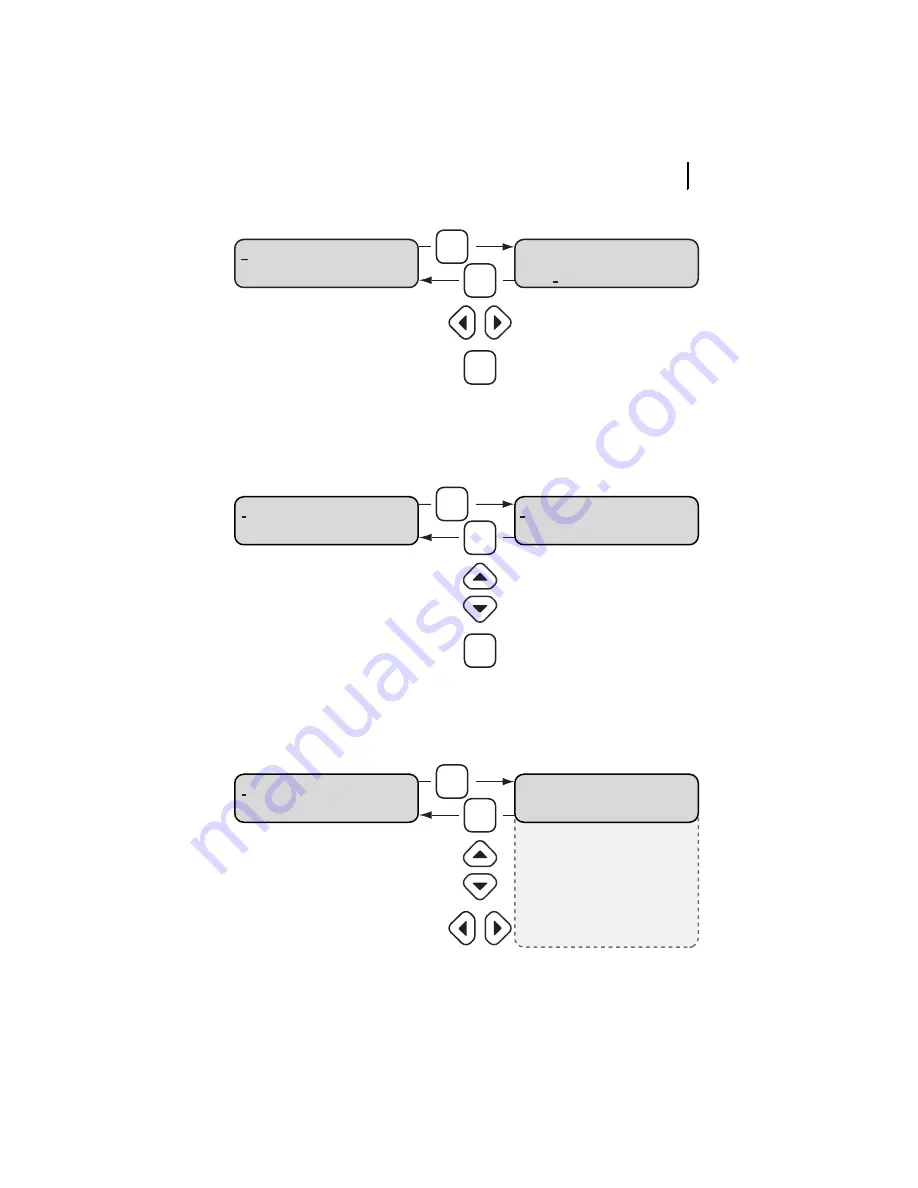
Date Code 20011009
SEL-701-1 Monitor
Front-Panel Operation
Front-Panel Main Menu
4.17
Figure 4.23
Meter Values Reset Functions.
Figure 4.24
Main Menu: History Data Function.
Figure 4.25
History Data\Display History Function.
To move between Yes and No.
Yes: Initiates action;
No: Returns to Meter Values Menu.
To select underlined option.
Reset Demand Peaks
Reset Demand Peaks?
Yes No
Meter Values Menu Item
Reset Demand Peaks Function
ESC
ENTER
ENTER
History Data
Display History
Clear History
Main Menu Item
History Data Menu
Press these keys
to move within the list.
Press this key to select
an underlined menu item.
ESC
ENTER
ENTER
Trip Type:
.
.
.
1
kVA= 452.6
PF = 0.85 LAG
Move among
data for this event.
Display History
1
Date: 03/18/1999
Time: 06:31:02.257
Move among events.
History Data Menu Item
ESC
ENTER
Display History Function
Summary of Contents for SEL-701-1
Page 16: ...This page intentionally left blank ...
Page 18: ...This page intentionally left blank ...
Page 20: ...This page intentionally left blank ...
Page 34: ...This page intentionally left blank ...
Page 118: ...This page intentionally left blank ...
Page 142: ...This page intentionally left blank ...
Page 196: ...This page intentionally left blank ...
Page 210: ...This page intentionally left blank ...
Page 242: ...This page intentionally left blank ...
Page 384: ...This page intentionally left blank ...