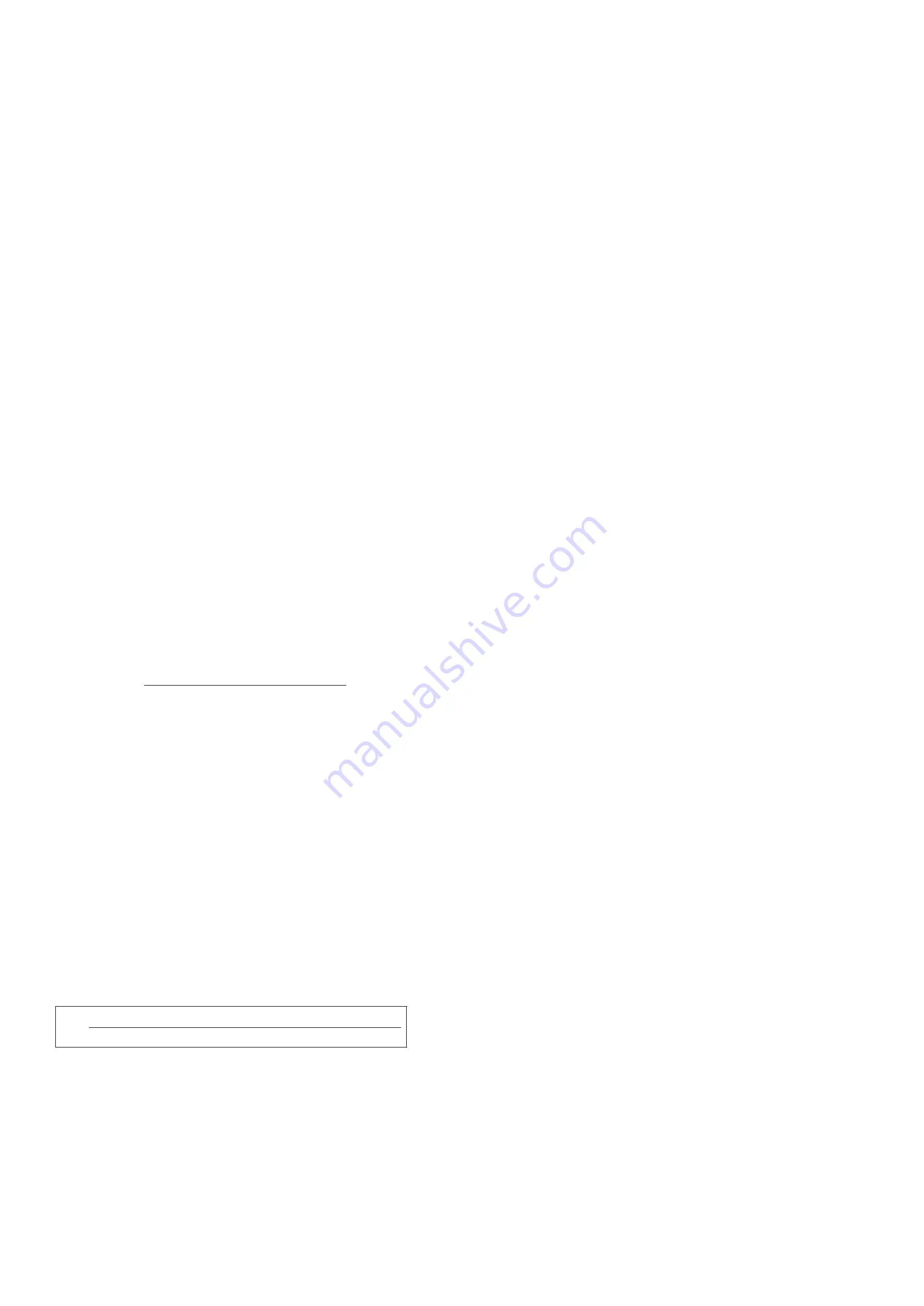
Analog Value Processing
S5-115F Manual
6.5
Wire-break Signalling and Scanning
Wire-break signalling in the 460 analog input module
There are three methods of detecting wire-break:
Wire-break detection per hardware:
This is implemented with the 498-1AA11 range card. A constant current is briefly switched
(1.6 ms) through the input terminals before each coding of the input value and the resulting
voltage is checked for a limit. The voltage exceeds the limit value if there is a sensor or line
interrupt and wire-break is signalled by setting the condition code bit ”F” in data byte 1. This is
evaluated by FB 250 ANEI ( 6.9).
Wire-break monitoring with FB 250 ANEI
The 460 AI module with the range cards 498-1AA51 or 498-1AA71 and the 463 AI module with
jumpers set for the range 4 to 20 mA use the live-zero method for detecting wire-breaks:
If the sensors, signal path and input module are all intact, 4 mA is the lowest permissible value.
All values lower than 3 mA are interpreted by FB 250 ANEI as wire-breaks.
Wire-break detection per user program and FB 250 ANEI
All measuring ranges of the two AI modules which do not permit wire-break detection as in
and above must use the following procedure supported by the user program.
For this purpose, a wire-break range in the standardized value range must be defined with the
ODGR and UDGR parameters.
The error bit ”FB” is set in FB 250 in the following cases:
• If the analog value lies within the limits ODGR and UDGR
• If the DRAK bit is set in the control program ( 6.9).
Using this procedure to test the line for wire-break only makes sense if the analog value lies
outside the wire-break limits.
Note
The L PB and L PW operations are not permitted for analog value processing.
6-26
EWA 4NEB 811 6148-02