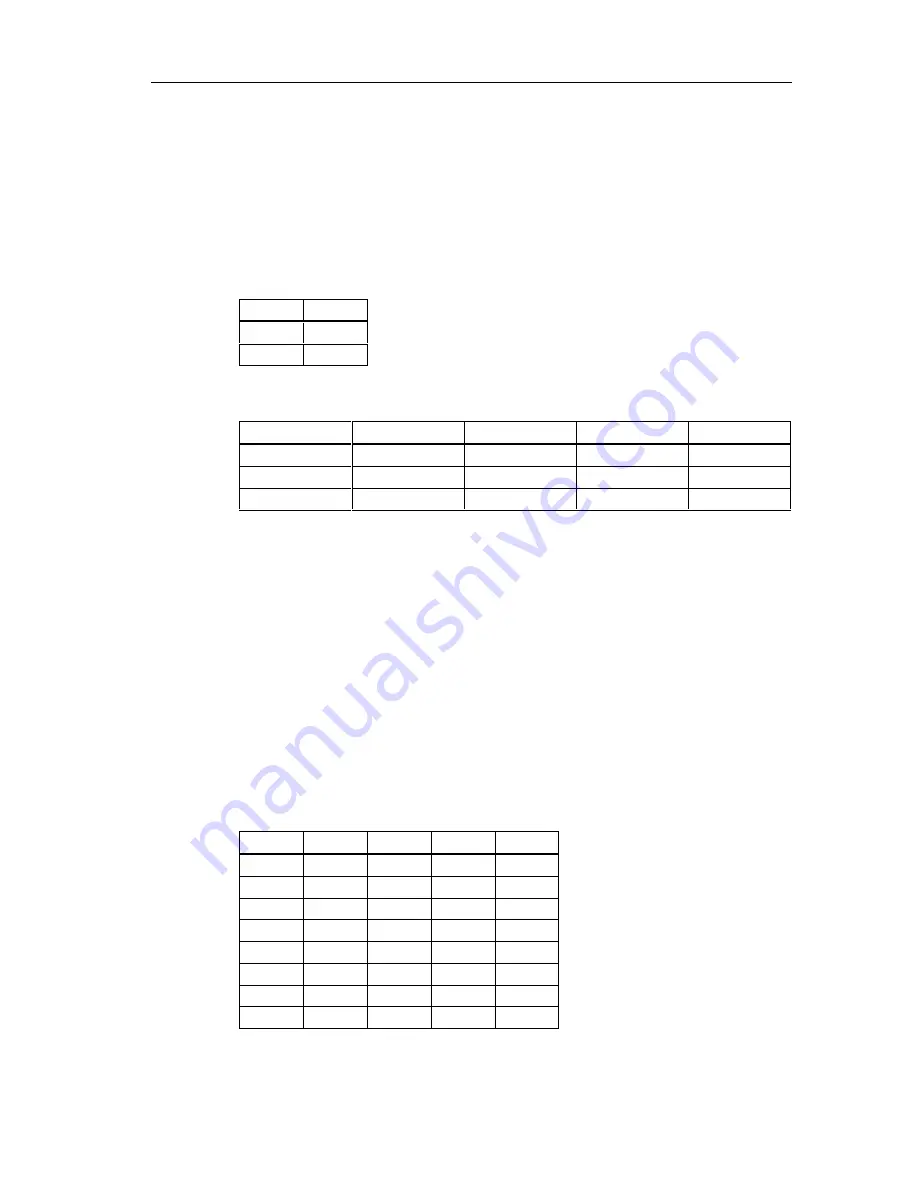
Fail-Safe Blocks
Fail-Safe Systems
A5E00085588-03
8-89
8.7.4 F_NOT
Function
The block inverts the input.
Truth Table
IN
OUT
0
1
1
0
I/Os
Name
Data Type
Explanation
Default
Input:
IN
F_BOOL
Input
0
Output:
OUT
F_BOOL
Output
1
Error Handling
None
8.7.5 F_2OUT3
Function
This block monitors three binary inputs for signal state 1. The output OUT is 1 if at
least two inputs are 1. Otherwise, the output is 0. The output OUTN corresponds to
the negating output OUT.
Truth Table
IN1
IN2
IN3
OUT
OUTN
0
0
0
0
1
0
0
1
0
1
0
1
0
0
1
0
1
1
1
0
1
0
0
0
1
1
0
1
1
0
1
1
0
1
0
1
1
1
1
0
Summary of Contents for SIMATIC S7 F
Page 8: ...Important Information Fail Safe Systems viii A5E00085588 03 ...
Page 16: ...Contents Fail Safe Systems xvi A5E00085588 03 ...
Page 38: ...Product Overview Fail Safe Systems 1 22 A5E00085588 03 ...
Page 56: ...Getting Started Fail Safe Systems 2 18 A5E00085588 03 ...
Page 70: ...Safety Mechanisms Fail Safe Systems 3 14 A5E00085588 03 ...
Page 115: ...Programming Fail Safe Systems A5E00085588 03 5 33 Examples Receive Block Send Block ...
Page 154: ...Programming Fail Safe Systems 5 72 A5E00085588 03 ...
Page 166: ...Operation and Maintenance Fail Safe Systems 6 6 A5E00085588 03 ...
Page 332: ...Fail Safe Blocks Fail Safe Systems 8 144 A5E00085588 03 ...
Page 344: ...References Fail Safe Systems B 2 A5E00085558 03 ...
Page 350: ...Glossary Fail Safe Systems Glossary 6 A5E00085588 03 ...