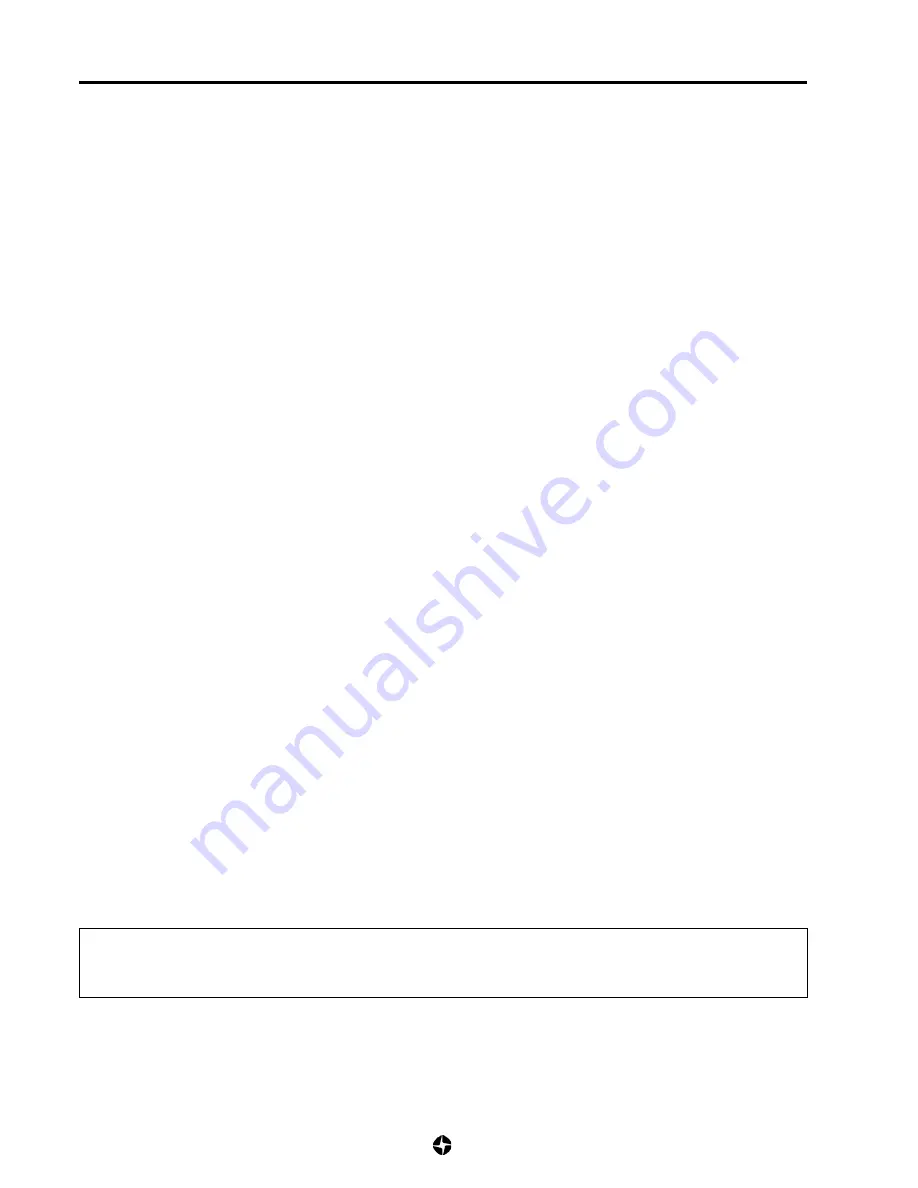
6C-26 ENGINE FUEL AND EMISSION CONTROL SYSTEM
PRECAUTION IN DIAGNOSIS TROUBLE (COMMON RAIL)
For Common Rail vehicles it is necessary to respect the following rules and warnings before carrying out any
interventions which concern the supply system components.
• Before any intervention on the engine, carry out the engine /vehicle diagnosis with the corresponding equipment and
print the results
• The replacement of the MS6.3 control board must be authorised by
SANTANA MOTOR.
• The following components must be replaced as they are irreparable: fuel flow limiter, pressure limiter valve, fuel
pressure sensor, hydraulic accumulator, supply pump, complete high pressure pump, pressure regulation valve and
electro-injectors.
• All the Common Rail system elements are packaged in oiled paper and stored in cardboard boxes. They should be
protected from humidity and only unpacked just before fitting.
• Maximum attention is needed when cleaning parts - making sure that during manipulation and fitting, be it the simple
replacement of the filter and prefilter, no impurities or foreign bodies enter the system. For this reason, the protector
plugs for the hydraulic parts and the sensors should only be removed at the moment of fitting.
• In all electrical connections it is necessary to follow the polarity.
• All nut connections must be tightened to the specified torque.
• All fuel conexions (placed over high pressure fuel pump and fuel outlet conector) must be fitted till the end. For removal,
act on clamps from hose end.
Electro-injector:
None of the joints/clamps/nuts in the injector body can be manipulated. It is neither necessary nor permitted to remove the
spray body or the electro-valve.
In the event of interventions on the high pressure pipe, the injector hexagonal side must be held with a key.
Before any intervention on the pipes, check that the injector is held in place on the cylinder head.
When dismantling/fitting the injector excess connector, the retaining spring must not be removed from its place: pushing
the spring towards the engine and exercising a vertical force will free it. When fitting, the connector is held in position and
a vertical force is applied keeping the retaining spring towards the engine.
Engine speed sensor (camshaft/flywheel)
During fitting a air gap between the sensor and pole of 0.8 ÷1.5 mm must be guaranteed while controlling the parallelism
between the reading surface and the pole plane.
High pressure pump:
No intervention is permitted on the pressure regulator or on the 3
rd
piston deadivator valve. In the event of interventions on
the high pressure pipe, the pump hexagonal side must be held with a key.
Before any intervention on the high pressure pipe, check that the pump is fixed in its place.
High pressure pipe
Each high pressure pipe should be replaced after dismantling.
Tightening or loosening of the fixing joints must be carried out with the injectors, hydraulic accumulator (Rail) and high
pressure pump perfectly fixed and holding the hexagon, component side, if room allows.
Hydraulic accumulator (Rail) and accessories
The fuel flow limiter and limiter valve can stand 5 fittings after which it is necessary to replace them. Before fitting, lubricate
them with a film of oil.
The pressure sensor must also be lubricated before fitting, with joint being replaced.
WARNING:
Given the high pressure reached by the fuel (1350 bar) it is dangerous to manipulate the high pressure pipe
outlets when the engine is running or there is pressure in the hydraulic accumulator (Rail).
Summary of Contents for PS-10
Page 1: ......
Page 2: ......
Page 5: ......
Page 50: ......
Page 53: ...BUMPERS FRONTHOODANDFRONTAL2 3 REAR BUMPER 1 Rear bumper 2 Side pad 3 Center pad 2 3 3 1 2 ...
Page 69: ......
Page 90: ......
Page 124: ......
Page 149: ......
Page 163: ......
Page 209: ......
Page 448: ......
Page 489: ......
Page 505: ......
Page 594: ...BODYSERVICE9 31 FRAME MAIN DIMENSIONS ...
Page 595: ...9 32BODYSERVICE FRAME MAIN DIMENSIONS ...
Page 601: ...ELECTRICAL DIAGRAMS ...
Page 602: ...ELECTRICAL DIAGRAMS 2 ONLY COMMON RAIL POWER SUPPLY DIAGRAM ...
Page 605: ...ELECTRICAL DIAGRAMS 5 ONLY COMMON RAIL STARTING HEATER VALVE DIAGRAM ...
Page 606: ...ELECTRICAL DIAGRAMS 6 ONLY COMMON RAIL GLOW PLUG STARTING HEATER RELAY DIAGRAM ...
Page 607: ...ELECTRICAL DIAGRAMS 7 ONLY COMMON RAIL FUEL FILTER SENSORS DIAGRAM ...
Page 608: ...ELECTRICAL DIAGRAMS 8 ONLY COMMON RAIL DOUBLE STOP SWITCH ...
Page 609: ...ELECTRICAL DIAGRAMS 9 ONLY COMMON RAIL FUEL PUMP ...
Page 610: ...ELECTRICAL DIAGRAMS 10 ONLY COMMON RAIL DIAGNOSIS DIAGRAM ...
Page 611: ...ELECTRICAL DIAGRAMS 11 ONLY COMMON RAIL A C DIAGRAM ...
Page 612: ...ELECTRICAL DIAGRAMS 12 ONLY MECHANICAL INJECTION POWER SUPPLY DIAGRAM ...
Page 613: ...ELECTRICAL DIAGRAMS 13 ONLY MECHANICAL INJECTION GLOW PLUG RELAY DIAGRAM ...
Page 614: ...ELECTRICAL DIAGRAMS 14 ONLY MECHANICAL INJECTION INSTRUMENT PANEL ...
Page 615: ...ELECTRICAL DIAGRAMS 15 ONLY MECHANICAL INJECTION COMBINATION METER DIAGRAM ...
Page 616: ...ELECTRICAL DIAGRAMS 16 ONLY MECHANICAL INJECTION COOLING SYSTEM ...
Page 617: ...ELECTRICAL DIAGRAMS 17 GENERAL DIAGRAMS HEADLAMP LEVELING SYSTEM DIAGRAM ...
Page 618: ...ELECTRICAL DIAGRAMS 18 GENERAL DIAGRAMS REVERSE LAMP DIAGRAM ...
Page 619: ...ELECTRICAL DIAGRAMS 19 GENERAL DIAGRAMS RADIO REAR WINDOW DEFOGGER ...
Page 620: ...ELECTRICAL DIAGRAMS 20 GENERAL DIAGRAMS REAR DEMISTER STOP LAMP DIAGRAM ...
Page 621: ...ELECTRICAL DIAGRAMS 21 GENERAL DIAGRAMS HORN DIAGRAM ...
Page 622: ...ELECTRICAL DIAGRAMS 22 GENERAL DIAGRAMS TURN SIGNAL HAZARD LAMP DIAGRAM ...
Page 623: ...ELECTRICAL DIAGRAMS 23 GENERAL DIAGRAMS LAMPS DIAGRAM ...
Page 624: ...ELECTRICAL DIAGRAMS 24 GENERAL DIAGRAMS WASHER WIPER DIAGRAM ...
Page 625: ...ELECTRICAL DIAGRAMS 25 GENERAL DIAGRAMS CHARGING SYSTEM DIAGRAM ...
Page 627: ......