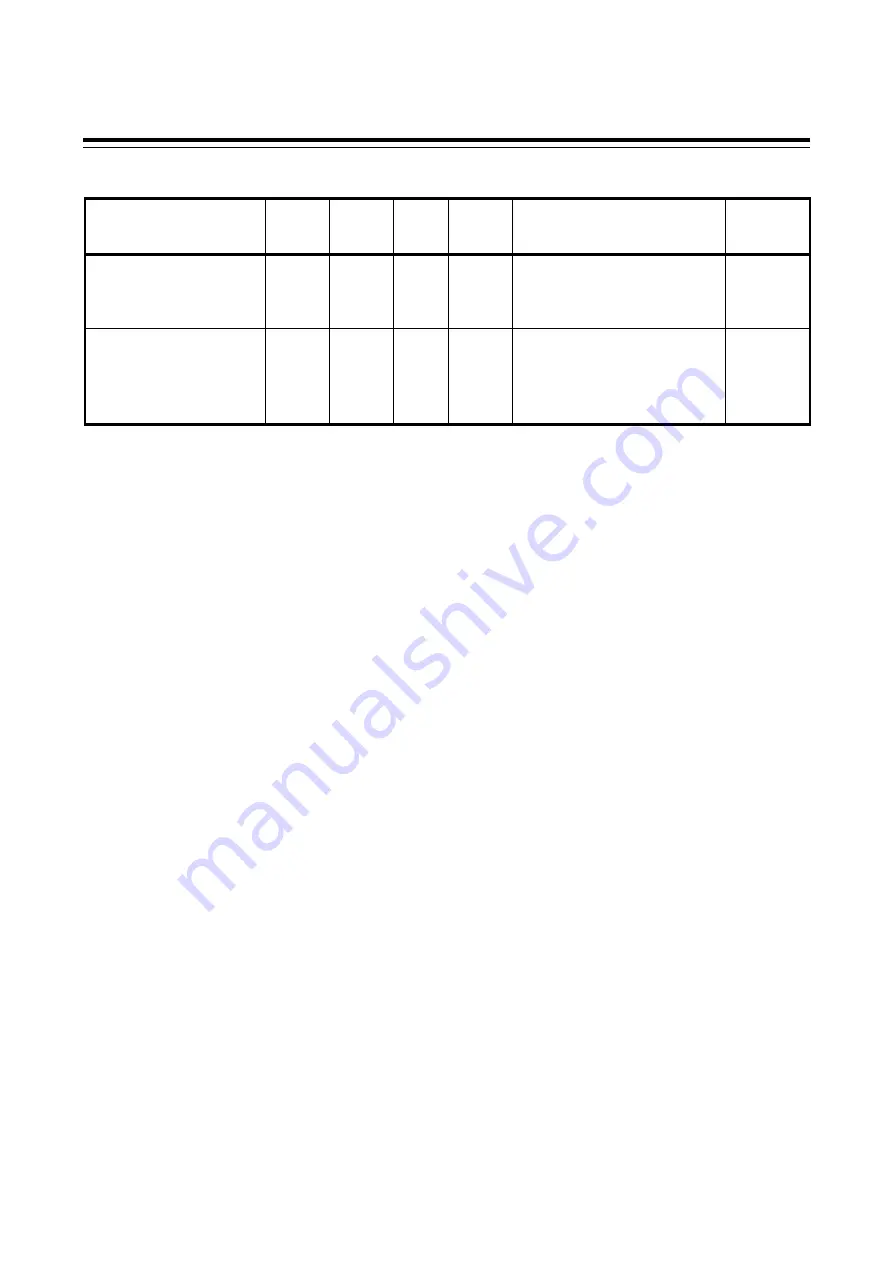
6. RKC COMMUNICATION
IMS01J02-E2
80
Continued from the previous page.
Name
Iden-
tifier
Digits Attri-
bute
Struc-
ture
Data range
Factory
set
value
PLC scanning time
setting *
[H-PCP-J]
ST
6
R/W
U
0 to 3000 ms
10
Integral time limiter at
AT end
[H-TIO- , H-CIO-A,
H-SIO-A]
GY
6
R/W
U
1 to 3600 seconds
Setting will be valid in
heat/cool control.
3600
* Set the PLC scanning time (time of waiting for a response from the PLC) so as to adapt to the
environment used.
Setting example:
Set PLC scanning time to any value more than twice as long as the
maximum scanning time of PLC.
If PLC scanning time is extremely short (When at a factory set value of 10 ms as an example), the
SR Mini HG SYSTEM may detect the time-out not conducting normal communication processing.
The maximum scanning time of PLC differs depending on the CPU processing speed, I/O unit
configuration and the user program capacity of the PLC.