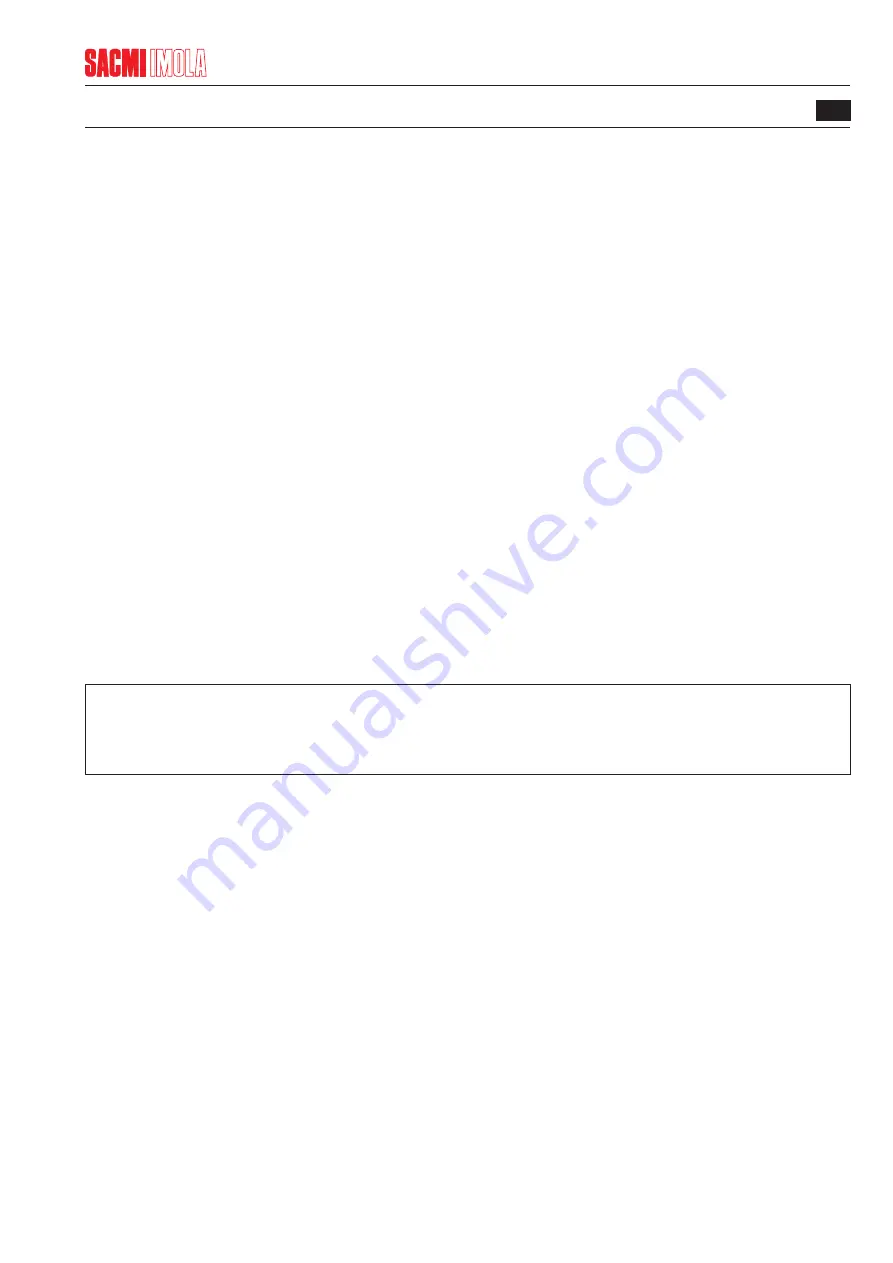
062AZ005A
ADJUSTMENTS
7
7-1
7 ADJUSTMENTS
7.1
ADJUSTING THE VISION SYSTEM
7.1.1
PROCEDURE FOR CHECKING THE ACQUISITION AND EJECTION DEVICES
This procedure is carried out to verify the sensor/encoder and reject device work correctly.
Prepare ten pieces (they can be good quality or defective pieces).
- Open the tracking/reject parameter window.
- Check sensor operation by stopping the device manually: the relative indication signal should activate on the user
interface at the same time.
- Turn on the conveyor belt and see whether the encoder, if present, works efficiently (an external encoder must be
selected). The corresponding block on the user interface should flash.
- Press the Test button to see if the reject device works in a trouble-free manner.
- Set the system to operate with the sensor in synchronized acquisition and allow the pieces to travel.
- Select the various ejection modes and check operation:
- none: no pieces should be ejected
- all: all the pieces should be ejected
- alternating: every other piece should be ejected
- group: the pieces should be ejected in groups of four.
7.1.2
PROCEDURE FOR CHECKING THE ACQUISITION AND EJECTION DEVICES
The purpose of this procedure is to verify that the vision system properly ejects all the defective pieces and none of
the good quality ones. In other words, this procedure sees whether good quality pieces are rejected or if defective
pieces are not rejected due to improper functioning of the inspection and ejection mechanisms.
- Prepare one hundred pieces that are more or less defective and one hundred pieces that are surely good quality.
- Allow the vision system to inspect the pieces using a configuration able to tell good quality pieces apart from
defective ones without any doubts.
NOTE
For example, the defective pieces can be marked with a permanent marker and a configuration that
employs one inspection region (in the area where the piece is marked) using large margins of acceptability
for that region. In any case, any configuration capable of distinguishing good quality pieces from defective
ones can be used.
- Stop the line placed before the vision system and remove any extraneous pieces from the conveyor belt.
- Use two empty containers, one for defective pieces and the other for good quality ones, to collect the pieces being
inspected on the conveyor.
- Mix the defective pieces and good quality ones together and feed them to the vision system. The normal operating
speed and spacing between the pieces should be used.
- The acquisition and ejection mechanisms work properly if all the good quality pieces are accepted and all the
defective ones are rejected by the vision system.
It is advisable to repeat this procedure a few times to be 100% certain.
On the other hand, if some defective pieces are accepted or a few good quality ones rejected, the acquisition and
ejection mechanisms are not working properly. The way in which the ejected pieces behave also has to be observed
to make sure ejection is efficient. The trouble has to be located and remedied. Once this has been done, repeat the
procedure until positive results are obtained.
Summary of Contents for Imola CHS Series
Page 2: ......
Page 4: ...062AZ005A...
Page 48: ...062AZ005A 2 FEATURES 2 32...
Page 76: ...062AZ005A 4 INSTALLATION 4 10...