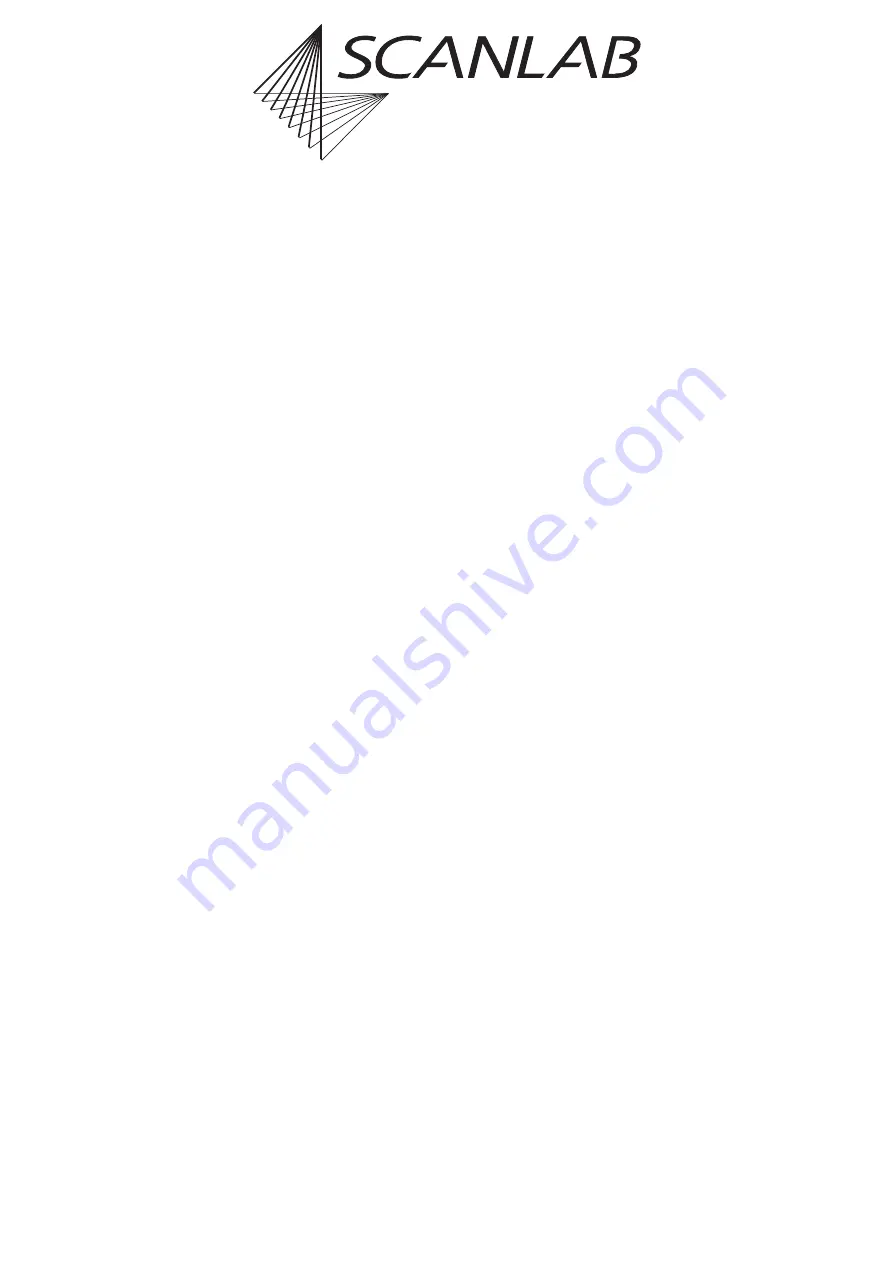
RTC
®
5 PC Interface Board
Rev. 1.9 e
2 Product Overview
34
innovators for industry
Changed Timing Behavior
The following RTC
®
4 list commands are processed by
the RTC
®
5 as “short list commands”. This can result
in a changed timing behavior during execution (see
).
•
•
•
•
(changed, depending on the memory
configuration)
•
•
•
•
•
•
•
•
(Firmware changed)
•
•
•
•
•
(enhanced)
•
(changed)
•
•
•
•
•
Likewise, automatic delay adjustments can produce a
changed timing behavior (see
2.7.3 New and Changed Function-
ality
Interface to the PC
• The RTC
®
5 software drivers supports simulta-
neous control of any number of RTC
®
5 boards in
• Connectors and commands for master/slave
synchronization of multiple RTC
®
5 boards (see
)
Scan System Control
• New interface to the scan system (see
– 9-pin female D-SUB connector at the RTC
®
5
slot cover and on-board 10-pin connector
– SL2-100 transfer protocol
– 2 data channels each for both scan head con-
nectors
– Galvanically isolated signals
– 20-bit positioning resolution (see
)
– Enhanced status return from the scan system
)
– Control and status channels for enhanced data
transfer with i
DRIVE
®
scan systems
(intelli
SCAN
®
, intelli
SCAN
de
®
, intelli
DRILL
®
,
intelli
cube
®
, intelli
WELD
®
, vario
SCAN
de
)
• An XY2-100 converter is provided for data
transfer according to the XY2-100 protocol (see
). The RTC
®
5 provides power for this
converter.
– 25-pin female D-SUB connector
– 16-bit positioning resolution
– Status return according XY2-100 or XY2-100
Enhanced protocol
– Transfer synchronization is configurable for
long data cables via solder jumpers in the
XY2-100 converter
• For optical data transfer between the RTC
®
5 and
scan systems,
no
special variant of the RTC
®
5
(with XY2-100-O interface) is required. Optical
data transfer can be realized via a SCANLAB data
cable with electrical-to-optical conversion in its
D-SUB connector housing (see
).