATIC HMI, it is also possible for an external
master (Class 2 master) as defined in the acyclic parameter channel according to the
PROFIdrive profile, Version 4.1 (with DS47), to access the inverter.
An example of acyclic data transmission can be found in the STEP 7 program example for
acyclic communication (Page 126) section.