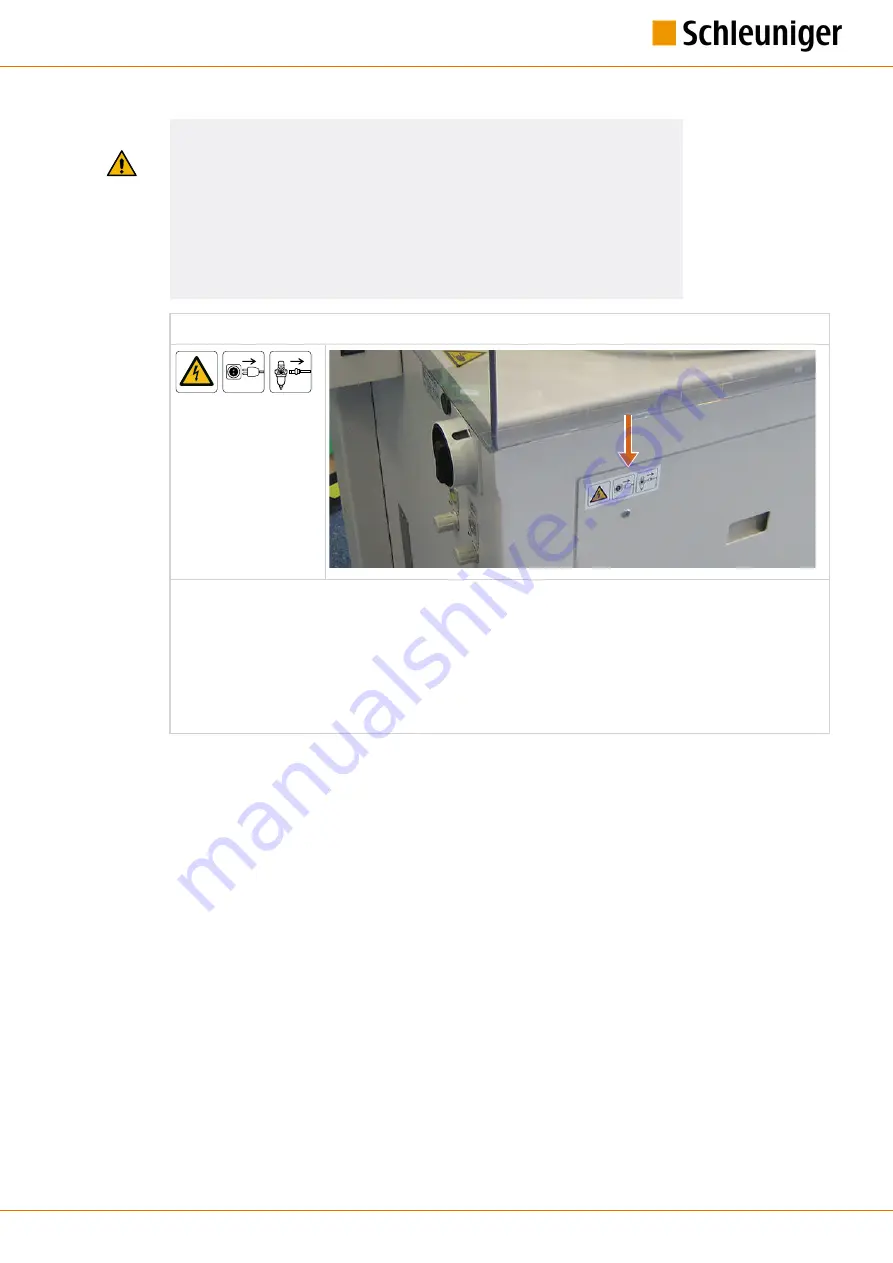
5. Product description
Reference Manual |Edition 5.0 (09-2016) |
CoaxCenter 6000
37 | 194
CAUTION
Personal and property damage when product is operated by
untrained or not properly trained personnel.
Employment of insufficiently qualified personnel by ignorance in handling the
product and their potential hazard may lead to personnel injury and property
damage.
■
Operate the product only by trained personnel
■
Carry out regular staff training
Unplug machine from the mains- and compressed air supply
There is a danger of electric shock by contact with parts inside the machine and on the mains con-
nection. Touching electric components can cause injury to the operator personnel. Unintentional
operation of pressurized components, or unintentionally escaping compressed air can cause injury.
Therefore always before opening the machine:
■
Turn off the main switch, block against switching on again and disconnect the machine from the
mains (for hard wired machines, the main switch serves as a mains disconnecter).
■
Unplug the machine from the compressed air supply.
Summary of Contents for CoaxCenter 6000
Page 4: ...Topic list 4 194 Reference Manual Edition 5 0 09 2016 CoaxCenter 6000...
Page 10: ...Table of contents 10 194 Reference Manual Edition 5 0 09 2016 CoaxCenter 6000...
Page 22: ...3 Transportation 22 194 Reference Manual Edition 5 0 09 2016 CoaxCenter 6000...
Page 48: ...5 Product description 48 194 Reference Manual Edition 5 0 09 2016 CoaxCenter 6000...
Page 78: ...7 General handling operation 78 194 Reference Manual Edition 5 0 09 2016 CoaxCenter 6000...
Page 110: ...10 User interface user levels 110 194 Reference Manual Edition 5 0 09 2016 CoaxCenter 6000...
Page 122: ...11 Diagnostics troubleshooting 122 194 Reference Manual Edition 5 0 09 2016 CoaxCenter 6000...
Page 154: ...15 Decommissioning disposal 154 194 Reference Manual Edition 5 0 09 2016 CoaxCenter 6000...
Page 155: ...16 Appendix Reference Manual Edition 5 0 09 2016 CoaxCenter 6000 155 194 APPENDIX...
Page 161: ...16 Appendix Reference Manual Edition 5 0 09 2016 CoaxCenter 6000 161 194...
Page 162: ...16 Appendix 162 194 Reference Manual Edition 5 0 09 2016 CoaxCenter 6000 16 2 PNEUMATIC SCHEMA...
Page 163: ...16 Appendix Reference Manual Edition 5 0 09 2016 CoaxCenter 6000 163 194...
Page 174: ...16 Appendix 174 194 Reference Manual Edition 5 0 09 2016 CoaxCenter 6000...
Page 186: ...16 Appendix 186 194 Reference Manual Edition 5 0 09 2016 CoaxCenter 6000...
Page 187: ...Personal notes Reference Manual Edition 5 0 09 2016 CoaxCenter 6000 187 194...
Page 188: ...Personal notes 188 194 Reference Manual Edition 5 0 09 2016 CoaxCenter 6000...
Page 193: ......
Page 194: ......