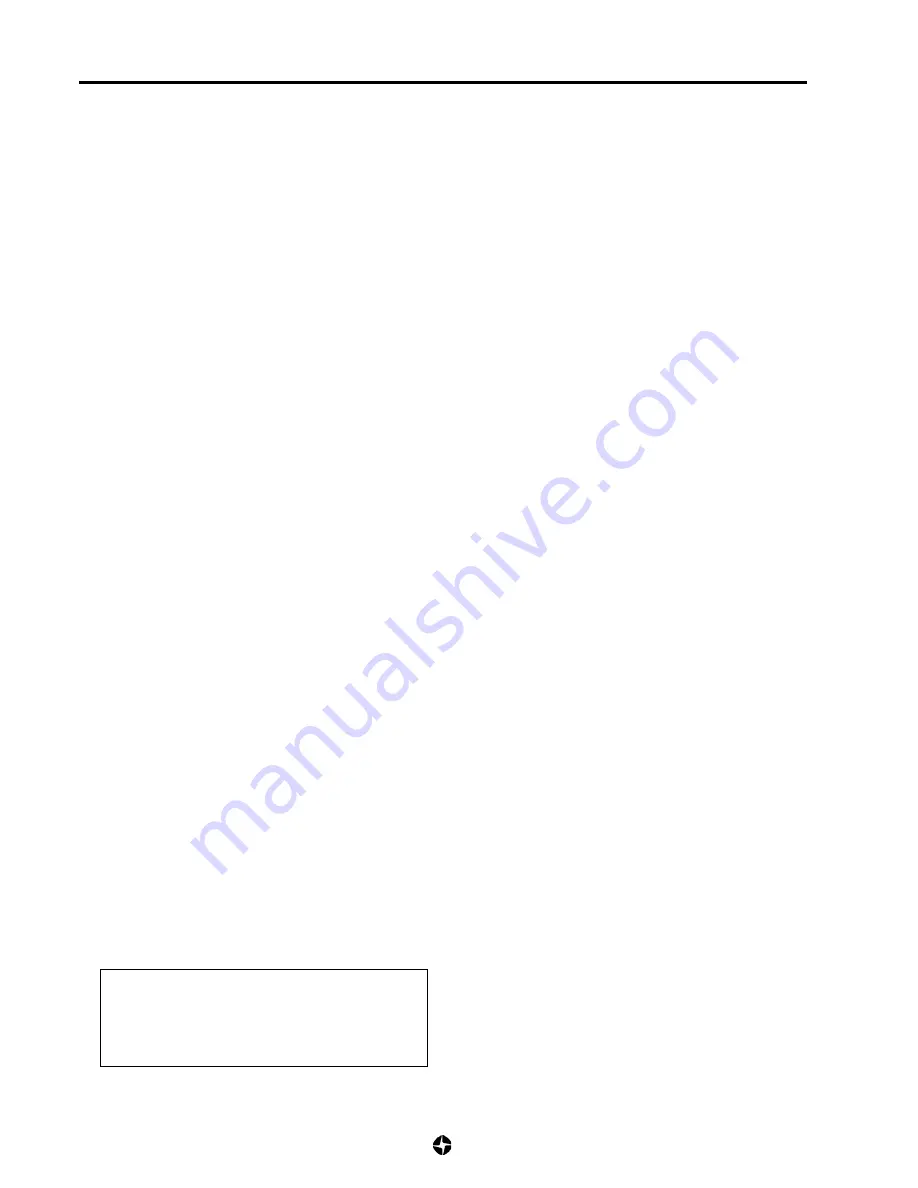
ENGINE REPAIR 6A-83
Installation
1) Proceed in reversing removal procedures. Apply the
specified tightening torques and noting the following
remarks:
• Revise the worthiness of pushing ball bearing,
pressure plate and disc of clutch.
• Apply in the end of primary shaft recommended
grease.
• Be cautious when trying to connect engine and gear
box avoiding catches and over efforts caused by
misalignments.
• Verify the worthiness of silentblocks at the front
seatings replacing them if worn or damaged.
• Check the worthiness of air and water hoses, vacuum
hoses, servosteering hydraulic hoses, fuel pipes,
impermeabilizing gaskets, braces, exhaust tube
supports, etc... Substitute those pieces where
damage or aging are detected.
• While install, be sure there are no rubbings of pipes
and hoses with metallic parts or between themselves;
no bendings or crushings.
• Make sure that the electric leads are firmly connect.
Tightening torques:
• Nuts for connection gear box to engine:
4 ÷ 6 Kg-m (40 ÷ 60 Nm)
• Screws for connection gear box to engine:
4 ÷ 6 Kg-m (40 ÷ 60 Nm)
• Nuts of the connection silentblocks to supports:
4,9 Kg-m (49 Nm)
• Linkage (38) sending oil to steering box:
3 ÷ 4 Kg-m (30 ÷ 40 Nm)
• Linkage (37) inlet oil to pump:
3 ÷ 4 Kg-m (30 ÷ 40 Nm)
• Supply and return raccord of fuel:
2,5 Kg-m (25 Nm)
(mechanical injection
(mechanical injection
(mechanical injection
(mechanical injection
(mechanical injection
engine ).
engine ).
engine ).
engine ).
engine ).
2) Execute the following tasks:
• Refill an level engine with engine oil (see 0B-5, point
1.3).
• Fille, purge and level of refrigerant circuit (see 0B-8,
point 1.5).
• Fuel supply system purge (see 6C-8).
• To fill and level servosteering hydraulic circuit
servosteering hydraulic circuit purge (see 0B-27, point
4.7).
• Servosteering hydraulic circuit purge (see 3B-12).
3) If vehicle fit air conditioning, plenish gage with
necessary equipment.
CAUTION:
Before start engine, fill central body of
turbocharger with oil through supply sleeve;
use new engine oil.
Checks and controls
1) Start engine and leave it at a rev. regime slightly over ticking
over regime, wait till the coolant comes to a temperature
ensuring the opening of thermostat (94ºC to 110ºC).
Afterwards, check the following points:
• There are no water leaks through the unions of houses
of refrigeration circuit.
• There are no oil leaks between the plungers cover and
cylinder head, between the oil housing and block,
between oil filter and its housing, between heat exchanger
and its housing and in the lubrication circuit.
• There are no fuel leaks through unions and linkages of
low pressure fuel pipes or through the rigid pipes of the
fuel injection.
• The light witnessing signals at the dash board work
correctly and those of control instruments which were
connected and disconnected during the removal and the
installation of engine.
NOTE:
Retighten, repair, correct or substitute any anomaly
or faulty pieces found during the corresponding
checks.
2) Do a trial driving on the road verifying everything is running
properly.
Summary of Contents for PS-10
Page 1: ......
Page 2: ......
Page 5: ......
Page 50: ......
Page 53: ...BUMPERS FRONTHOODANDFRONTAL2 3 REAR BUMPER 1 Rear bumper 2 Side pad 3 Center pad 2 3 3 1 2 ...
Page 69: ......
Page 90: ......
Page 124: ......
Page 149: ......
Page 163: ......
Page 209: ......
Page 448: ......
Page 489: ......
Page 505: ......
Page 594: ...BODYSERVICE9 31 FRAME MAIN DIMENSIONS ...
Page 595: ...9 32BODYSERVICE FRAME MAIN DIMENSIONS ...
Page 601: ...ELECTRICAL DIAGRAMS ...
Page 602: ...ELECTRICAL DIAGRAMS 2 ONLY COMMON RAIL POWER SUPPLY DIAGRAM ...
Page 605: ...ELECTRICAL DIAGRAMS 5 ONLY COMMON RAIL STARTING HEATER VALVE DIAGRAM ...
Page 606: ...ELECTRICAL DIAGRAMS 6 ONLY COMMON RAIL GLOW PLUG STARTING HEATER RELAY DIAGRAM ...
Page 607: ...ELECTRICAL DIAGRAMS 7 ONLY COMMON RAIL FUEL FILTER SENSORS DIAGRAM ...
Page 608: ...ELECTRICAL DIAGRAMS 8 ONLY COMMON RAIL DOUBLE STOP SWITCH ...
Page 609: ...ELECTRICAL DIAGRAMS 9 ONLY COMMON RAIL FUEL PUMP ...
Page 610: ...ELECTRICAL DIAGRAMS 10 ONLY COMMON RAIL DIAGNOSIS DIAGRAM ...
Page 611: ...ELECTRICAL DIAGRAMS 11 ONLY COMMON RAIL A C DIAGRAM ...
Page 612: ...ELECTRICAL DIAGRAMS 12 ONLY MECHANICAL INJECTION POWER SUPPLY DIAGRAM ...
Page 613: ...ELECTRICAL DIAGRAMS 13 ONLY MECHANICAL INJECTION GLOW PLUG RELAY DIAGRAM ...
Page 614: ...ELECTRICAL DIAGRAMS 14 ONLY MECHANICAL INJECTION INSTRUMENT PANEL ...
Page 615: ...ELECTRICAL DIAGRAMS 15 ONLY MECHANICAL INJECTION COMBINATION METER DIAGRAM ...
Page 616: ...ELECTRICAL DIAGRAMS 16 ONLY MECHANICAL INJECTION COOLING SYSTEM ...
Page 617: ...ELECTRICAL DIAGRAMS 17 GENERAL DIAGRAMS HEADLAMP LEVELING SYSTEM DIAGRAM ...
Page 618: ...ELECTRICAL DIAGRAMS 18 GENERAL DIAGRAMS REVERSE LAMP DIAGRAM ...
Page 619: ...ELECTRICAL DIAGRAMS 19 GENERAL DIAGRAMS RADIO REAR WINDOW DEFOGGER ...
Page 620: ...ELECTRICAL DIAGRAMS 20 GENERAL DIAGRAMS REAR DEMISTER STOP LAMP DIAGRAM ...
Page 621: ...ELECTRICAL DIAGRAMS 21 GENERAL DIAGRAMS HORN DIAGRAM ...
Page 622: ...ELECTRICAL DIAGRAMS 22 GENERAL DIAGRAMS TURN SIGNAL HAZARD LAMP DIAGRAM ...
Page 623: ...ELECTRICAL DIAGRAMS 23 GENERAL DIAGRAMS LAMPS DIAGRAM ...
Page 624: ...ELECTRICAL DIAGRAMS 24 GENERAL DIAGRAMS WASHER WIPER DIAGRAM ...
Page 625: ...ELECTRICAL DIAGRAMS 25 GENERAL DIAGRAMS CHARGING SYSTEM DIAGRAM ...
Page 627: ......